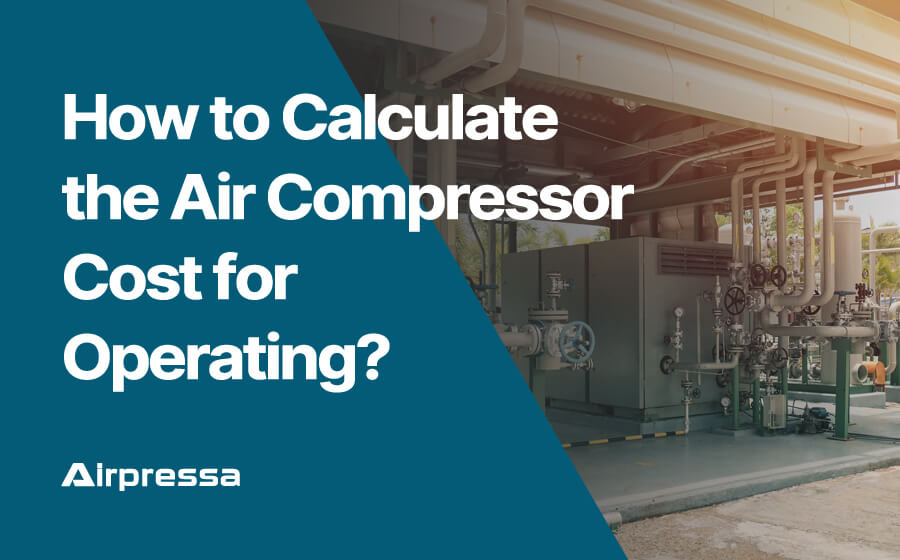
There are many aspects to the air compressor cost, not just the product itself.
Usually, the air compressor works as the core of an compressed air system. So, it is necessary to save corporate funds by understanding these cost components and optimizing them.
We can start from these aspects:
You can click on any section that you interest to get there quickly.
Purchase Cost of Air Compressors
Purchase Cost of Air Compressor: The initial investment includes the cost of the air compressor unit itself. Prices can vary significantly based on the type, size, and brand of the compressor you choose.
Air Dryer: If your application requires compressed air with low moisture levels, you may need an air dryer. Consider the cost of this additional equipment when calculating your expenses.
Air Tank: An air tank can help stabilize pressure fluctuations and reduce the load on the compressor. Include the cost of the air tank if you decide to use one.
Air Filter System: Ensuring the quality of compressed air is crucial. Factor in the cost of an air filter system, which may include compressed air filters, an auto water drain system, and piping to maintain clean and dry compressed air.
Packaging and Shipping Costs
Beyond the purchase costs we’ve discussed earlier, it’s essential to consider expenses related to packaging and shipping. These costs can vary significantly depending on several factors:
Wooden Box Packaging
Ensuring that your air compressor is well-packaged for transportation is crucial to prevent any damage during transit. Wooden boxes are commonly used for this purpose. Calculate the cost of the wooden box or packaging materials.
Sea Freight
If the air compressor is being imported or exported internationally, sea freight charges will apply. These costs depend on factors like the weight and volume of the shipment, the shipping route, and the chosen carrier.
Transportation to Your Warehouse
You need to consider the cost of transporting it to warehouse from the nearest port. This can include inland transportation costs, such as trucking.
Properly accounting for packaging and shipping costs is essential for budgeting and understanding the total expenses associated with acquiring and operating an air compressor.
These costs can vary widely depending on your location, the supplier’s location, and the specific logistical requirements of your air compressor purchase. By factoring them into your calculations, you’ll have a more accurate estimate of the total cost of ownership for your air compressor.
Labor Costs
Calculating the operating cost of an air compressor also requires considering labor costs associated with both installation and operation.
Especially centrifuges and large industrial screw air compressors usually require professionals to install, operate, and maintain. In order to facilitate the more stable and efficient operation of the compressed air system.
Installation Costs
When installing an air compressor, you’ll likely need skilled technicians who can handle the electrical and mechanical aspects of the installation.
These technicians may need to assemble and position the compressor, connect electrical components, and ensure that it operates correctly.
The cost of hiring these professionals should be factored in.
Operational Labor Costs
Operating an air compressor requires personnel to monitor and manage its performance. Operators are responsible for starting and stopping the compressor, adjusting settings as needed, and performing routine maintenance tasks.
The labor cost associated with these operators, including salaries and benefits, should be considered.
It’s important to note that labor costs can vary widely depending on location, skill levels required, and the complexity of the installation and operation.
Additionally, operational labor costs can be ongoing expenses that should be accounted for in your long-term budget.
By including labor costs in your calculation of air compressor operating costs, you’ll have a more accurate understanding of the financial implications of owning and using this essential equipment.
Air Compressor Maintenance cost
Proper maintenance ensures the longevity and efficiency of your compressor. However, the air compressor replacement cost is also a figure that cannot be ignored.
Air Filter Maintenance
Importance
The air filter in a screw air compressor plays a pivotal role in the air intake process. Its primary function is to filter out impurities and dust from the ambient air that enters the compressor. This filtration is vital to ensure the smooth and efficient operation of the screw air compressor.
Cost Implications
Neglecting air filter maintenance can lead to increased energy consumption, reduced efficiency, and even equipment damage. Regular inspection, cleaning, and replacement of air filters are essential maintenance tasks.
Oil Filter Maintenance
Importance
Oil filters, usually made of paper, are responsible for removing impurities from the compressor’s lubricating oil. These impurities can include metal particles and oil degradation products. The filtration accuracy typically ranges from 5 microns to 10 microns. Effective oil filtration is critical to protect bearings and rotors.
Cost Implications
Failure to maintain the oil filter can result in contaminated oil, leading to accelerated wear and tear on mechanical components. Regular oil filter replacement is necessary to prevent costly repairs.
Oil Separator Maintenance
Importance
The oil separator is a vital component of a screw air compressor. Its primary function is to separate gas from liquid and extract oil from the compressed air.
Cost Implications
A malfunctioning oil separator can lead to increased oil carryover in the compressed air, causing damage to downstream equipment. Regular inspection and maintenance of the oil separator are essential to prevent such issues.
Lubricating Oil
Importance
Screw air compressors rely on lubricating oil to reduce friction and wear between mechanical parts. Proper lubrication is critical for the compressor’s reliability and longevity.
Cost Implications
Inadequate or deteriorating lubricating oil can result in excessive wear, reduced efficiency, and potential equipment breakdowns. Regular monitoring of oil levels and quality, along with scheduled oil changes, is essential.
In summary, factoring in maintenance costs when calculating the operating cost of an air compressor is crucial for ensuring the reliability, efficiency, and longevity of the equipment. Neglecting maintenance can lead to increased energy consumption, decreased performance, and costly repairs, making it a cost-effective investment in the long run.
Air Compressor Spares: How Often Are Consumables Replaced?
For more information on air compressor spare parts and the appropriate frequency of replacement, please check out this article.
Wear and Tear Costs in Air Compressor Operation
It’s essential to account for wear and tear expenses.
Over time, various components of air compressors experience wear and aging due to continuous operation. Here are some key components and considerations:
Belts
Belts serve as the medium for transmitting power within belt-driven air compressors. They play a critical role in the compressor’s operation by transferring power from the motor to the compressor’s rotating components. If a belt breaks or slips, it can disrupt the entire operation of the screw air compressor.
Regular inspection and replacement of belts are necessary maintenance tasks, so the cost of belts should be included in the operating cost calculation.
It’s worth noting that direct drive air compressors, which eliminate the need for belts, are a more reliable and recommended option.
Direct drive air compressors and belt drive air compressors have their advantages and applications in various industries.
This article may help you make your choice: Direct Drive Air Compressors Vs Belt Drive Air Compressors
Solenoid Valves
Solenoid valves are vital components responsible for controlling the start and stop functions of the compressor. They regulate the flow of air and play a significant role in maintaining proper compressor operation.
If a solenoid valve fails, it can lead to disruptions in the compressor’s normal operation, affecting efficiency and potentially causing damage.
Other Components
Air compressors consist of various other components, each contributing to their overall functionality. These may include pressure switches, gaskets, seals, pneumatic fittings, and more.
Wear and tear on these components can lead to inefficiencies or malfunctions. Regular inspections, preventive maintenance, and the cost of replacement parts should be considered in your operating cost analysis.
Following a structured maintenance schedule can help prolong the lifespan of these components and minimize unexpected expenses.
Air Compressor Replacement Parts & Accessories: Ultimate List
There are many other replacement parts in an air compressor that may be replaced due to wear and tear.
We won’t go into details here, please check this article for more information.
Motor and Air End Damage
One scenario you definitely want to avoid is motor and main unit damage. The motor and main unit, often referred to as the “air end,” are critical components of any air compressor system. Let’s delve into the cost implications of their damage:
Motor Damage
The motor is the powerhouse of the air compressor, providing the necessary energy to drive the compression process. Any damage or failure of the motor can bring the entire compressor system to a halt.
Repairing or replacing a damaged motor can be a significant expense. Additionally, motor failures can lead to downtime, resulting in lost productivity and potentially affecting your operations.
Air End Damage
The air end is the heart of the compressor where the actual compression of air takes place. It consists of various components, including rotors, bearings, and seals, all of which are critical for efficient compression.
Damage to the main unit can result in decreased efficiency and increased energy consumption. If not addressed promptly, it can lead to further damage and a decline in the compressor’s performance.
Repairing or replacing components of the air end can be costly, and the longer the damage goes unaddressed, the more extensive the repairs may become.
What Is The Compressor Air End And How to Choose?
The compressor air end of a screw compressor is a vital component responsible for compressing and delivering air to various applications.
Understanding the air end and choosing the right one for your needs can ensure the efficiency and reliability of your compressor.
Preventing motor and air end damage should be a top priority in air compressor maintenance. Regular inspections, scheduled maintenance, and monitoring of performance can help identify issues early, reducing the risk of costly damage.
Additionally, investing in high-quality compressors with robust motor and air end components can contribute to longer equipment life and lower operating costs.
The Cost of Testing Compressed Air Quality
The often underestimated factor is compressed air quality testing costs.
Compressed air quality testing involves specialized equipment and expertise. The cost can vary depending on the number of parameters tested, testing frequency, and the volume of air sampled.
Moreover, corrective actions, such as filtration or system adjustments, may be necessary if test results reveal issues with air quality.
Quality Assurance
Compressed air plays a vital role in numerous industries, from manufacturing to healthcare.
Ensuring that the air used in various processes is free from contaminants is crucial for product quality, equipment longevity, and compliance with industry standards.
Testing Frequency
The frequency of compressed air quality testing can vary based on industry regulations, the criticality of air quality to operations, and the specific applications.
For instance, industries like pharmaceuticals or food production often require more frequent testing due to stringent quality requirements.
Testing Parameters
Compressed air quality testing typically includes assessments for various parameters such as:
- Particle Count: To measure the presence of solid particles and contaminants.
- Oil Content: To determine if there are traces of oil in the compressed air, which can be detrimental in certain applications.
- Microbiological Contamination: Important in industries where sterile air is essential, like healthcare or pharmaceuticals.
Benefits
While there are costs associated with compressed air quality testing, the benefits are substantial. These include:
- Product Quality: Ensuring that products are not contaminated during production.
- Equipment Protection: Preventing damage to sensitive equipment that relies on clean air.
- Regulatory Compliance: Meeting industry standards and regulations.
- Energy Efficiency: Maintaining clean air can lead to more efficient compressor operation and lower energy costs.
While compressed air quality testing does add to the operating costs of an air compressor system, its importance cannot be overstated.
The investment in testing is, in fact, an investment in product quality, operational reliability, and compliance.
Efficiency Loss in Air Compressors
The efficiency of an air compressor is a measure of how effectively it converts electrical power (usually expressed in KW and HP) into compressed air. It’s often represented as a percentage. The higher the efficiency, the less power is wasted, and the lower the operating cost.
How does air compressor efficiency affect overall enterprise costs?
Energy Consumption
Inefficient compressors consume more electrical power to produce the same amount of compressed air as efficient ones. This translates to higher energy bills.
Maintenance
Inefficient compressors tend to experience more wear and tear, leading to increased maintenance costs over time.
Multiple Compressors and System Efficiency
In some cases, it’s more efficient to use multiple smaller air compressors working together as a system rather than relying on a single large compressor. This strategy, known as load modulation or load sharing, can help improve overall efficiency.
More Energy-saving Air Compressor
It’s important to strike a balance between the upfront cost of a compressor and its long-term operating efficiency. Sometimes, investing in a more energy-efficient compressor with a slightly higher initial cost can lead to significant savings over its lifetime.
Factors such as load profile (how air demand fluctuates), duty cycle, and required air quality must be considered to make an informed decision.
In addition, the unanimous view is that variable speed air compressors can save a lot of energy costs. They are increasingly appearing in various major applications and projects.
Optimizing Layout and Space
The design and physical arrangement of your compressed air system can significantly impact operating costs.
Before installation, careful planning and design are crucial. Consider the following:
Space Utilization: Make the most of available space by optimizing the layout. Efficiently using your facility’s footprint can help avoid unnecessary expansion costs.
Location: Place the compressor in an area that minimizes heat and contaminants. A well-ventilated, clean environment can extend the lifespan of your compressor and reduce maintenance costs.
What is the Variable Speed(VSD) Compressor and How to Choose Correctly
Want to know more about VSD air compressor? Click to learn more:
- What is the VSD Compressor?
- What is the VFD in the VSD Compressor?
- The Difference between VSD and Fixed-Speed Compressor
- Features and Benefits of the VSD Compressor
- Costs and Operations: VSD Compressor vs. Fixed Speed Compressor
- How to Choose the Right VSD Air Compressor?
Optimize the Entire Compressed Air System
An optimized compressed air system can result in substantial energy savings and reduced operating costs.
Here’s how:
Shorten Cable Length
Reduce the length of electrical cables between the compressor and power source to minimize energy loss.
Minimize Pipeline Length
Shorter pipelines reduce pressure drop, which in turn reduces the energy required to maintain adequate air pressure. This also cuts down on the cost of pipe materials.
Lower Pressure Requirements
If your processes allow, operate the compressed air system at the lowest possible pressure to achieve the required air flow. Lower pressure means less energy consumption.
Air Quality
Ensure that the layout supports proper air quality. This includes effective separation of clean and contaminated air sources, as well as the correct placement of air dryers and filters.
Consider Future Expansion
When designing the layout, factor in the potential for future expansion. Leave space for additional compressors or equipment if your business is likely to grow.
Optimizing the layout and space utilization of your air compressor system is a crucial step in reducing operating costs. Efficient design, location, and maintenance can lead to energy savings, lower maintenance expenses.
How to Design An Air Compressor Room? 7 Things to Consider
What is the Air Compressor Room?
What Equipment is Included in An Air Compressor Room?
Working Pressure and Free Air Delivery (FAD)
Indoor or Outdoor?
Space for an Air Compressor Room
Air Quality in the Air Compressor Room
Pipe Connections and Distances
Air Compressor Room Ventilation Design
End of Article
Running an entire compressed air system is indeed no easy task. How to reduce air compressor costs is a question that almost every business owner considers.
By carefully considering and calculating these factors, you can arrive at a comprehensive estimate of the operating costs for your air compressor system. Hope our article is valuable to your cost saving and air compressor operating.
At last, remember that regular maintenance and efficiency optimization can lead to cost savings over time and prolong the life of your air compressor.