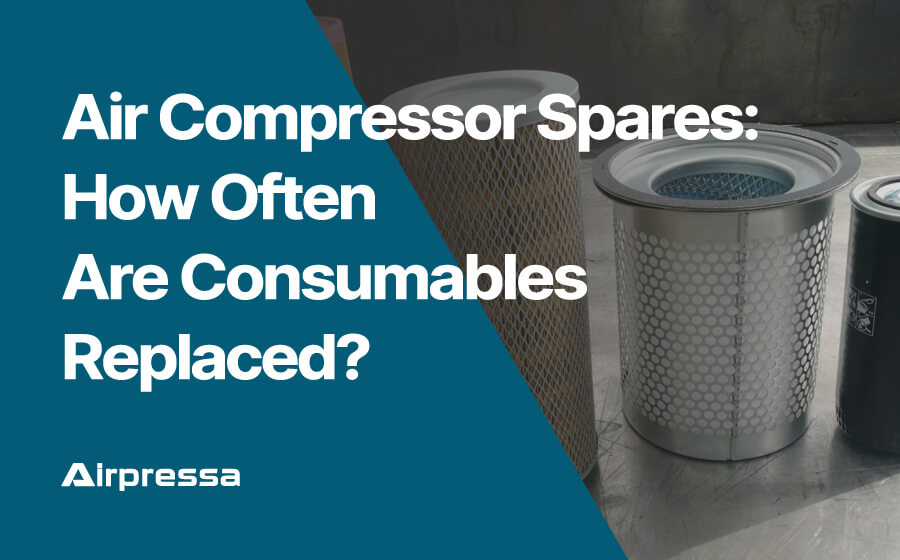
Air compressor spares include more than dozens of parts. In this article, we mainly discuss consumables that need to be replaced regularly, including the following:
You can click on any section that you interest to get there quickly.
Compressor Air Filter
Commonly known as pre-filter or air intake filter.
The air compressor air filter is the most common air compressor spare part. It operats within a sophisticated system, the air filter plays a pivotal role in maintaining the quality of the air that enters the compressor, ultimately influencing its overall performance.
Function and Operation
The primary function of the air compressor air filter is to ensure the purity of the air that enters the compressor. This is achieved through a two-fold process: filtration and separation.
As ambient air is drawn into the compressor, the air filter acts as a barrier, capturing contaminants such as dust, dirt, and debris suspended in the air.
The operation of the air filter involves a multi-layered media or element that traps particles of various sizes. This prevents them from entering the compressor’s internal components, safeguarding against potential damage and wear.
In essence, the air filter acts as a gatekeeper, permitting only clean and filtered air to proceed into the compressor’s chambers.
Replacement Cycle
The replacement interval typically depends on factors such as the compressor’s usage frequency, operating environment, and the manufacturer’s recommendations. Regular replacement is recommended to ensure consistent and effective filtration.
Based on our 20 years of industry experience, here are some suggestions:
- Replace the air filter every 1500-2000 hours of operation of the air compressor
- In a dusty environment, replace it every 4 to 6 months
Consequences of Delayed Replacement
Neglecting the timely replacement of the air filter can lead to several adverse effects on the compressor’s performance. The accumulation of contaminants within the filter can lead to decreased airflow, causing the compressor to work harder to draw air.
This can result in increased energy consumption, reduced efficiency, and potential overheating of the compressor’s motor.
Furthermore, inadequate filtration can allow contaminants to enter the compressor, leading to potential damage to internal components. Excessive wear, increased friction, and compromised performance are among the possible consequences.
Prolonged use of a clogged air filter can strain the compressor, potentially shortening its overall lifespan.
Air Compressor Oil Filter
As an integral component within an air compressor, the air compressor oil filter plays a critical role in maintaining the overall efficiency and longevity of the equipment. Operating within a complex system, the oil filter can ensure the purity and quality of the lubricating oil that circulates through the compressor.
Function and Operation
The air compressor oil filter is designed with the primary function of removing contaminants, impurities, and particulates from the lubricating oil. This process is vital as it prevents these harmful particles from circulating within the compressor’s internal components, safeguarding them against premature wear and damage.
The filter’s operation involves the oil passing through a fine mesh or porous material, which captures debris and contaminants. The clean oil is then allowed to continue its journey through the compressor, promoting smooth and friction-free operation.
Replacement Cycle
The replacement cycle of the air compressor oil filter is a crucial consideration in maintaining optimal compressor performance. Typically, the replacement interval is determined by the manufacturer’s recommendations and the operating conditions of the compressor.
These intervals can vary, we will give our distributors and users the following suggestions:
- After the first 500 hours of operation of the air compressor, replace the oil filter
- After that, the air compressor should be replaced every 2000 hours or so
- In a humid and dusty environment, please shorten the time
Consequences of Delayed Replacement
If the air compressor oil filter is not replaced within the recommended interval, the consequences can be significant.
The accumulation of contaminants in the lubricating oil can result in compromised lubrication of critical components. This can lead to increased friction, heat generation, and accelerated wear, ultimately shortening the compressor’s lifespan.
Additionally, contaminated oil can negatively impact the compressor’s energy efficiency, leading to increased energy consumption and operational costs.
A clogged or inefficient oil filter can strain the compressor’s motor and other components, potentially causing them to overheat or fail prematurely. These will increase energy consumption, and potentially lead to costly repairs.
Oil Separator Element
In the intricate landscape of air compressor components, the oil separator element ensures the separation of oil from compressed air, safeguarding the integrity of the air compressor’s operation.
Function and Operation
The primary function of the oil separator element is to remove oil aerosols and vapors from the compressed air before it leaves the compressor’s discharge.
The oil & gas separator element is constructed with a specialized media, capitalizes on the differences in density between the air and oil, to allows air to pass through while capturing and coalescing oil droplets.
The operation of the oil separator element involves a multistage process. As compressed air enters the separator, it encounters the media designed to trap oil particles.
These particles gradually coalesce into larger droplets, which then gravitate down the separator element and collect at the bottom, where they are drained off. This ensures that only oil-free compressed air proceeds to downstream processes or applications.
Replacement Cycle
The replacement cycle of the oil separator element is a critical aspect of air compressor maintenance. The recommended replacement interval varies based on factors such as compressor usage, environmental conditions, and manufacturer guidelines.
Regular replacement is essential to prevent the buildup of oil and contaminants within the element.
The service life of the oil-gas separator is mainly determined by the quality of the filter element and the use environment, usually 4000-8000 hours. The harsher the environment, the shorter the service life.
Consequences of Delayed Replacement
Over time, a saturated element will struggle to effectively separate oil from the compressed air, leading to an increased oil carryover into the downstream air network.
This can contaminate the air supply, cause malfunctions in connected equipment, and even lead to decreased overall efficiency.
Additionally, oil carryover can lead to deposits in downstream equipment, affecting their performance and necessitating costly maintenance.
Long-term neglect of the oil separator element’s replacement can result in reduced compressor efficiency, increased energy consumption, and potential damage to other system components.
The lack of proper oil separation can lead to increased wear on equipment, decreased product quality, and higher maintenance costs.
Air Compressor Lubricating Oil
In oil-lubricated air compressors, lubricating oil is an essential consumable. It can facilitate the smooth movement of various parts while safeguarding against friction-induced wear and tear.
Function
The air compressor lubricating oil acts as a protective barrier, preventing metal-to-metal contact between the moving parts within the compressor.
Its primary function is to reduce friction, dissipate heat generated by mechanical interaction, and provide a sealing effect to prevent gas leakage.
As the compressor’s moving parts engage, a thin layer of oil is formed on their surfaces. This layer acts as a cushion, absorbing the forces generated during operation and minimizing wear.
Simultaneously, the oil carries away excess heat, preventing overheating and ensuring optimal performance.
Replacement Cycle
The replacement cycle of air compressor lubricating oil varies depending on factors such as compressor type, usage intensity, environmental conditions, and oil quality.
Again, here are some suggestions:
- Change the engine oil within 500 hours of the first operation of the air compressor
- Should be replaced lubricating oil every 4000 hours or so
- In addition, in some special industries and environments, if the air contains acidity, alkalinity and gas, please replace in advance
Consequences of Delayed Replacement
As the oil’s lubricating properties wane, friction between components escalates, resulting in accelerated wear and tear. This can lead to compromised compressor efficiency, increased energy consumption, and even catastrophic failures in extreme cases.
Furthermore, ineffective lubrication can lead to increased heat generation, causing thermal stress on components. This can degrade the integrity of critical parts, leading to decreased performance and unexpected downtime.
Contaminants and debris in aged lubricating oil can also infiltrate the compressor’s internal mechanisms, further exacerbating potential issues.
In Conclusion
These air compressor spares play a pivotal role in maintaining the efficient operation and longevity of air compressor systems.
From the air filter’s function in ensuring clean air intake to the oil filter’s role in safeguarding against contaminants, each component has a specific purpose.
The oil separator element, meanwhile, prevents oil carryover, safeguarding both efficiency and environmental concerns.
The lubricating oil acts as the lifeblood, reducing friction and heat while requiring timely replacement to avoid air flow reducing.
Air Compressor Replacement Parts & Accessories: Ultimate List
In addition to these air compressor spare that need to be replaced regularly, there are also many other replacement parts in an air compressor that may be replaced due to wear and tear.