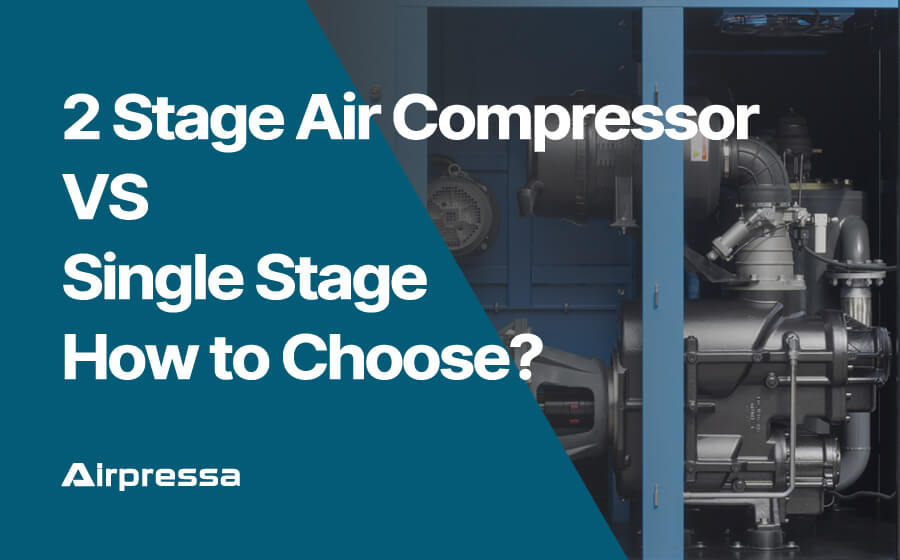
The two-stage air compressor is a type of compressor recognized for its durability and high performance, What is the difference between 2-stage air compressors and single-stage air compressors? How should I choose?
Now let’s dive in:
You can click on any section that you interest to get there quickly.
What is the 2-stage air compressor?
The 2-stage air compressor compress air in two stages or phases to reach a desired pressure level. In short, the 2-stage air compressor compress the air twice and output. It caters specifically to high-pressure applications where a single-stage compressor falls short.
2-stage air compressors are available in different forms, such as piston-type and rotary screw compressors, each offering its own advantages.
2-stage Air Compressor Working Principle
At its core, a 2-stage air compressor operates through a dual-stage compression process.
Let’s break it down:
Air Intake
The process begins with ambient air being sucked into the first-stage screw, also known as the low-pressure screw. It might interest you to know that rotary screw compressors rely on two interlocking helical screws, often referred to as rotors.
Initial Compression
Once inside, the air is compressed by the rotating action of these screws. This mechanical action reduces the space the air initially occupied, thereby increasing its pressure.
Intercooling
After undergoing initial compression, the air is not immediately transferred to the second stage.
It first goes through a vital midpoint called the intercooler. Acting like a pit stop, the intercooler performs the crucial task of cooling down the initially compressed air. It helps minimize the heat of compression.
This is a paramount measure as it helps in increasing efficiency and protects the compressor system from possible damage due to overheating.
Second Compression
Post-intercooling, the cooled compressed air is then led into the second stage, which is the high-pressure screw. Here, similar to the first screw stage, the air is compressed even more.
The second-stage compression significantly elevates the air pressure, readying it for final delivery.
Usually high-pressure air compressors, such as 30 bar(435 psi) and 40 bar(580 psi), are mostly two-stage air compressors or multi stage compressors.
Click to view Airpressa’s two-stage compressors
Key Features of 2-stage Air Compressor
Increased Pressure
The two-stage design allows for achieving higher pressures compared to single-stage compressors, making it suitable for demanding applications.
Intercooling
Cooling between the stages ensures that the compressed air doesn’t become excessively hot, contributing to smoother and more efficient operation.
Energy Efficiency
Despite the additional compression stage, 2-stage compressors are often more energy-efficient than their single-stage counterparts.
Applications
The versatility of the 2-stage air compressor makes it indispensable in various industries. It is particularly favored in scenarios where a continuous and elevated supply of compressed air is essential. Common applications include manufacturing, automotive, and other high-demand settings.
Two Stage Air Compressor vs Single Stage
Let’s delve deeper into the specifications and key distinctions between single-stage and two-stage screw air compressors in those categories.
Operating Principle
Single-Stage:
In a single-stage screw air compressor, the air is compressed once in one step. The intake air is drawn into the compressor, where the screw elements compress it and then send it to the air receiver or directly into the facility’s air network.
Two-Stage:
Differently, in a two-stage screw air compressor, the air is compressed twice. The initial compression occurs in the first-stage rotor, then it is cooled before entering the second stage for another round of compression.
Pressure
Single-Stage:
Single-stage compressors can typically deliver pressures up to about 150 PSI.
Two-Stage:
Two-stage compressors, with their double compression, can deliver pressures above 200 PSI, making them more suitable for high-pressure applications.
Airflow Volume
Single-Stage:
Generally, single-stage compressors deliver higher volumes of air because the entire volume of air is compressed at once.
Two-Stage:
In two-stage compressors, air volume can be slightly lower because it is split between two compression stages.
Efficiency
Single-Stage:
Single-stage compressors are less efficient as they generate more heat due to the quick compression process.
Two-Stage:
Two-stage compressors, with their intercooling phase, are more efficient, generating less heat per unit of compressed air.
Reliability
Single-Stage:
The reliability of single-stage compressors can be lower as they tend to generate more heat, leading to increased wear.
Two-Stage:
By distributing the workload over two compression stages and reducing heat generation, two-stage compressors can be more reliable and have longer service lives.
Cost
Single-Stage:
Single-stage compressors are usually cheaper due to their less complex design.
Two-Stage:
Two-stage compressors can be more expensive upfront because of their more complex architecture. However, their improved efficiency can lead to lower operating costs over time.
Maintenance
Single-Stage:
Owing to their simpler design, single-stage compressors may require less maintenance.
Two-Stage:
Although two-stage compressors may need more maintenance due to their more complex design, this is often offset by the increased longevity of their parts.
Application
Single-Stage:
Ideal for light to moderate-duty applications, such as tire inflation, powering air tools, and other less demanding tasks.
Two-Stage:
Perfectly suited for industrial applications needing a higher air pressure, such as manufacturing, heavy-duty workshops, or places where multiple high-pressure air tools are used simultaneously.
Please see the comparison table for a more visual comparison:
Feature | Single-Stage Air Compressor | Two-Stage Air Compressor |
Operating Principle | Compressed air once in a single step. | Compressed air twice with two compression stages. |
Pressure | Up to about 150 PSI. | Above 500 PSI, suitable for high-pressure applications. |
Airflow Volume | Higher volumes of air compressed at once. | Split between two compression stages, higher air volumes total |
Efficiency | Less efficient, generates more heat. | More efficient with intercooling, less heat per unit of compressed air. |
Reliability | Lower reliability due to increased heat generation. | Higher reliability with reduced heat generation and longer service life. |
Cost | Usually cheaper upfront due to a simpler design. | Higher purchasing cost, but lower operating costs over time. More energy-efficient |
Maintenance | Requires less maintenance due to a simpler design. | Air compression units require focused maintenance |
Application | Ideal for light to moderate-duty applications. | Suited for industrial applications requiring higher air pressure. |
In conclusion
Although single-stage air compressors might be more cost-effective initially and suitable for lighter applications, two-stage air compressors provide greater pressure, efficiency, and reliability for heavy-duty and industrial applications.
Therefore, the selection between the two should be based on the specific needs and demands of your operation.
Should I Choose the 2-stage Air Compressor?
Selecting between single-stage and two-stage compressors ultimately hinges on your specific needs.
High Pressure Needs
If your application requires pressure that exceeds 150 PSI, then a two-stage compressor is likely a better fit. It is designed to accommodate high-pressure operations, with some models delivering pressures over 200 PSI.
In this case, the selection might lean towards the two-stage compressor, even the multi stage compressor.
Continuous Heavy Duty Use
Two-stage air compressors are designed to handle more strenuous and continuous heavy-duty applications. They can work longer without overheating, reducing downtime and increasing productivity. If your operation involves running multiple high-pressure air tools simultaneously or depends heavily on compressed air.
Efficiency
Are you concerned about energy costs?
If yes, then you might want to consider a two-stage air compressor. It uses less power per unit of air delivered because of its intercooling stage between the two compression stages, which reduces the work of compression.
Longevity & Reliability
Due to the construction and how they operate, two-stage compressors typically enjoy a longer lifespan. They generate less heat, which reduces wear and tear.
Summary
If your air needs are light to moderate and budget is your primary concern, then single-stage compressors are a fair choice.
But if you handle heavy-duty, large scale operations, requiring higher pressures and efficiency, a two-stage compressor is worth considering despite the higher upfront costs.
Inverter Compressors VS Normal Compressors: Which is Better?
VSD compressors have become a game-changer in the quest for optimized performance and reduced energy consumption. As industries continue to prioritize sustainability and cost-effectiveness, the demand for inverter compressors continues to rise steadily.