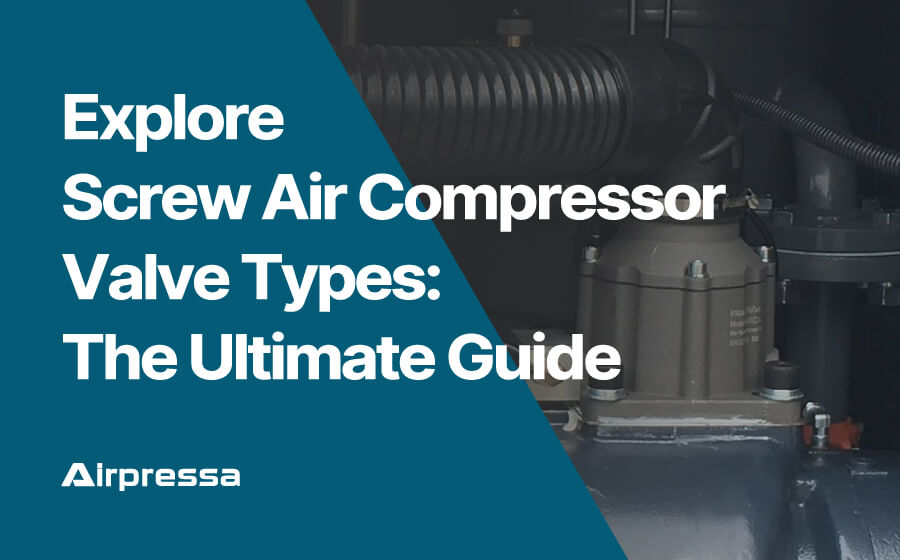
There are many types of air compressor valves, each with their own unique and indispensable functions. They Together form the air compressor valve system, allowing it to operate safely and stably.
This article highlights the 11 main air compressor valve types. How do they work?
Let’s dive in.
You can click on any section that you interest to get there quickly.
Air Compressor Unloader Valve
What is the Air Compressor Unloader Valve?
The unloader valve is a vital component of an air compressor system, also known as intake valve. It’s primarily responsible for providing a path for the pressurized air to escape when the compressor is not in operation.
The unloader valve is the most important type of air compressor. It’s typically part of the pressure switch assembly, ‘unload’ or release the air pressure from the compressor pump to the outlet tube.
Function of the Unloader Valve
The function of the unloader valve is twofold.
Firstly, when the pressure reaches the preset maximum limit in the pressure switch, the unloader valve opens to let out the accumulated pressurized air, effectively stopping the build-up.
Secondly, the unloader valve facilitates a smoother startup by creating a no-load condition, allowing the motor to restart without having to fight the initial resistance from pressurized air.
How Does the Air Compressor Unloader Valve Work?
The unloader valve responds to the pressure changes inside the compressor’s storage tank.
When the tank pressure reaches the maximum preset pressure, the pressure switch flips a small lever on the switch, which triggers the unloader valve to open and vent the pressurized air.
Conversely, when the pressure in the tank drops below the minimum preset pressure, the pressure switch triggers the unloader valve to close, halting the airflow, and allowing pressure to again build up inside the compressor.
Consequences of a Malfunctioning Air Compressor Unloader Valve
A malfunctioning unloader valve can pose several issues. These include:
Difficulty in Starting
An air compressor with a faulty unloader valve can struggle to start due to the resistance from the pressurized air.
Motor Overload
Without proper functioning of the unloader valve, the motor will be under constant strain, potentially leading to overheating or tripping of motor protection devices.
Reduced Compressor Efficiency
If the valve sticks in the open position, pressurized air will continuously escape, resulting in reduced efficiency.
Air Compressor Check Valve
What is an Air Compressor Check Valve?
The air compressor check valve is a non-return valve that allows pressurized air to flow from the pump to the tank in an air compressor system, and prevents it from flowing back from the tank to the pump.
Function of the Check Valve
The primary function of a check valve is to direct the flow of pressurized air in one direction: from the compressor pump to the air storage tank. This allows the compressor to build up a reserve of pressurized air for use when needed.
How Does the Air Compressor Check Valve Work?
When the compressor pump is running and generating pressurized air, this air pushes the check valve open, allowing the air to flow into the storage tank.
When the pump stops, the rise in pressure on the tank side (compared to the pump side) closes the check valve, keeping the pressurized air in the tank and preventing it from moving back to the pump.
Consequences of a Malfunctioning Air Compressor Check Valve
The malfunction of a check valve can lead to several issues:
Backflow of Air
If the check valve fails to close properly, pressurized air could flow back from the tank into the pump. This could cause the motor to struggle to start or overload because it would be working against pressure.
Leakages
A faulty check valve could lead to air leakages, resulting in loss of pressure and reduced compressor efficiency.
Damage to the Pump or Motor
In serious cases, the backflow of air might lead to damage in the pump, or overloading and potential overheating of the electric motor, if it’s unable to start against pressure.
Air Compressor Minimum Pressure Valve
What is the Air Compressor Minimum Pressure Valve?
The minimum pressure aalve is a check valve that ensures minimum pressure in the internal system of the air compressor. It is one of the moset important air compressor valve type.
Function of the Minimum Pressure Valve
Primarily, it ensures the system maintains a minimum operating pressure to lubricate the air compressor and stabilize the compressor output.
It prevents the system pressure from dropping below a minimum threshold, protecting sensitive components from possible damage due to low pressure and ensuring the lubricating oil’s proper function. Additionally, it separates the oil and air mixture.
How Does the Minimum Pressure Valve Work?
When the system is not generating minimum pressure, the minimum pressure valve stays closed, effectively becoming a barrier between the oil circulation system and the compressed air reservoir.
When the compressor reaches the necessary pressure, the minimum pressure valve opens, allowing the mixed air and oil to enter the separator.
Thus, the minimum pressure valve becomes operational, ensuring that the air compressor’s pressure stays within a specific minimum range facilitating proper lubrication and separation of the oil-air mixture.
Consequences of a Malfunctioning Minimum Pressure Valve
The effects of a malfunctioning minimum pressure valve often include:
Inefficient Lubrication
If the valve fails and the system can’t maintain minimum pressure, the air compressor may not be properly lubricated. This can accelerate wear and tear on various components and potentially result in premature failure of the air compressor.
Poor Separation of Oil and Air
If the valve does not open correctly, the oil/air mixture may not be separated properly, which could lead to oil in the air line, degrading the quality of compressed air delivered by the system.
Pressure Fluctuations
A faulty minimum pressure valve can result in pressure fluctuations, causing an unstable output and potentially affecting the performance of any tools or processes using the compressed air.
Air Compressor Oil Stop Valve
What is the Air Compressor Oil Stop Valve?
The oil stop valve in an air compressor, also known as oil check valve or oil return valve, is an important component found in the oil circulation system of an oil-injected rotary screw compressor.
Function of the Oil Stop Valve
Primarily, the function of the oil stop valve is to control the flow of oil within the compressor.
When the compressor stops, it prevents the oil from flowing back or draining into the compressor elements, ensuring that there is always a necessary amount of oil in the system for lubrication, cooling, and sealing purposes when the air compressor starts again.
How Does the Air Compressor Oil Stop Valve Work?
The operation of the oil stop valve largely depends on the pressure changes within the compressor.
When the compressor is operational and generating pressure, this valve opens, allowing the oil to circulate. The compressor ceases to function and there’s no pressure being built up, the valve closes, stopping the backflow of oil into the compressor elements.
Consequences of a Malfunctioning Oil Stop Valve
Should the oil stop valve malfunction, it can lead to serious repercussions such as:
Insufficient Lubrication
Without a properly functioning valve, the lubrication process can be hindered, inducing undue wear and tear, heat generation, and inefficiency.
Difficulty in Starting
If the valve fails to hold the oil in place during a stop, the compressor may have to start dry, leading to difficulty in starting, potential damage, and reduced lifetime of the compressor components.
Air Compressor Temperature Control Valve
What is the Air Compressor Temperature Control Valve?
The temperature control valve, also known as a thermostat valve, typically found in oil-cooled rotary screw compressors.
Function of the Temperature Control Valve
The temperature control valve modulates the running temperature within the compressor, aiming to keep it within a specified safe range. It determines how much cooling oil to circulate based on the temperature of the compressor, therefore preventing overheating and ensuring optimal and efficient operation of the compressor.
How Does the Air Compressor Temperature Control Valve Work?
This valve regulates the amount of oil flowing through the cooler based on the air-end discharge temperature.
In colder start-up conditions, it curtails the flow of oil going to the cooler, allowing the compressor to warm up to its efficient operational temperature swiftly. When the compressor reaches the desired operating temperature, the valve permits more oil to the cooler to maintain steady temperature levels and prevent overheating.
Consequences of a Malfunctioning Temperature Control Valve
If the temperature control valve fails, it can lead to serious problems:
Overheating
A stuck or malfunctioning valve that doesn’t open when necessary can cause the compressor to overheat, risking severe damage to the compressor system.
Inefficient Operation
If the valve doesn’t regulate the oil flow efficiently, the compressor might operate at temperatures less optimal for its performance, leading to inefficiency.
Air Compressor Solenoid Valve
What is an Air Compressor Solenoid Valve?
A solenoid valve is an electromagnetic device used to control the flow of air or other gases within the air compressor system.
Function of the Solenoid Valve
Solenoid valves primarily serve to control the pneumatic functions within an air compressor. They control the start and stop of the airflow and also regulate the direction of the airflow.
How Does the Air Compressor Solenoid Valve Work?
The solenoid valve operates through an electric coil.
When the coil is powered, it generates a magnetic field which moves a plunger inside the valve, thereby opening or closing the valve.
When the electrical power is shut off, a spring returns the plunger to its original position, reversing the action of the valve.
Consequences of a Malfunctioning Solenoid Valve
A malfunctioning solenoid valve could lead to several issues:
Flow Disruptions
Disruptions in airflow could cause uneven pressure management and inconsistent functioning of the compressor.
System Shutdown
In extreme cases, a faulty solenoid valve might cause the whole air compressor system to stop functioning due to uncontrolled airflow.
Air Compressor Vent Valve
What is the Air Compressor Vent Valve?
The vent valve, often found in larger air compressors, is a mechanism installed to ensure the controlled release of air or gas from the system.
Function of the Vent Valve
The principal function of a vent valve is to control the discharge of air from the compressed air system. It helps to relieve the pressure when needed, thereby assisting in maintaining a balanced operational environment within the compressor system.
How Does the Air Compressor Vent Valve Work?
The vent valve works in a straightforward fashion. When the pressure within the compressor system reaches a specified level or when there’s a need to depressurize the system (like for maintenance purposes), the vent valve is manually or automatically opened to allow the compressed air to escape.
This action aids in reducing the pressure inside the compressor in a safe and controlled manner.
Consequences of a Malfunctioning Vent Valve
A faulty vent valve could trigger several problems:
Pressure Accumulation
A malfunctioning valve may not open when it’s supposed to, leading to an unsafe buildup of pressure within the compressor system.
System Damage
Excessive pressure can cause damage to other components within the compressor and potentially lead to a costly system breakdown.
Air Compressor Capacity Regulating Valve
What is the Air Compressor Capacity Regulating Valve?
The capacity regulating valve is a valve which controls the compressor’s output based on the demand of the air system.
Function of the Capacity Regulating Valve
The primary function of the capacity regulating valve is to adjust the quantity of air being drawn into the compressor during each cycle. This process effectively controls the compressor’s output to match the consumption rate of the compressed air system, ensuring energy-efficient operation.
How Does the Air Compressor Capacity Regulating Valve Work?
The capacity regulating valve operates by altering the compressor’s load.
When the air receiver’s pressure reaches the maximum set point, the capacity regulating valve partially closes, limiting the volume of air that the compressor can intake.
Conversely, when the air receiver’s pressure drops to the minimum set point, the capacity regulating valve opens to allow full air intake, hence restoring the compressor’s full output.
Consequences of a Malfunctioning Capacity Regulating Valve
If the capacity regulating valve malfunctions, several problems can occur:
Inefficient Operation
A faulty valve may not accurately regulate the compressor’s load, leading to inefficiencies and higher energy consumption.
System Instability
Inconsistent pressure due to a malfunctioning valve could lead to an unstable compressed air system, negatively impacting overall operational performance.
Air Compressor Drain Valve
What is an Air Compressor Drain Valve?
A drain valve is a simple yet important part of any air compressor system. Positioned typically at the bottom of the system’s receiver tank, its design is built to discharge any moisture or other forms of condensation that accumulate during compressor operation.
Function of the Drain Valve
The fundamental role of a drain valve is to allow the expulsion of accumulated water and other condensates from the receiver tank. This maintenance process prevents corrosion and ensures the overall health of the air compressor system.
How Does the Air Compressor Drain Valve Work?
The operating mechanism of a drain valve is relatively simple. During or after compressor operation, as condensates collect at the bottom of the receiver tank, the drain valve is manually (in some cases automatically) opened.
This action lets out the accumulated moisture, ensuring that no water remains inside the tank to cause potential corrosion damage.
Consequences of a Malfunctioning Drain Valve
A malfunctioning drain valve can lead to complications such as:
Tank Corrosion
Water accumulation in the tank could promote rust and corrosion, diminishing the lifespan of the system.
System Health
An ineffectively drained system harbors the risk of transferred moisture to the air lines, potentially damaging other components of the air system.
Air Compressor Bypass Valve
What is the Air Compressor Bypass Valve?
A bypass valve, also known as a diverting valve, is an essential component in certain air compressor systems. It is prominently featured in compressor systems where a constant pressure level needs to be maintained.
Function of the Bypass Valve
The bypass valve’s primary role is to maintain steady pressure within the compressor system regardless of the system’s load demand. It achieves this function by redirecting excess compressed air either back to the inlet or to the atmosphere, depending on the design and requirement of the system.
Working of an Air Compressor Bypass Valve
The operation of a bypass valve is closely linked with the compressor’s regulation system.
When the compressed air’s pressure exceeds the required level, the valve opens to redirect the surplus air. This regulation process ensures a steady output pressure from the compressor, irrespective of the changes in load demand.
Consequences of a Malfunctioning Bypass Valve
Faulty bypass valves can cause various issues:
Pressure Fluctuation
An improperly functioning bypass valve can result in fluctuating pressure levels, negatively impacting the stability and efficiency of the compressor system.
Damage to System
Prolonged exposure to unstable pressure could risk damage to the compressor, and other components within the system, leading to potential breakdowns and costly repairs.
Air Compressor Inverse Proportion Valve
What is an Air Compressor Inverse Proportion Valve?
The inverse proportion valve is particularly implemented in systems that require precise control over air pressure. It is not a necessary component for every rotary screw compressor.
Function of the Inverse Proportion Valve
The inverse proportion valve operates to regulate pressure within the air compressor system, maintaining stability. It plays a central role in adjusting the air pressure as per the system’s requirement.
How Does the Air Compressor Inverse Proportion Valve Work?
The inverse proportion valve works in reverse connection to the air pressure.
As the air pressure increases, the valve opening decreases, reducing the air flow, and vice versa. The valve continuously adjusts its position, responding to changes in system pressure to maintain a stable output.
How to Maintain These Types of Air Compressor Valve?
All air compressor valves play an important role in the operation of the entire equipment. Maintenance of valves should be a routine task.
- Regularly inspect the valve for signs of wear, tear, or blockages.
- Clean the valve periodically to prevent debris accumulation.
- Check the air compressor operational efficiency; if it’s not opening or closing properly at the required pressure points, there might be a need for repair or replacement.
Remember, adherence to the manufacturer’s guidelines helps to prolong the valve’s lifespan and the overall efficiency of a screw air compressor.
Why Is The Air Compressor Oil Water Separator Clogged?
The air compressor oil water separator plays an important role in the compression process of air. It ensures that oil, water and other harmful substances do not end up in the compressed air system and pipe.
It consists of many parts, but each has its own unique and indispensable role. When the oil water separator get clogged, you could be in big trouble.