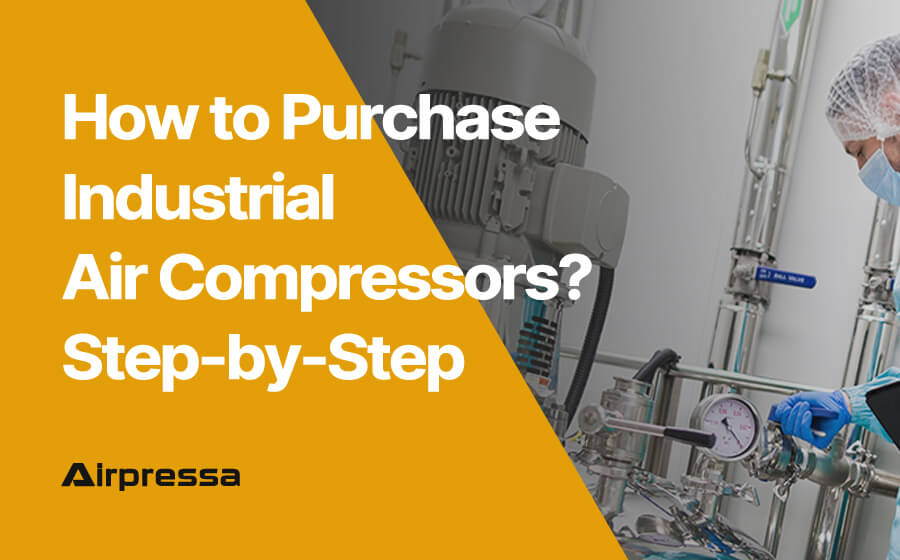
Industrial air compressors are essential tools for a variety of industries. However, with so many different types of compressors on the market, it can be challenging to determine which one is the best fit for your specific needs.
In this ultimate guide, we will explore the various types of industrial air compressors available, their unique features, and how to purchase the right one for your business.
You can click on any section that you interest to get there quickly.
Applications of Industrial Air Compressors
Screw air compressors are essential tools used in various industrial and production processes. Their versatility and efficiency make them a reliable source of compressed air in numerous industries. These compressors come in different sizes and designs to suit different applications, making them ideal for various industries.
By providing a reliable source of compressed air, they enable precise and efficient operation of machinery, tools, and control systems. Whether it is for manufacturing, construction, healthcare, or energy, screw air compressors are an essential tool for modern industry.
Manufacturing Industry
In the manufacturing industry, screw air compressors are used to power pneumatic tools, control systems, and machinery. They are essential in providing a reliable source of compressed air that can be used in many different applications, from spray painting to assembly line equipment.
Food and Beverage Industry
The food and beverage industry requires compressed air for a variety of applications, such as packaging, bottling, and pneumatic conveying. Screw air compressors are ideal for this industry because they can provide clean, oil-free air that meets the strict requirements for food safety.
Medical Industry
Screw air compressors play a critical role in the medical industry, where they are used to power surgical tools, dental equipment, and laboratory instruments. They must operate with precision and reliability, as even the slightest air contamination can have serious consequences.
Construction Industry
The construction industry relies on compressed air for a variety of tasks, such as drilling, sandblasting, and powering heavy machinery. Screw air compressors are ideal for construction sites because they are portable and can be easily moved around to different locations.
Automotive Industry
The automotive industry requires compressed air for many applications, such as painting, sanding, and operating pneumatic tools. Screw air compressors are ideal for this industry because they can provide a continuous supply of clean, oil-free air that is essential for high-quality painting and finishing work.
Textile Industry
In the textile industry, compressed air is used for many applications, such as cleaning, spinning, and weaving. Screw air compressors are ideal for this industry because they can provide a reliable source of clean, dry air that is essential for maintaining the quality and efficiency of textile production.
It is worth mentioning that the production process of the sprayed flannelette, which is the raw material for mask production, requires the intervention of industrial air compressors.
In 2020, due to the global epidemic of COIVD-19, countless manufacturers of velvet cloth and masks have purchased industrial screw air compressors from China.
Energy Industry
The energy industry requires compressed air for a variety of applications, such as power generation, oil and gas drilling, and refining. Screw air compressors are ideal for this industry because they can provide a reliable source of compressed air that can be used in many different applications, from powering machinery to providing compressed air for pneumatic controls.
Injection Molding Industry
The injection molding industry is a very important application of industrial air compressors.
In the plastic forming industry, compressed air is used to blow molded plastic into the desired shape. This process requires a consistent and high-quality source of compressed air to ensure that the plastic is evenly distributed and shaped correctly.
Screw air compressors are ideal for this application because they can deliver a steady flow of compressed air at a constant pressure, ensuring that the plastic is formed correctly every time.
In the metal film forming industry, screw air compressors are used to power pneumatic tools that are used to cut and shape metal films. These tools require a clean, dry source of compressed air to operate effectively.
Screw air compressors are equipped with filtration systems that remove moisture and other contaminants from the compressed air, ensuring that the pneumatic tools operate efficiently and the metal films are cut and shaped accurately.
Chemical Industry
The chemical industry requires compressed air for many applications, such as mixing, packaging, and powering machinery. Screw air compressors are ideal for this industry because they can provide a reliable source of clean, dry air that is essential for maintaining the quality and safety of chemical production.
Mining Industry
The compressors are used to power various drilling machines and equipment used in mining operations, such as drilling, ventilation, and powering machinery.
They also provide compressed air for ventilation systems in mines, ensuring that the working environment is safe and conducive for workers.
In other fields, industrial air compressors are also widely used.
For examples:
In agriculture, the compressors are used to power various tools and equipment, including sprayers, pneumatic seeders, and grain conveyors.
In power generation, the compressors are used in gas turbine power plants to provide compressed air for combustion.
In conclusion, these applications discussed above are just a few examples of how these compressors are used in various industrial and production processes.
As technology advances, more industries are likely to adopt screw air compressors, making them an essential tool for the future.
Before exploring how to correctly purchase industrial air compressors, we need to understand which common air compressors are used in industry and production. This is especially important for our future purchases.
So, let’s move on.
Reciprocating compressors
Reciprocating compressors, also known as piston compressors, are widely used in various industrial applications due to their efficiency, durability, and versatility.
Types of Reciprocating Compressors
Reciprocating compressors can be classified into two types: single-stage and multi-stage compressors.
Single-stage compressors have one or two cylinders and are suitable for low to medium pressure applications.
Multi-stage compressors have more than two cylinders and can achieve higher pressure ratios, making them ideal for high-pressure applications.
Common Industries and Applications
Reciprocating compressors are widely used in various industries and applications, including:
Oil and Gas Industry
Reciprocating compressors are used for natural gas gathering and processing, gas transmission, and oil refining. They can handle high-pressure gas compression, as well as gas dehydration, sweetening, and other processing tasks.
Chemical Industry
Reciprocating compressors are used for chemical synthesis, polymerization, and processing. They can handle various gases and vapors, including toxic and corrosive ones, and provide reliable compressed air for chemical processes.
Food and Beverage Industry
Reciprocating compressors are used for food processing, packaging, and storage. They can provide clean and oil-free compressed air for food-grade applications, such as beverage bottling, dairy processing, and snack packaging.
Manufacturing Industry
Reciprocating compressors are used for various manufacturing processes, including metalworking, woodworking, and plastic injection molding. They can provide compressed air for pneumatic tools, equipment, and controls, as well as for product cleaning and cooling.
Development Trends
Most of the small reciprocating compressors are for household use, and two-stage reciprocating compressors are used in industry and production.
Centrifugal Industrial Air Compressors
The centrifugal air compressor is a popular type of air compressor used in a variety of industries.
Types of Centrifugal Compressors
Centrifugal air compressors are divided into two types: radial compressors and axial compressors.
The radial compressor consists of a rotor with impellers that rotate in the casing, increasing the velocity of the air.
In contrast, the axial compressor consists of multiple stages of rotating blades that compress the air by moving it in a linear direction.
Industries and Applications
Centrifugal air compressors are commonly used in large-scale industrial applications where high volumes of compressed air are needed.
Centrifugal compressors are frequently found in oil and gas, chemical processing, power generation, and refrigeration industries.
In addition, they are also used in medical facilities and aerospace applications, where a reliable source of compressed air is critical.
Development Trends
In recent years, there has been a significant shift towards more energy-efficient centrifugal compressors.
The demand for these compressors has been driven by increasingly stringent energy efficiency standards and the desire to reduce operating costs.
As a result, many manufacturers are developing new technologies to improve the efficiency of centrifugal compressors, including advanced control systems, improved rotor designs, and variable frequency drives.
Screw Industrial Air Compressors
Screw air compressors are widely used in various industries and applications due to their high efficiency, low energy consumption, and ease of maintenance.
In recent years, screw air compressors have undergone significant advancements in terms of technology and design. Such as the variable speed air compressor, making air compression be more reliable and cost-effective.
Types of Screw Air Compressors
There are many types of screw air compressors, the common ones are as follows:
- Fixed speed air compressor
- Variable speed air compressor
- Oil lubricated air compressor
- Oil-free air compressor
- Low pressure air compressor
- Air compressor with tank for laser cutting
A screw industrial air compressor can have several characteristics at the same time, for example: oil-free frequency conversion air compressor. And 2-stage air compressors are more popular with industrial users.
Common Applications of Screw Air Compressors
Screw air compressors have a wide range of applications in various industries, including:
Automotive industry: screw air compressors are used for painting, pneumatic tools, and assembly lines.
Textile industry: screw air compressors are used for spinning, weaving, and dyeing.
Chemical industry: screw air compressors are used for mixing, stirring, and transportation.
Paper industry: screw air compressors are used for paper cutting, folding, and printing.
Electronics industry: screw air compressors are used for electronics manufacturing, including PCB assembly, soldering, and packaging.
Development Trend
Among industrial air compressors, screw type compressors are becoming more and more popular, especially variable frequency air compressors.
Besides, the development trend of screw air compressors is focused on energy efficiency, environmental friendliness, and automation.
For instance, many manufacturers are now producing screw air compressors with intelligent control systems that can monitor and adjust the compressor’s performance in real-time, optimizing its energy consumption and reducing maintenance costs.
According to market research, the global screw air compressor market is expected to reach $16.5 billion by 2027, with a compound annual growth rate (CAGR) of 5.6% from 2020 to 2027.
Tips
Screw air compressors have become mainstream industrial compressors. They have a high duty-cycle and can even run non-stop.
If you are looking for the industrial compressor with a duty-cycle of more than 60%, the screw air compressor is definitely the best choice.
Industrial Air Compressor Purchasing Step
There are several important factors to consider when we purchasing industrial air compressors.
From determining the required CFM, horsepower, pressure, and voltage, to deciding on the type of compressor, there are many considerations that can impact the efficiency and cost of your operation.
Step 1: Determine your required CFM, horsepower, pressure, and voltage
The first step in purchase the industrial air compressor is to determine your specific requirements for CFM, horsepower, pressure, and voltage.
CFM (cubic feet per minute) refers to the volume of air the compressor can deliver. What is CFM in compressor?
Horsepower and pressure refer to the power and force with which the air is delivered.
Voltage refers to the electrical requirements of the compressor and can vary depending on your location and power supply.
To determine your specific requirements, consider the size of your operation, the number of tools or machines that will require compressed air, and the frequency of use.
Choosing the industrial air compressor that can deliver the necessary volume and pressure to keep up with your operation, without wasting energy or incurring unnecessary costs.
Step 2: Determine the type of compressor you need
Once you have determined your requirements for CFM, horsepower, pressure, and voltage, it’s time to consider the type of compressor that will best meet your needs. There are several different types of compressors to choose from, each with their own advantages and disadvantages.
2.1 Reciprocating, centrifugal, or rotary screw compressor?
Reciprocating compressors are typically smaller and more affordable, making them a good choice for small businesses or workshops. They work by using a piston to compress air, which is then stored in a tank.
Centrifugal compressors are used for high-volume applications, such as in power plants and factories.
Rotary screw compressors are a popular choice for many industrial applications. They use two rotating helical screws to compress air, resulting in higher volumes and smoother operation. Rotary screw compressors are ideal for medium to large operations that require continuous compressed air.
When selecting a compressor, consider the size and type of operation, as well as the specific demands of your equipment.
2.2 Fixed speed or variable speed compressor?
Fixed-speed compressors run at a constant speed, providing a steady supply of compressed air. These compressors are typically less expensive but less efficient than variable-speed compressors.
Variable-speed compressors adjust their speed based on the demand for compressed air. They are more expensive but more efficient, as they can reduce energy usage during times of lower demand.
2.3 Oil-lubricated or oil-free compressor?
Lubricated compressors use oil to cool and lubricate the internal components. They are typically less expensive but require regular maintenance to check and change the oil.
Oil-free compressors use special coatings or materials to lubricate the internal components, making them suitable for applications where oil contamination is a concern. They are more expensive but require less maintenance.
Oil-free compressors are best suited for operations that require a clean, oil-free air supply, such as the food or medical industry.
Step 3: Consider your budget and costs
When purchasing industrial air compressor, it’s important to consider both the upfront purchase cost and the ongoing operational costs. Here are some factors to consider:
3.1 Purchase cost
Reciprocating compressors are typically the most affordable, followed by centrifugal compressors and rotary screw compressors.
However, when considering the total cost of ownership over the lifespan of the compressor, rotary screw compressors are often the most cost-effective option.
3.2 Operational costs
Variable speed compressors are typically more energy efficient than fixed speed compressors, which can result in significant cost savings over time.
While variable speed compressors may be more expensive to purchase, they can often pay for themselves within a few years of operation.
Where Should I Purchase Industrial Air Compressors?
Finding the best supplier for your industrial air compressor needs can be a daunting task. With so many options available, it can be challenging to determine which supplier is the best fit for your business.
In this section, we will discuss the advantages and disadvantages of purchasing from international brands, dealerships, and importing from China to help you make an informed decision.
International Known Brands
There are several internationally recognized brands that have earned a reputation for quality and reliability.
These brands have a vast network of distributors and service centers worldwide, making it easy to find replacement parts and service when needed.
Advantages:
- Guaranteed quality and reliability
- Easy access to replacement parts and service
- Reputation for being a trusted brand in the industry
Disadvantages:
- High minimum order quantity
- Higher cost compared to other options
- Limited customization options
- Longer lead times for delivery due to production and shipping times
- You may have difficulty getting a response from them
Purchasing from distributors
Another option for purchasing the industrial air compressor is to go through a distributors or dealers. They offer a variety of brands and models, and often have a more personalized approach to customer service.
Advantages:
- Access to a variety of brands and models
- Personalized approach to customer service
Disadvantages:
- Higher prices compared to other options
- Limited customization options
- Less control over the manufacturing process
Importing from China
Importing industrial air compressors from China has become a popular option due to the lower cost of labor and production.
China is known for its manufacturing capabilities, and there are many reputable suppliers that offer the wide variety industrial air compressors.
Advantages:
- Lower cost compared to other options
- Customization options available
- Access to a wide range of suppliers and manufacturers
Disadvantages:
- Longer lead times for delivery due to shipping times
- Quality control issues may arise if not working with a reputable supplier
Each option has its advantages and disadvantages, and the best choice is depending on your business and budget.
Consider factors such as cost, customization options, and access to replacement parts and service when making your decision. By taking the time to research and choose the right supplier, you can ensure that your industrial air compressor meets your business needs and runs smoothly for years to come.
Common Mistakes When Purchasing Industrial Air Compressors
It’s important to educate potential buyers about common mistakes to avoid when purchasing an air compressor. Here are some of the most common mistakes buyers make when buying industrial air compressors.
Not determining the correct CFM, horsepower, pressure, and voltage
When purchasing an air compressor, it’s important to ensure that it meets the specific neyeds of your application. Failure to do so can lead to inefficiency, higher costs, and even damage to your equipment.
You should take the time to evaluate your needs and specifications before making a purchase.
Choosing the wrong type of air compressor
As mentioned earlier, there are three main types of air compressors: reciprocating, centrifugal, and rotary screw. Each type has its own advantages and disadvantages.
Factors such as air demand, duty cycle, and maintenance requirements should be considered when selecting the appropriate type of compressor.
Not considering the costs associated with the compressor’s operation
While the initial cost of an air compressor is important, it’s equally important to consider the long-term operating costs. This includes the cost of energy, maintenance, and repairs.
Choosing a compressor that is energy-efficient and requires minimal maintenance can save you significant costs over the life of the compressor.
VSD (Variable Speed) air compressors meet this point, What is the VSD Compressor and How to Choose Correctly.
Choosing the wrong size compressor
Choosing the wrong size compressor can lead to inefficiency and unnecessary wear and tear on the compressor.
A compressor that is too small for your needs will have to work harder to meet demand, while a compressor that is too large can lead to wasted energy and higher costs.
Ignoring the importance of air quality
The quality of compressed air is critical for many applications, particularly those in the medical and food industries.
Choosing a compressor that meets the appropriate air quality standards is important to avoid contamination and ensure product safety. In these industries, oil-free air compressors are the best option.
Not considering the compressor’s noise level
Air compressors can be noisy, and excessive noise can be a problem in certain environments. Choosing a compressor with a lower decibel level can help reduce noise pollution and maintain a safer work environment.
In conclusion
Purchasing the industrial compressor is a major investment. Hope this guide is valuable to you.
If you have more questions, you can contact our experts to answer them for you.