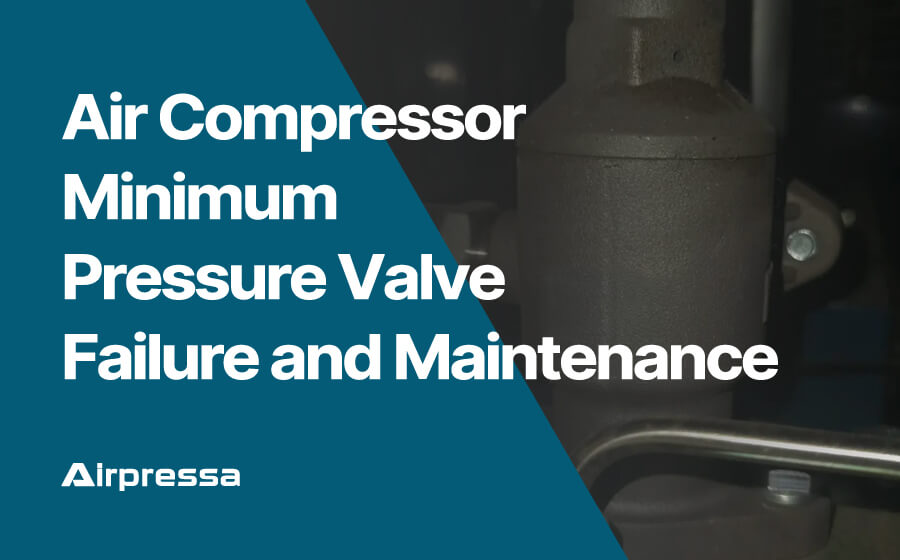
The minimum pressure valve is often overlooked but are actually very important component in an air compressor.
In the daily work of an air compressor, many failures may occur, among which minimum pressure valve failure is one of the common.
So, how should we determine the cause of the failure and how to solve it?
Let’s dive in.
You can click on any section that you interest to get there quickly.
- What is the Minimum Pressure Valve?
- How the Minimum Pressure Valve Works
- Structure of the Minimum Pressure Valve
- Main Functions of the Minimum Pressure Valve
- Common Symptoms of Minimum Pressure Valve Failure
- Minimum Pressure Valve Failure Causes in Screw Air Compressors
- Solutions for Minimum Pressure Valve Failure
What is the Minimum Pressure Valve?
The minimum pressure valve, also known as the minimum pressure check valve or the minimum pressure unloader valve, is a crucial valve in screw air compressors.
In essence, the minimum pressure valve acts as a safeguard, preventing the compressed air system from operating below the minimum pressure threshold, which could lead to performance issues or damage to equipment downstream of the compressor.
How the Minimum Pressure Valve Works
The working principle of the minimum pressure valve in an air compressor is straightforward:
When the pressure in the compressed air system drops below the preset minimum operating pressure, the minimum pressure valve opens, allowing air to flow through the valve into the system, thereby increasing the system’s pressure.
Once the pressure in the system reaches or exceeds the preset minimum operating pressure, the minimum pressure valve closes, halting the inflow of air into the system.
This mechanism ensures that the system’s pressure remains within the desired range.
Structure of the Minimum Pressure Valve
The structure of the minimum pressure valve typically comprises the following components:
Valve Body
The shape and size of the valve body depend on the design and application of the minimum pressure valve. It is usually made of pressure-resistant materials such as cast steel or stainless steel.
Valve Seat
The valve seat is part of the valve body and is typically connected to the inlet. It often features a circular or conical opening used to control the flow of gas.
Spring
The spring provides the pressure required to keep the valve seat closed. It is typically compressed and applied to the valve seat to maintain the closed state of the minimum pressure valve.
Diaphragm
The diaphragm serves to isolate the valve seat from the outlet. It is usually made of elastic material and can respond to changes in outlet pressure.
Adjustment Nut
The adjustment nut is used to adjust the preload force of the spring, thereby adjusting the opening pressure of the minimum pressure valve.
Outlet
The outlet is the port connected to the system pipeline through which gas can flow out.
Seal
The seal is used to ensure the valve’s sealing performance and prevent gas leakage.
These components constitute the basic structure of the minimum pressure valve. Specific designs and structures may vary depending on the application and system requirements.
The minimum pressure valve is commonly found in compressors with a capacity of 20 cubic feet or more. Despite its small size, this seemingly inconspicuous component can experience various faults that can affect the normal operation of the air compressor.
Main Functions of the Minimum Pressure Valve
Pressure Requirement for Opening the Valve
The minimum pressure valve typically requires a pressure of around 4 bar (in most cases) to open. This means that the valve opens when the pressure reaches this value, aiming to prevent rapid airflow.
Both excessive and insufficient airflow can hinder the normal operation of the compressor. By reducing the airflow rate, unnecessary faults can be avoided.
Regular Overload Protection
The minimum pressure valve serves as an internal safety valve in the compressor, unloading pressure when it reaches a set value, thus providing overload protection.
Prevention of Compressed Air Backflow
After the gas is delivered, if compressed air flows back, the minimum pressure valve acts as a check valve, preventing air from flowing back. If the minimum pressure valve fails to function during compressor unloading, air backflow may occur.
Therefore, when monitoring reveals gas backflow, the problem often lies with the minimum pressure valve.
Tip:
One crucial function of the minimum pressure valve is to lower the pressure in the cylinder, preventing excessive energy consumption due to high pressure.
Excessive pressure can also increase resistance, leading to electrical faults, misjudgments, increased current, and even shutdowns. This situation occurs when the valve of the minimum pressure valve fails to open, causing air blockage.
Common Symptoms of Minimum Pressure Valve Failure
Several common failures associated with the minimum pressure valve include:
Air Jetting
Air jetting issues primarily occur when the pressure within the system becomes too high. This could be due to blockages within the piping system, hindering the smooth flow of air.
Alternatively, malfunctioning pressure gauges may provide inaccurate readings, leading to incorrect pressure assessments.
As air pressure increases, the compressor adjusts its compression ratio accordingly, resulting in elevated internal pressure and air jetting.
Insufficient Lubricating Oil Pressure
When the minimum pressure valve malfunctions, it may fail to provide sufficient lubricating oil pressure to establish the necessary circulation pressure promptly.
This can result in increased wear in frictional areas, leading to abnormal noises in the compressor or causing excessive clearances between rotors, resulting in decreased gas production.
Faulty Minimum Pressure Valve During Unloading
If the minimum pressure valve fails to close securely during unloading, it can cause an increase in the pressure of the oil-gas separator, preventing complete separation of oil and gas and affecting the quality of compressed air.
Overload Shutdown
When the minimum pressure valve fails to open or experiences difficulty opening, it can lead to increased pressure within the oil separator, resulting in increased motor load and equipment overload shutdowns.
Additionally, if the minimum pressure valve becomes stuck, it can increase exhaust pressure, causing the operating current to overload and resulting in the shutdown of the screw air compressor. Shutdowns can cause compressed air within the piping system to flow back into the oil separator, leading to oil spray-back.
Minimum Pressure Valve Failure Causes in Screw Air Compressors
The minimum pressure valve can sometimes fail to close tightly, become damaged, or malfunction due to various reasons. Here are some common causes:
Poor Air Quality or Foreign Impurities Entering the Compressor
During the operation of a screw air compressor, poor air quality or external impurities entering the unit can impact the components of the minimum pressure valve.
These impurities, carried by the high-pressure airflow, can damage or contaminate the valve components, leading to its failure.
Excessive Oil Injection into the Air Compressor
Excessive oil injection into the air compressor can increase the viscosity of the lubricating oil. This makes it difficult for the valve plate to close or delays its opening, resulting in problems with the minimum pressure valve.
Large Fluctuations in Operating Conditions
The minimum pressure valve is set based on specific operating conditions. Large fluctuations in operating conditions can quickly lead to valve failure.
Extended Shutdown Followed by Restart
When a screw air compressor is restarted after a prolonged shutdown, moisture from the lubricating oil and air can enter the internal components of the equipment.
This accumulation of moisture can corrode various parts of the minimum pressure valve, leading to oil thickening and subsequent valve failure.
Solutions for Minimum Pressure Valve Failure
Preventive Measures
(1) Regularly clean the air filter to maintain cleanliness inside the compressor.
(2) Control the oil injection volume of the air compressor to maintain an appropriate level of lubricating oil.
(3) Stabilize operating conditions to avoid large fluctuations.
(4) Avoid prolonged shutdowns followed by restarts. If a shutdown is necessary, take measures to prevent moisture and lubricating oil from entering the internal components of the equipment.
Maintenance Measures
If a screw air compressor failure has occurred and there is a strong suspicion of a problem with the minimum pressure valve, the following steps can be taken to resolve it:
First, shut down the air compressor and disconnect the power to ensure that the equipment is safely turned off.
Next, locate the minimum pressure valve. It is usually located at the top of the oil-gas separator, and check for any malfunctions.
If the valve core or spring of the minimum pressure valve is faulty, replace the new components.
If there is no problem with the minimum pressure valve, the equipment can be overhauled, including cleaning and clearing, to ensure smooth and timely opening and closing of the valve.
Finally, restart the operation and observe whether the equipment is running normally. If the fault persists, it is recommended to replace the valve unless there are special circumstances.
It is important to note that before performing maintenance, ensure that the equipment is in a safe state, disconnect the power, and release the internal pressure to avoid accidents.
Explore Screw Air Compressor Valve Types: The Ultimate Guide
Unloader Valve
Check Valve
Minimum Pressure Valve
Oil Stop Valve
Temperature Control Valve
Solenoid Valve
Vent Valve
Capacity Regulating Valve
Drain Valve
Bypass Valve
Inverse Proportion Valve