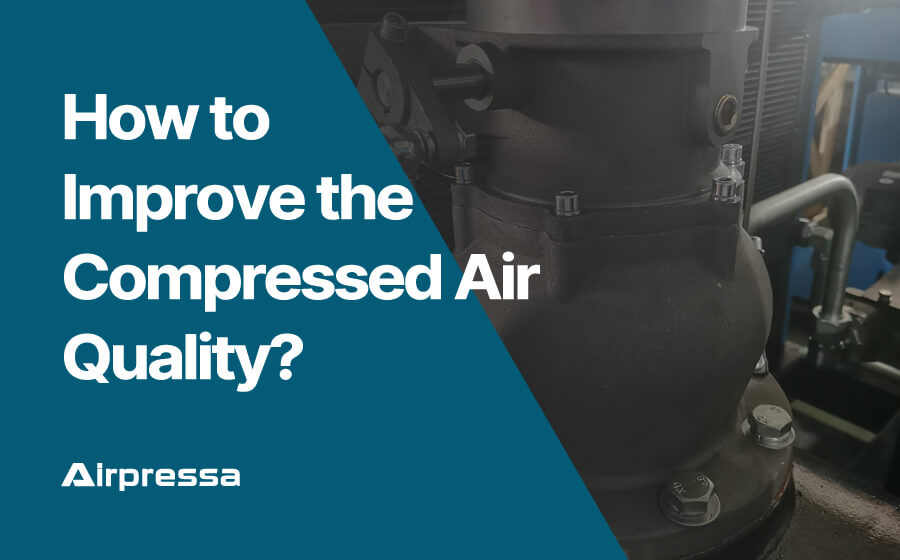
Compressed air quality is a paramount concern for industries utilizing air compressors.
Over the past several years, numerous air compressor manufacturers and associated suppliers have offered comprehensive solutions to address this issue.
You can click on any section that you interest to get there quickly.
Improve the Quality of Inhaled Air
Certainly! Enhancing the quality of inhaled air is indeed the first and foremost step towards improving compressed air quality.
Clean Environment of Air Intake
The point where your compressor system inhales air is where the entire process begins. To maintain the quality of the inhaled air, you should locate the air intake in a clean and pollution-free area as far as possible from sources of dust, dirt, or fumes.
The cleaner the inhaled air, the better the quality of the compressed air.
High-Quality Intake Filters
The air around us carries some amount of microscopic contaminants. That’s where high-quality intake air filters come into play.
They strain out any potential contaminants from the inhaled air, acting as a pre-emptive line of defense against pollutants. Regular replacement of these air filters keeps them effective.
Minimize Moisture Intake
Often overlooked, moisture in the intake air can lead to various complications in the resulting compressed air, from corrosion to compromised tool performance. Dehumidifiers or air dryers prior to intake can be used, especially in regions of high humidity.
Improving the quality of inhaled air sets an excellent foundation, ensuring the rest of your compressed air system works on the best possible air supply, greatly enhancing the overall output quality.
Using High-Quality Air Dryers
Using high-quality dryers is a pivotal strategy to remove unwanted moisture from your compressed air.
There are several types of air dryers, and among the most common are refrigerated and desiccant air dryers.
Refrigerated Air Dryer
Refrigerated air dryers work by cooling compressed air to lower its dew point, causing moisture to condense and separate from the air stream.
This process effectively removes water vapor and reduces the humidity of the compressed air.
The process within a refrigerated air dryer involves the following steps:
- Compressed air enters the dryer.
- This air is cooled down to about 3 degrees Celsius, using a refrigerant. This cooling leads the moisture in the air to condense.
- The condensed moisture is then separated and drained away.
- The cold dried air is re-heated to room temperature before exiting the dryer, to prevent downstream pipe sweating and corrosion.
Refrigerated air dryers are an excellent choice for most industrial drying applications, they are typically used where a dewpoint of +2°C – +10°C is sufficiently dry.
Refrigerated air dryers are widely used in applications where moderate levels of moisture removal are required. They are cost-effective, energy-efficient, and suitable for most industrial environments.
What Is Pressure Dew Point? Why Is It So Important?
Pressure dew point is a key term that must be mentioned in the air compressor industry. It plays a vital role in the entire compressed air system, connected equipment and applications.
Different from atmospheric dew point, pressure dew point has more practical application significance. So, what is pressure dew point and why is it so important?
Desiccant Air Dryer
Desiccant air dryers utilize adsorption technology to remove moisture from compressed air. These dryers contain desiccant materials, such as silica gel or activated alumina, which attract and retain water vapor molecules from the air stream.
The operation inside a desiccant air dryer consists of the following main steps:
Wet air passes directly over desiccant material, usually silica gel or activated alumina.
As the air interacts with the desiccant material, moisture adheres to the surface of the desiccant, effectively taking the moisture out of the air.
Once the desiccant material is fully saturated with moisture, it can no longer provide drying. To prevent this, desiccant dryers typically have two twin towers, filled with desiccant.
While one tower is adsorbing moisture from the compressed air, the other tower will regenerating itself, by driving off the collected moisture.
Desiccant air dryers are typically used where a pressure dewpoint below freezing is required (-40 °C and -70 °C are common).
These air dryers are often used in critical applications where stringent air quality standards must be met, such as pharmaceutical manufacturing, electronics production, and food processing.
However, desiccant dryers typically require more maintenance and consume additional energy compared to refrigerated air dryers.
What Is The Compressed Air Dryer? A Comprehensive Overview
The compressed air dryer is an important part of air compression system, it ensures the quality and efficiency of compressed air systems.
Let’s delve into what a compressed air dryer is and why it’s a crucial component in various industries.
After Air Filter System
The appropriate selection of compressed air filter grades contributes significantly to improving the compressed air quality. Each has a specific application depending on the degree of filtration required.
Solid Particles Removal
These filters, generally known as particulate filters, are designed to remove solid particles like dust, pollen, and rust. Their efficiency varies with the particle size they can filter out.
Filters are rated by the size of the particle they can remove, measured in microns. Common grades in this category include:
* P Grade – Pre-filters that can capture particles down to 1 micron.
* S Grade – Secondary filters for particles down to 1 micron.
* F Grade – Fine filters that can trap particles as small as 0.01 microns.
Oil Removal
Oil vapor and aerosols are frequently present in compressed air and can cause harmful effects if not adequately eliminated. Various grades of coalescing filters include:
* AO Grade – Oil aerosols removal down to 0.6 mg/m3.
* AA Grade – High efficiency for oil aerosols reduction to 0.01 mg/m3.
* ACS Grade – Specifically designed to eliminate oil vapor and hydrocarbon odors.
Water Vapor Removal
Water vapor is another common contaminant in compressed air. While dryers are typically used for this purpose, if any moisture remains, high-efficiency dry particulate filters (FD grade) can provide the final line of defense, removing even the tiniest water particles.
Using the Compressed Air Tank
Proper use of the compressed air tank (air receiver) will also improve compressed air quality.
Employing a compressed air tank serves multiple purposes in enhancing air quality:
Moisture Removal
The compressed air tank acts as a reservoir, allowing moisture to condense and settle at the bottom.
This separation process helps to remove water vapor from the air, reducing the risk of moisture-related issues such as corrosion and contamination downstream.
Particle Settlement
As the compressed air enters the tank, any solid particles present in the air tend to settle at the bottom due to gravitational force.
This settling process helps to trap contaminants, such as dust and debris, ensuring that cleaner air is delivered to the end-use applications.
Oil Separation
In systems where oil-lubricated compressors are used, the compressed air tank provides an opportunity for oil to separate from the air. This separation allows for the collection and removal of oil residues, preventing oil carryover and contamination of downstream processes.
Pressure Stabilization
The compressed air tank helps to maintain a stable pressure level within the system, reducing pressure fluctuations and ensuring consistent air delivery.
Oil-Free Compressors
Improving compressed air quality can be significantly enhanced by using of oil-free compressors.
Oil-free compressors offer several advantages for enhancing compressed air quality:
Elimination of Oil Contamination
Unlike oil-lubricated compressors, oil-free compressors do not introduce oil into the compressed air stream. This eliminates the risk of oil carryover, ensuring that the compressed air remains free from oil contamination.
The Ultimate Guide: What Is The Oil-free Air Compressor?
Reduced Risk of Product Contamination
In applications where compressed air comes into direct contact with products or processes, such as food packaging or pharmaceutical manufacturing, the use of oil-free compressors minimizes the risk of product contamination.
This helps maintain product integrity and ensures compliance with regulatory requirements.
Enhanced Air Purity
Oil-free compressors produce air with higher purity levels, making them suitable for critical applications where even trace amounts of oil can have detrimental effects.
By eliminating oil from the compressed air, these compressors deliver cleaner, safer, and more reliable air quality, resulting in improved product quality and reduced maintenance costs.
Oil-free compressor is especially suitable for these industries of PET, PETG, PP Container, Pharmaceutical, Liquid Medicin Packing, Dry Pharmaceutical Product, Mineral Water, Cosmetic, Food and Beverage, etc.
Rotary Screw Oil Free Air Compressors 30-55 kw 40-75 hp
Gas Type: Air
Water Lubricated & Dry Oil Free
Driven method: Fixed Speed & Variable Speed
Series: Rotary Screw Air Compressor
Power: 30/37/45/55 kw
Pressure: 0.7/0.8/1.0 Mpa
Flow: 4.3 – 10.0 m3/min