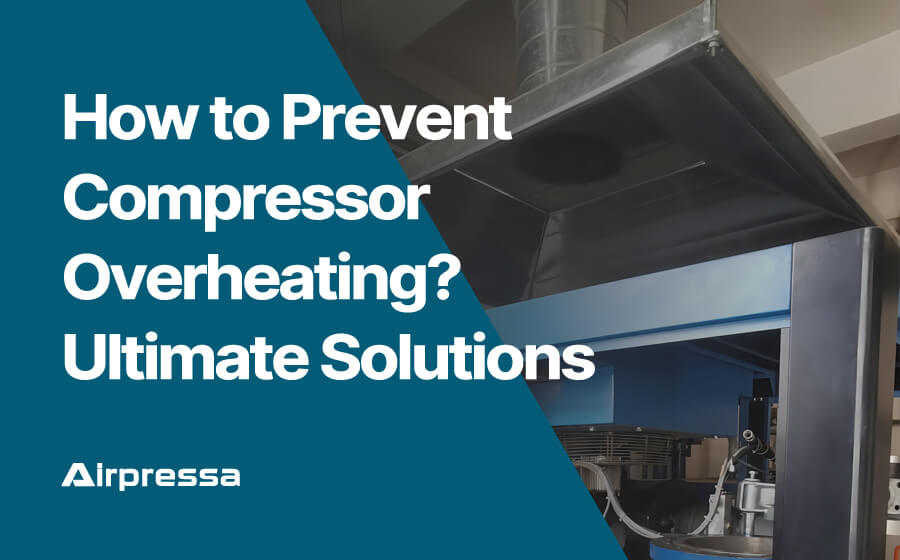
Compressor overheating is a common problem that can adversely affect the performance of the equipment and even lead to complete breakdown.
So, what unfavorable factors will cause it to overheat, and what are the solutions to prevent the compressor from overheating?
Let’s explore.
You can click on any section that you interest to get there quickly.
Consequences of Compressor Overheating
Overheating in compressors can have several detrimental consequences, impacting both the compressor itself and the overall system efficiency.
Reduced Efficiency
Overheating leads to increased friction and wear within the compressor components, reducing its overall efficiency.
As the temperature rises, the viscosity of the lubricating oil decreases, resulting in inadequate lubrication and increased frictional losses.
Component Damage
High temperatures can cause thermal expansion, leading to distortion and damage to critical components such as rotors, bearings, seals, and gaskets. This damage can compromise the integrity of the compressor and lead to costly repairs or even complete failure.
Oil Degradation
Excessive heat can accelerate the degradation of compressor oil, reducing its lubricating properties and thermal stability. This can result in oil breakdown, increased viscosity, and the formation of harmful sludge and deposits within the compressor system.
Reduced Air Quality
Overheating can cause the compressor to operate less efficiently, leading to inadequate cooling of the compressed air.
It will result in higher moisture content and decreased air quality, potentially leading to issues such as corrosion, contamination, and compromised product quality in downstream processes.
Increased Energy Consumption
Overheating requires the compressor to work harder to maintain optimal operating temperatures, resulting in increased energy consumption and higher operating costs. This not only impacts the compressor’s efficiency but also contributes to higher energy bills for the facility.
System Downtime
Severe overheating can lead to component failures and system shutdowns, resulting in costly downtime for maintenance and repairs. This can disrupt production schedules, impact productivity, and lead to financial losses for the business.
In summary, overheating in compressors can have significant consequences, ranging from reduced efficiency and component damage to compromised air quality and increased energy consumption.
It is crucial to monitor and address overheating issues promptly through proper maintenance, cooling systems, and operational controls to ensure the reliable and efficient operation of air compressors.
What Causes Air Compressor Overheating?
Several factors can contribute to overheating in air compressors:
Inadequate Lubrication
Insufficient lubrication or the use of improper lubricants can lead to increased friction and heat generation within the compressor. This can occur due to low oil levels, degraded oil quality, or improper oil viscosity.
High Ambient Temperatures
Operating in environments with high ambient temperatures can strain the cooling capacity of the compressor, leading to overheating. Poor ventilation or inadequate cooling systems exacerbate this issue.
Dirty or Blocked Air Filters
Clogged or dirty air filters restrict airflow into the compressor, reducing cooling efficiency and causing the compressor to overheat. Regular filter maintenance is essential to prevent this problem.
Excessive Load
Running the compressor beyond its designed capacity or continuously operating at high loads can lead to overheating. This can occur due to increased air demand, improper sizing of the compressor, or inefficient system design.
Faulty Cooling Systems
Malfunctioning or inadequate cooling systems, such as oil coolers, air coolers, or cooling fans, can fail to dissipate heat effectively, causing the compressor to overheat.
Compressor Design Issues
Poor compressor design, including inadequate cooling passages, improper rotor clearances (in rotary screw compressors), or insufficient lubrication systems (in oil lubricated compressors), can contribute to overheating under certain operating conditions.
Operating Conditions
Variations in operating conditions, such as changes in pressure, temperature, or humidity, can affect the compressor’s performance and lead to overheating if not properly managed.
Mechanical Issues
Mechanical problems such as worn or damaged bearings, misaligned components, or internal leaks can increase friction and heat generation, contributing to compressor overheating.
Electrical Faults
Electrical issues such as motor overload, phase imbalance, or voltage fluctuations can cause the compressor motor to overheat, leading to overall compressor overheating.
Poor Maintenance
Neglecting routine maintenance tasks, such as oil changes, filter replacements, or system inspections, can result in the accumulation of debris, degraded lubricants, or mechanical issues that contribute to overheating.
Better Design to Prevent Compressor Overheating
In production, better heat dissipation and reasonable layout can reduce the risk of compressor overheating.
Here’s how we approach the design process and the technologies and processes we use to enhance heat dissipation:
Optimal Layout Design
Engineering a compressor to successfully dissipate heat begins with the compressor’s layout and structure. Components should be arranged to enable sound airflow, reducing the chances of heat concentration in certain zones.
Cooling System Design
Implementing an effective cooling system is crucial for dissipating heat and maintaining optimal operating temperatures. This includes incorporating components such as oil coolers, air coolers, and cooling fans strategically within the compressor design to facilitate heat transfer.
Air Cooling Compressor VS Water Cooling Compressor
Air cooling compressor and water cooling compressor, as the two most widely used types of air compressors, have different cooling systems.
There are significant differences in production processes, cooling methods, cooling efficiency and applications. So how do we choose?
Optimized Rotor Design
For screw air compressors, the rotor profile and geometry play a significant role in heat generation and dissipation. By optimizing the rotor design, including the rotor profile, clearance, and surface finish, we can minimize frictional losses and improve heat dissipation efficiency.
Efficient Lubrication System
Proper lubrication is essential for reducing friction and heat generation within the compressor. Utilizing advanced lubrication systems with high-quality oils and precise delivery mechanisms ensures optimal lubrication to critical components, minimizing wear and heat buildup.
Enhanced Airflow Management
Implementing efficient airflow management techniques, such as optimizing inlet and outlet designs, ducting, and airflow paths, promotes better cooling and heat dissipation throughout the compressor system.
Advanced Cooling Technologies
Incorporating advanced cooling technologies, such as variable-speed cooling fans, liquid cooling systems, or heat exchangers, enhances heat dissipation efficiency and allows for precise temperature control under varying operating conditions.
Thermal Insulation
Applying thermal insulation materials to critical components and areas prone to heat buildup helps minimize heat transfer to surrounding components and maintain stable operating temperatures within the compressor.
Monitoring and Control Systems
Integrating intelligent monitoring and control systems enables real-time monitoring of temperature, pressure, and other critical parameters.
It allows for proactive identification of potential overheating issues and enables automatic adjustments to optimize performance and prevent overheating.
Material Selection
Choosing high-quality materials with excellent thermal conductivity and heat resistance properties for critical components ensures reliable operation and efficient heat dissipation throughout the compressor’s lifespan.
By integrating these technologies and processes into the design of screw air compressors, we can enhance heat dissipation capabilities, minimize the risk of overheating, and ensure optimal performance and reliability in various industrial applications.
The Ultimate List: Screw Air Compressor Parts
A screw air compressor is a complex machine with many parts that work together to produce compressed air. Each part plays a crucial role in the overall performance and efficiency of the compressor.
As such, it is essential to understand the different parts and their functions to properly maintain and repair the compressor.
In this article, we present the ultimate list of screw air compressor part and names, along with a brief description of each part and its function.
The Manual for Preventing Compressor Overheating at High Temperature
Preventing compressors from overheating at high temperatures is is a challenge.
Here are some effective strategies to prevent overheating in screw compressors operating in high-temperature environments:
1. Top Quality Compressor
Choose a screw compressor with high quality, reasonable layout and good heat dissipation function. This saves a lot of unnecessary work.
2. Proper Ventilation
Ensure the compressor room or installation area is adequately ventilated to allow for proper airflow.
Adequate ventilation helps dissipate heat generated by the compressor and prevents heat buildup in the surrounding environment.
3. Cooling System Maintenance
Regularly inspect and maintain the compressor’s cooling system, including air and oil coolers, to ensure they are clean and free from debris or obstruction.
Clean cooling fins and replace air filters as needed to maintain optimal airflow and cooling efficiency.
4. Optimized Lubrication
Use high-quality lubricants suitable for high-temperature applications and follow recommended lubrication schedules. Proper lubrication reduces friction and heat generation within the compressor, helping to prevent overheating.
5. Temperature Monitoring
Install temperature monitoring devices, such as thermocouples or temperature sensors, to continuously monitor the compressor’s operating temperature. Set up alarms or alerts to notify operators if the temperature exceeds safe limits, allowing for timely intervention.
6. Operating Conditions
Avoid operating the compressor beyond its rated capacity or in extreme ambient temperature conditions whenever possible. Adhere to manufacturer’s guidelines regarding operating conditions and load limits to prevent excessive heat buildup.
7. Regular Maintenance
Implement a comprehensive maintenance program that includes routine inspections, cleaning, and servicing of the compressor components. Address any signs of wear, leaks, or abnormal operation promptly to prevent issues that could lead to overheating.
8. Heat Dissipation Enhancements
Consider installing additional heat dissipation enhancements, such as heat exchangers, thermal insulation, or reflective coatings, to improve heat transfer and minimize heat absorption by surrounding components.
9. Control Pressure
Keep the system’s pressure within the manufacturer’s recommended range. Overpressure can lead to increased heat.
10. Environmental Controls
Implement environmental controls, such as shade structures or insulation, to minimize exposure to direct sunlight or extreme heat. Protecting the compressor from external heat sources helps maintain a cooler operating environment.
11. Gradual Startup
When starting a screw compressor after a long downtime, allow it to warm up gradually instead of abruptly moving to full load, minimizing the chances of overheating.
By implementing these preventive measures and proactive maintenance practices, operators can effectively prevent screw compressors from overheating in high-temperature environments, ensuring reliable operation and extending the equipment’s service life.
How to Design An Air Compressor Room? 7 Things to Consider
What Equipment is Included in An Air Compressor Room?
Working Pressure and Free Air Delivery (FAD)
Indoor or Outdoor?
Space for an Air Compressor Room
Air Quality in the Air Compressor Room
Pipe Connections and Distances
Air Compressor Room Ventilation Design