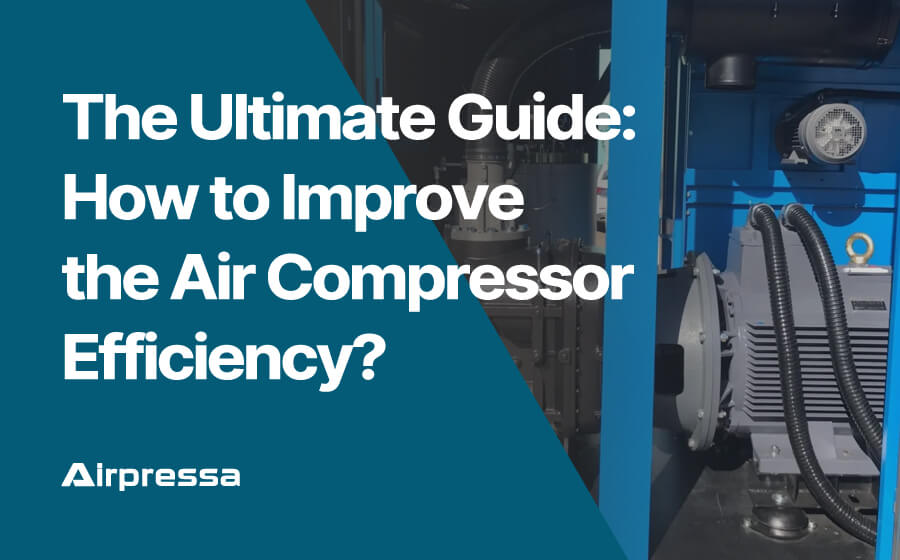
The air compressor efficiency is a concern for every company that operates air compressors. Improving the working efficiency of air compressors means saving energy costs, shortening production time, and increasing corporate profits
So how to improve your air compressor efficiency? Here are some tips.
Let’s dive in.
You can click on any section that you interest to get there quickly.
- Use the Compressor with Matching Air Flow
- Use Properly Designed Screw Air Compressors
- Optimize Compressor Operating Pressure
- Proper Lubrication
- Air Intake Filtration
- Keep the Efficient Cooling System
- Load Matching Control
- Minimize Air Leaks
- Equipped with Air Tanks for Your Compressor
- Optimizing the Compressed Air System
Use the Compressor with Matching Air Flow
A compressor with the air flow that can meet the needs of production or projects can greatly improve work efficiency.
The Consequences of Insufficient Airflow
Insufficient airflow from a screw compressor can lead to several adverse consequences. These include:
Reduced Productivity
When a compressor doesn’t produce enough air flow, it can’t meet the demands of pneumatic tools and processes. This leads to reduced productivity as operations slow down or come to a halt.
Energy Inefficiency
Operating a compressor below its designed airflow capacity can be highly energy-inefficient. The motor continues to consume energy, but the output doesn’t match the requirements, resulting in wasted power and increased operating costs.
Increased Wear and Tear
Continuous operation below the recommended airflow levels can lead to increased wear and tear on the compressor’s components, reducing its lifespan and necessitating more frequent maintenance.
How to Determine Air Flow that You Required
To improve screw compressor efficiency, it’s crucial to accurately determine how much air flow your specific applications require. Here’s how to do it:
1. Application Analysis
Begin by conducting a thorough analysis of your pneumatic applications. Identify the tools and processes that rely on compressed air and their respective air consumption rates. This information is essential for calculating your overall air demand.
2. Calculate Peak Demand
Determine the peak demand for compressed air during your operations. This usually occurs when multiple tools or machines run simultaneously. Knowing your peak demand helps size your compressor correctly.
3. Consider Variations
Keep in mind that air demand can vary throughout the day or between shifts. Factor in these variations to ensure your compressor can handle fluctuating requirements.
4. Use Online Tools
Several online calculators and software programs are available to help you calculate your air flow requirements more precisely. These tools consider various parameters, including pressure and duty cycle, to provide accurate estimates.
5. Consult a Professional
If you’re unsure about your calculations or have complex air system requirements, consider consulting with a compressed air system professional. They can perform a detailed assessment and recommend the most suitable compressor size and configuration.
You can contact us to get the exact air flow that you need.
Or you can check the article below, air flow is usually expressed in cfm or m3/min.
What Is CFM in Air Compressor And How To Calculate It?
CFM is a crucial factor in determining the performance and efficiency of air compressors. Understanding how to calculate it is essential for selecting the right compressor for your specific needs.
In this guide, we’ll break down the concept of CFM in air compressors in simple terms, provide practical examples and tips on how to calculate it.
Use Properly Designed Screw Air Compressors
One of the foundational steps to improve screw compressor efficiency is to ensure you are using compressors with well-designed features.
When selecting a screw compressor, carefully review its design specifications. Ensure it meets industry standards and has a proven track record of efficiency and reliability. Compressors with design flaws can lead to energy wastage and operational inefficiencies.
Convert to Direct-Coupled Compressors
Another effective strategy to enhance screw compressor efficiency is converting from a belt-driven compressor to a direct-driven compressor. Let’s explore why direct-coupled compressors can be a game-changer:
The Biggest Difference: Direct-Coupled vs. Belt-Type Air Compressors
Direct-connected air compressors and belt-type air compressors differ primarily in their power transmission mechanisms.
Direct-coupled compressors have a direct connection between the motor and the compressor unit, while belt-type compressors use belts and pulleys for power transmission.
Advantages of Direct-driven Air Compressors
Direct-connected air compressors offer several advantages over belt-type compressors, making them a preferred choice for improved efficiency:
Higher Efficiency: Direct-coupled compressors are more energy-efficient because they eliminate power losses associated with belt slippage and tensioning.
Reduced Maintenance: Belt-type compressors require regular maintenance to ensure the belts are in optimal condition. Direct-coupled compressors have fewer moving parts, reducing maintenance needs.
Space Savings: Direct-coupled compressors are often more compact, saving valuable floor space in your facility.
Better Alignment: Belt-driven compressors can experience alignment issues over time, leading to decreased efficiency and increased wear on components. Direct-coupled compressors maintain better alignment.
Direct Drive Air Compressors Vs Belt Drive Air Compressors
Direct drive air compressors and belt drive air compressors have their advantages and applications in various industries.
In this article, we will delve into the differences between direct drive and belt drive air compressors, exploring their unique features, performance, and suitability for different applications.
Optimize Compressor Operating Pressure
The operating pressure of a screw compressor is a critical factor influencing its efficiency. To ensure your compressor operates at its best, consider the following aspects related to operating pressure:
Consider System Losses
When setting the required pressure level for your screw compressor, it’s essential to account for system losses. These losses can occur in various components such as filters, piping, separators, and dryers.
Failure to consider these losses can result in the compressor operating at a higher pressure than necessary, leading to inefficiencies and increased energy consumption.
Avoid Excessive Pressure
Increasing discharge pressure beyond what is genuinely needed can lead to irregular usage patterns, such as leaks. This, in turn, reduces the overall efficiency of the compressor.
It’s crucial to strike a balance between the pressure required for your specific applications and overloading the system with excessive pressure.
Inconsistent Air Pressure Control
Another common issue that can hamper screw compressor efficiency is inconsistent air pressure control. Here are some considerations regarding air pressure control:
Sustained High Pressure
If the air compressor control system provides inconsistent or sustained high pressure, it can lead to inefficiencies.
Operating the compressor near its maximum pressure for extended periods puts more stress on the system and reduces its overall efficiency.
Regularly monitor and adjust the pressure control settings to ensure they align with your actual operational needs.
Sudden Drop in Air Compressor Pressure
A sudden drop in air compressor pressure can be a cause for concern. Here are some potential reasons for this issue:
Mechanical Problems: A sudden pressure drop can be indicative of mechanical problems within the compressor, such as a malfunctioning valve, worn-out seals, or an air leak. Regular maintenance and inspection can help identify and address these issues promptly.
Electrical Issues: Electrical problems, such as issues with the motor or control system, can also lead to pressure fluctuations. Regularly check the electrical components of your compressor for signs of wear or malfunction.
Proper Lubrication
Lubrication is the lifeblood of a screw compressor. Without adequate lubrication, the compressor’s internal components can experience excessive wear and friction, leading to reduced efficiency and potential breakdowns. Here’s how to ensure proper lubrication:
Choose the Right Lubricant
Selecting the appropriate lubricant for your screw compressor is crucial. Consult your compressor’s manual or manufacturer’s recommendations to determine the right type of oil or lubricant. Different compressors may require specific formulations to operate optimally.
Regular Oil Analysis
Implement a routine oil analysis program to monitor the condition of the lubricant. This involves taking oil samples at regular intervals and analyzing them for contaminants, wear particles, and degradation. Oil analysis can help identify potential issues before they lead to efficiency losses or equipment damage.
Maintain Proper Oil Levels
Ensure that the compressor always maintains the correct oil level. Too much or too little oil can negatively impact efficiency. Regularly check and adjust oil levels as needed to keep them within the manufacturer’s recommended range.
Change Filters and Separators
Filters and separators are essential components of the lubrication system. Over time, they can become clogged with contaminants, reducing the effectiveness of lubrication. Follow a maintenance schedule to replace these components as recommended by the manufacturer.
Monitor Oil Temperature
Excessively high oil temperatures can lead to oil breakdown and reduced lubricating properties. Install temperature monitoring systems and ensure that the oil temperature remains within the specified range.
Address Leaks Promptly
Oil leaks not only waste lubricant but can also lead to insufficient lubrication in critical areas. Inspect your compressor for oil leaks regularly and address them promptly.
Air Intake Filtration
A dusty environment will gradually reduce the working efficiency of your air compressor.
Therefore, it is necessary to maintain routine maintenance of the air intake filter.
Choosing Quality Air Filters
Start by ensuring that your screw compressor is equipped with high-quality air intake filters. These filters are the first line of defense against contaminants such as dust, dirt, and debris. Choose filters designed to capture even the smallest particles to prevent them from entering the compressor.
Regular Inspection and Replacement
Develop a routine maintenance schedule for inspecting and replacing air intake filters. Over time, filters can become clogged and less effective. Replace them according to the manufacturer’s recommendations or when pressure differentials indicate reduced airflow.
Proper Sizing
Ensure that the air filters are correctly sized for your compressor’s airflow requirements. Filters that are too small can restrict airflow, leading to increased energy consumption and reduced efficiency. Consult the compressor’s specifications to determine the right filter size.
Seal Air Leaks
Ensure that there are no air leaks in the compressor’s intake system. Even small leaks can allow unfiltered air to bypass the filters and enter the compressor, potentially causing damage and reducing efficiency.
Maintain a Clean Environment
Keep the area around the compressor clean to minimize the introduction of external contaminants. Regularly clean the compressor room or enclosure and address any sources of dust or particulate matter.
Explore Screw Air Compressor Valve Types: The Ultimate Guide
There are many types of air compressor valves, each with their own unique and indispensable functions. They Together form the air compressor valve system, allowing it to operate safely and stably.
This article highlights the 11 main air compressor valve types. How do they work?
Keep the Efficient Cooling System
It is difficult for any machine to work efficiently when the cooling system is out of balance.
One of the effective ways to improve the working efficiency of the air compressor is to keep the cooling system running normally.
Regular Cleaning
Dust and debris can accumulate on the cooling fins and surfaces of the compressor’s heat exchangers. Regularly clean these components to prevent reduced heat transfer efficiency. This simple maintenance task can significantly impact the compressor’s overall performance.
Check Coolant Levels
Screw compressors often use a cooling system that relies on a coolant or lubricant to dissipate heat. Ensure that the coolant levels are within the manufacturer’s recommended range. Low coolant levels can lead to overheating and reduced efficiency.
Monitor Cooling Temperatures
Install temperature gauges at critical points in the cooling system, such as the inlet and outlet of the heat exchangers. Keeping an eye on these temperatures can help you detect issues like reduced coolant flow or fouling of heat transfer surfaces early on.
Inspect Fans and Blowers
Cooling fans and blowers are essential for maintaining proper airflow through the compressor’s cooling system. Regularly inspect and maintain these components to ensure they are functioning optimally. Replace damaged or worn-out fan blades as needed.
Consider Ambient Temperature
The ambient temperature in the compressor room can impact cooling efficiency. If the compressor operates in a hot environment, consider additional cooling solutions such as air conditioning or ventilation to maintain optimal operating conditions.
Use Heat Recovery
In some applications, it’s possible to recover heat generated by the compressor and repurpose it for other heating needs within the facility. This not only improves overall energy efficiency but also reduces operating costs.
Load Matching Control
Understanding Load Profile
To optimize efficiency, it’s vital to understand your facility’s compressed air demand throughout the day. Air demand can fluctuate, and a compressor that’s too large for the load wastes energy during partial load conditions.
In addition, especially for screw air compressors, variable frequency technology is very mature and widely used.
Variable Speed Drive (VSD) Compressors
What is the VSD Compressor?
The Variable Speed Drive (VSD) compressor is a type of air compressor designed to adjust its motor speed and, consequently, its compressed air output to match the specific air demand of a system. This technology provides several advantages in terms of energy efficiency and performance.
A significant advantage of the VSD compressor is greater efficiency and energy utilization.
Traditional fixed-speed compressors run continuously, cycling on and off to meet air demand. This on-off cycling can be inefficient, especially when air demand fluctuates.
On the other hand, VSD compressors can adjust their speed to provide only the required amount of compressed air. This results in energy savings because the compressor is not running at full capacity when it’s not needed.
More and more entrepreneurs consider investing in variable speed drive screw compressors.
Multiple Compressor Control
In facilities with multiple compressors, employing a master controller that manages the operation of these units can be highly efficient. The controller can coordinate the operation of compressors to ensure that the most energy-efficient units are used during varying load conditions.
What is the VSD Compressor and How to Choose Correctly
Want to know more about VSD air compressor? Click to learn more:
- What is the VSD Compressor?
- What is the VFD in the VSD Compressor?
- The Difference between VSD and Fixed-Speed Compressor
- Features and Benefits of the VSD Compressor
- Costs and Operations: VSD Compressor vs. Fixed Speed Compressor
- How to Choose the Right VSD Air Compressor?
Minimize Air Leaks
Air leaks in a compressed air system can lead to energy wastage, increased operational costs, and decreased overall efficiency.
To minimize air leaks, follow these steps:
Pressure Drop Analysis
Monitor the pressure drop in your compressed air system over time. A significant and consistent pressure drop can be a sign of air leaks. Investigate and repair any pressure losses promptly.
Check the Whole System
We should implement a routine inspection schedule for the whole compressed air system This includes checking connections, pipes, valves, and other components for visible signs of leakage.
How to effectively check for compressed air leaks?
- Visual Inspection: Start with a visual inspection of your compressed air system. Look for signs of corrosion, wear, loose fittings, or damaged components. Pay special attention to areas where pipes and fittings connect.
- Listen Closely: Sometimes, you can hear compressed air leaks. Listen for hissing or whistling sounds around the system. Use a mechanic’s stethoscope to pinpoint the source if necessary.
- Feel for Leaks: Gently run your hand along pipes and fittings while the compressor is running. You may feel air escaping through leaks. Be cautious when doing this, especially if the compressed air system operates at high pressure.
- Soap and Water Test: Perform a soap and water test by applying a soapy water solution to potential leak points. If bubbles form, it indicates a leak. Be sure to shut down the compressor before conducting this test for safety reasons.
- Use Detection Tools: Employ advanced detection tools like ultrasonic leak detectors or thermal imaging cameras. These tools offer precise and efficient leak detection capabilities, especially for larger systems or hard-to-reach areas.
Equipped with Air Tanks for Your Compressor
In many air compression projects, you will find that there is always an air tank (maybe many air tanks).
It plays a very important role in the operation of the entire system.
1. Stabilizing Air Pressure
Holding a Reserve: The air tank, also known as an air receiver, acts as a reservoir for compressed air. It stores excess compressed air generated by the screw compressor when demand is low.
Mitigating Pressure Fluctuations: During periods of high demand, the screw compressor can draw from this stored reserve, preventing rapid cycling and pressure fluctuations in the system.
Enhancing Consistency: Stable air pressure is vital for many applications. Air tools, pneumatic machinery, and manufacturing processes benefit from a consistent air supply, which is facilitated by the presence of an air tank.
2. Reducing Compressor Load
Minimizing Start-Stop Cycles: Frequent starting and stopping of a screw compressor can lead to wear and tear on the motor and associated components. With an air tank in place, the compressor can operate for more extended periods at a steady rate, reducing the frequency of these cycles.
Energy Efficiency: The reduced need for start-stop cycles translates to energy savings, as starting a compressor typically requires a surge of power. Maintaining a more continuous operation is more energy-efficient.
3. Heat Dissipation
Compressing air generates heat, and prolonged high-temperature operation can be detrimental to a screw compressor’s components. An air tank can serve as a heat exchanger, allowing the compressed air to cool as it sits in the tank, thus extending the life of the compressor.
4. Emergency Supply
As the backup air source, in the event of a temporary power outage or compressor malfunction, the air tank can provide a reserve of compressed air for essential processes or equipment, preventing costly downtime.
Optimizing the Compressed Air System
Finally, in addition to the performance and maintenance of the air compressor, the optimization of the entire compressed air system is equally important.
Improve Machine Layout
Strategic Placement
The location of your screw compressor within your facility can significantly impact its efficiency. Ensure that it is situated in a well-ventilated area, away from sources of excessive heat. Proper ventilation helps prevent overheating, which can compromise performance and longevity.
Accessibility
Facilitate easy access for maintenance and servicing. A well-organized layout ensures that technicians can perform routine checks and repairs efficiently, minimizing downtime.
Shorten Pipeline Routes
Minimize Pressure Drops
Long pipelines can lead to pressure drops, diminishing the effectiveness of your compressed air system. Where feasible, reduce the length of the pipeline to maintain optimal pressure levels throughout the system.
Regular Maintenance
Conduct periodic inspections and maintenance of the pipeline, including the removal of moisture and debris. This helps ensure smooth airflow and efficient compressor operation.
Provide a Conducive Working Environment
Temperature Control
Maintain a consistent temperature in the compressor room. Extreme heat or cold can negatively impact compressor efficiency and lifespan. Proper temperature control is vital.
Humidity Management
Implement measures to control humidity levels, preventing moisture buildup within the system. Excessive moisture can lead to corrosion and decreased performance.
We try to list as many ways as possible to improve the air compressor working efficiency of .
However, different machines, projects, environments, and maintenance will bring different results.
If there are any new ideas, we will continue to update here.