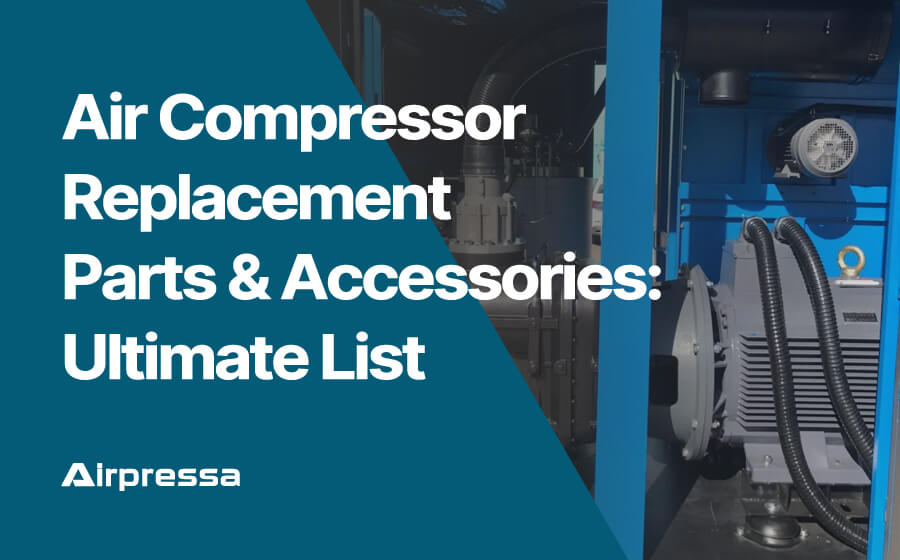
There are many types of air compresso replacement parts and accessories, their functions are also different. In addition to the main air compressor parts such as bearings, motors, and air ends, there are also various consumables that need to be replaced frequently.
Even an inconspicuous part can affect the working stability and air flow of the air compressor. This article mainly understands the consumables of the air compressor. Let’s dive in.
You can click on any section that you interest to get there quickly.
Air Compressor Oil Filter
The oil filter extends the compressor’s lifespan, lowers maintenance costs, and contributes to a harmonious and efficient industrial environment.
As a replacement part. air compressor oil filter is responsible for purging the compressor’s lubricating oil from contaminants that accumulate over time. As the oil circulates, it accumulates impurities, moisture, and debris that can hinder optimal operation. The oil filter captures these particles, ensuring that only clean and debris-free oil flows through the system.
With every circulation, the oil filter ensures that the lubricating oil retains its viscosity and purity. This not only enhances the compressor’s efficiency but also prevents excessive wear and tear on vital components.
Air Compressor Air Filter
In the realm of air compressors, the quality of air intake is paramount. This is where the air compressor air filter steps into the limelight, serving as the first line of defense against airborne contaminants.
The air filter ensures that the air drawn into the compressor is free from dust, debris, and foreign particles that could compromise its performance.
The air filter’s significance is not limited to safeguarding the compressor; it also plays a vital role in maintaining the overall air quality of the operation environment. Clean and filtered air prevents abrasive particles from infiltrating the compressor’s inner workings, preventing wear and tear and minimizing maintenance requirements.
In addition, the air filter contributes to the longevity of downstream equipment, ensuring that the air produced by the compressor is of impeccable quality.
In a scenario where air compressors are utilized in sensitive applications, such as medical facilities or laboratories, the air compressor air filter’s role becomes even more critical. It helps maintain the sterility and precision of processes, highlighting the filter’s impact beyond the mechanical realm.
Oil Separator Element
As compressed air undergoes the compression process, it carries traces of lubricating oil that have seeped into the air stream.
The oil separator’s pivotal function revolves around the separation of oil from compressed air, ensuring that the compressed air remains clean and devoid of contaminants. This process not only enhances the quality of the compressed air but also prevents oil buildup in downstream equipment.
By maintaining the purity of the compressed air, these elements contribute to the longevity and optimal functioning of the entire industrial ecosystem.
Lubricating Oil
The lubricating oil ensures the air compressor components move with synchronicity and minimal friction.
The role of the lubricating oil is multi-faceted, ranging from minimizing wear and tear to dispersing heat generated during compression.
And it also forms a protective film over crucial parts, reducing friction and preventing overheating that could otherwise hinder the compressor’s performance.
Beyond the boundaries of friction reduction, the lubricating oil plays a critical role in sealing and maintaining the compression chamber’s integrity. It safeguards the components against the rigors of compression, extending their lifespan and contributing to the compressor’s consistent efficiency.
Belt
Unlike direct air compressors, belt air compressors require a belt to drive. As the belt wraps around the pulleys, it drives the compressor’s pistons and other vital components, propelling the entire system towards peak performance.
What are different on direct air compressor with belt drive? You can check this article: Direct Drive Air Compressors Vs Belt Drive Air Compressors
Among the ensemble of belt dreive air compressor replacement parts, the belt is the most vulnerable parts that need attention. Its function, although seemingly straightforward, is instrumental in translating the energy from the motor to the compressor’s moving parts. The belt’s design and tension facilitate the seamless transfer of rotational force, ensuring the synchronized movement of components.
Gasket
In the intricate of air compressors, the gasket is one of the essential factors to ensure the air tightness of the whole machine.
Its primary function revolves around sealing critical junctures, preventing the leakage of air or fluids. The gasket’s design and material composition ensure that connections between components remain impervious to external factors.
The gasket seals the gaps between mating surfaces, such as cylinder heads and valve plates. This airtight seal not only maintains the compressor’s efficiency but also safeguards against potential leaks that could compromise the system’s operation. The gasket, in its unassuming role, upholds the integrity of the air compressor’s architecture, allowing it to function flawlessly.
O-Rings
O-Rings, also known as toric joints, are essential Sealing Elements within an air compressor.
These small circular rings are typically made from rubber or other elastomers. Their primary function is to create a reliable and airtight seal between different components, preventing leaks and ensuring the proper functioning of the compressor. By maintaining a secure seal, O-Rings contribute to the overall efficiency and safety of the air compressor, allowing it to perform optimally during continuous use.
Valves
Valves are fundamental components that oversee the flow of gases within an air compressor. They act as gatekeepers, regulating the movement of compressed air at various stages of the compression process. Valves play a pivotal role in ensuring that the compressed air flows smoothly, without disruptions or fluctuations.
These vital components come in various types, including intake valves, discharge valves, and safety valves.
Intake valves control the entry of ambient air into the compression chamber, while discharge valves manage the release of compressed air.
On the other hand, safety valves act as fail-safes, preventing the compressor from over-pressurizing and ensuring the safety of the equipment and operators.
Explore Screw Air Compressor Valve Types: The Ultimate Guide
There are many types of air compressor valves, each with their own unique and indispensable functions. They Together form the air compressor valve system, allowing it to operate safely and stably.
This article highlights the 11 main air compressor valve types.
Seals
Seals are indispensable elements that serve as barriers against leaks and contamination. These unassuming components are designed to create a secure and airtight enclosure within the compressor system. Their primary function is to prevent the escape of pressurized air, gases, or liquids from critical joints or openings.
Seals ensuring that the internal components of the compressor remain isolated from external elements. By maintaining a tight seal, they contribute to the overall efficiency and safety of the compressor, minimizing energy loss and preventing potential hazards.
Coolant
Coolant circulates through various components, dissipating heat generated during compression and preventing the system from overheating. It absorbs excess heat and releases it through a cooling process, maintaining optimal operating temperatures.
By preventing excessive heat buildup, they contribute to the durability and efficiency of the compressor, ensuring consistent performance even during continuous use.
Drain Valves
Drain valves ensure that the system remains free from excess moisture. They serve a fundamental role in maintaining the overall health of an air compressor system.
Their primary function revolves around fluid management, particularly the removal of accumulated condensate and moisture. The relentless compression process results in the buildup of excess moisture, which, if left unchecked, can lead to corrosion, reduced efficiency, and even mechanical failure.
By periodically releasing accumulated condensate, these valves help prevent potential damage and prolong the lifespan of the air compressor.
Pressure Gauge
As the eyes that monitor the internal dynamics of an air compressor, Pressure gauges primary function revolves around measuring and displaying the pressure levels within the system.
Pressure gauges are the operators’ window into the heart of the machine. This real-time and accurate pressure readings offers valuable insights into the compressor’s performance, enabling operators to gauge its efficiency and make informed adjustments when necessary.
Sensors
Sensors revolve around detecting various parameters, including temperature, vibration, and fluid levels. These sensors translate physical phenomena into electrical signals, which are then processed to provide critical data for system control and monitoring.
The versatility of sensors enables them to be tailored to different aspects of compressor operation. Whether it’s safeguarding against overheating or preventing system malfunctions, sensors contribute to the overall stability and reliability of the compressor. Their ability to promptly detect anomalies allows for swift responses, ensuring uninterrupted operation and minimizing downtime.
Article at the end
Especially for heavy industrial air compressors, there are countless large and small parts. They all play an irreplaceable role in the compressor work.
For these air compressor replacement parts & accessories, regular inspection and replacement are required to ensure the stable operation of the air compressor.
The Ultimate List: Screw Air Compressor Parts Name
The screw air compressor is a complex machine with many parts that work together to produce compressed air. Each part plays a crucial role in the overall performance and efficiency of the compressor.
In addition to the replaceable parts mentioned in this article, there are also very important core working accessories, such as air ends, bearings, control systems, motors, etc.