Home » Industries »
Air Compressors for Textile Industry
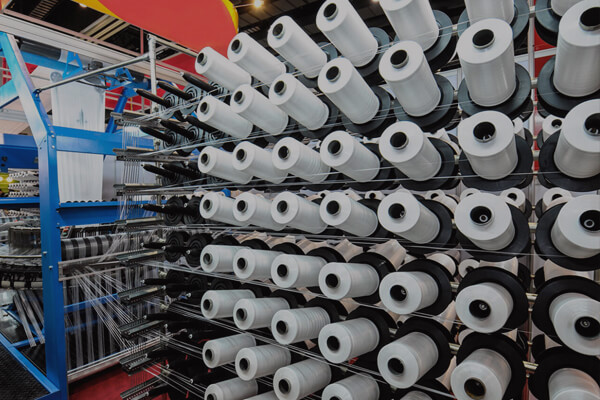
Air compressors have become indispensable tools in the textile industry, powering various machines and processes that contribute to the creation of high-quality fabrics.
From spinning and weaving to dyeing and printing, every step in the textile production journey requires precision, efficiency, and consistent air power.
Whether it’s optimizing energy consumption, enhancing production speed, or maintaining product integrity, air compressors have become a driving force behind the textile industry’s progress.
How Is the Air Compressor Used in the Textile Industry?
Air compressors play a pivotal role in the textile industry, contributing to a multitude of applications that enhance efficiency, quality, and overall production processes. This unassuming yet essential equipment finds itself seamlessly integrated into various facets of textile manufacturing, ensuring the precision and consistency that the industry demands.
Each step, from raw material handling to fabric finishing, demands a specific set of air compressor characteristics to ensure efficiency, precision, and overall quality.
Steam Treat and Straighten Yarn
Before the yarn takes its transformative journey from raw material to woven fabric, it undergoes a pivotal stage known as steam treatment. This process involves the controlled application of steam to relax and rejuvenate the fibers.
The air compressor provide the pressurized air required to drive steam generation to ensuring that the fibers are coaxed into a state of relaxation, prepared for the subsequent steps of textile production.
Pneumatic Conveying and Material Handling
Air compressors are instrumental in powering pneumatic conveying systems that transport raw materials, such as fibers and dyes, through pipelines. This process ensures the smooth and efficient movement of materials within the manufacturing facility, minimizing manual handling and reducing the risk of contamination.
Spinning and Weaving
In the spinning and weaving processes, air compressors regulate the tension of threads, ensuring uniformity and strength in the resulting fabric. They control air jets used to position and guide threads during weaving, maintaining the fabric’s integrity and texture.
Dyeing and Printing
Air compressors facilitate dye dispersion during the dyeing process, ensuring even color distribution across textile fibers. In printing, air assists in the precise application of pigments onto fabric surfaces, resulting in vibrant and well-defined patterns.
Fabric Cleaning and Finishing
Compressed air is harnessed for fabric cleaning processes, where it assists in removing dust, lint, and other contaminants from the surface. Additionally, air compressors are crucial in the finishing stages, such as ironing and steaming, ensuring that textiles leave the facility in a pristine and refined state.
Machinery Operation and Maintenance
Textile machinery often relies on compressed air for operational mechanisms, such as the air-jet looms, ginning mills, and spinning machines.
Air compressors power various pneumatic actuators, valves, and control systems that enable the smooth functioning of machinery. They are also used for cleaning and maintenance tasks, such as clearing clogged nozzles and dust removal from equipment.
Waste Water Treatment
In textile dyeing and finishing processes, wastewater is generated. Air compressors are used in wastewater treatment plants to provide aeration, promoting the growth of beneficial microorganisms that aid in breaking down pollutants before discharge.
Choosing Air Compressor for Textile Manufacturing
In the intricate tapestry of the textile industry, the selection of the right air compressor emerges as a crucial decision that underpins the seamless functioning of various production processes.
The textile industry’s diverse requirements necessitate careful consideration of various factors to ensure the right air compressor is chosen to drive productivity, quality, and cost-effectiveness.
Evaluating Air Demands
Air consumption requirements vary across textile processes. While some stages demand high volumes of compressed air, others require consistent pressure and quality.
By comprehensively assessing the air demands of each operation, one can determine the appropriate compressor capacity, pressure rating, and air quality standards necessary to meet production needs.
Precision Control and Energy Efficiency
In precision-demanding processes like weaving and dyeing, air compressor systems must offer precise control over air pressure and flow. Look for compressors equipped with advanced control systems that can regulate air output with accuracy, minimizing waste and maximizing energy efficiency.
Quality Considerations
Textile quality is paramount, and compressed air quality plays an integral role in maintaining it.
Air compressors used in dyeing and printing must provide oil-free and contaminant-free air to prevent color inconsistencies and fabric defects.
Moerover, integrating air treatment solutions such as air dryers and compressed air filters ensures the delivery of clean and dry air, safeguarding the end product’s integrity.
You also can check our complete compressed air system.
Maintenance and Reliability
Selecting an air compressor with a robust design and reliable performance can significantly impact production uptime. The textile industry operates around the clock, and any unexpected downtime can disrupt timelines and erode profits.
In the development of air compressors in recent years, the stability and reliability of rotary screw air compressors have been affirmed and widely used in the textile industry.
Cost Analysis
While capital expenditure is a consideration, a more comprehensive approach involves evaluating the total cost of ownership. This includes energy consumption, maintenance, spare parts, and service.
Investing in energy-efficient compressors may have a higher upfront cost but can lead to substantial long-term savings.
Known for their energy savings, variable speed compressors are becoming increasingly popular in manufacturing.
More details about variable speed(VSD) compressor, you could click here to check: What is the VSD Compressor and How to Choose Correctly
In conclusion, the selection of the right air compressor for the textile industry is a multifaceted endeavor. It requires a meticulous understanding of the textile manufacturing process, an assessment of air demands, consideration of precision control and air quality, reliability, and cost implications.
What is the Best Air Compressor for Textile Industry?
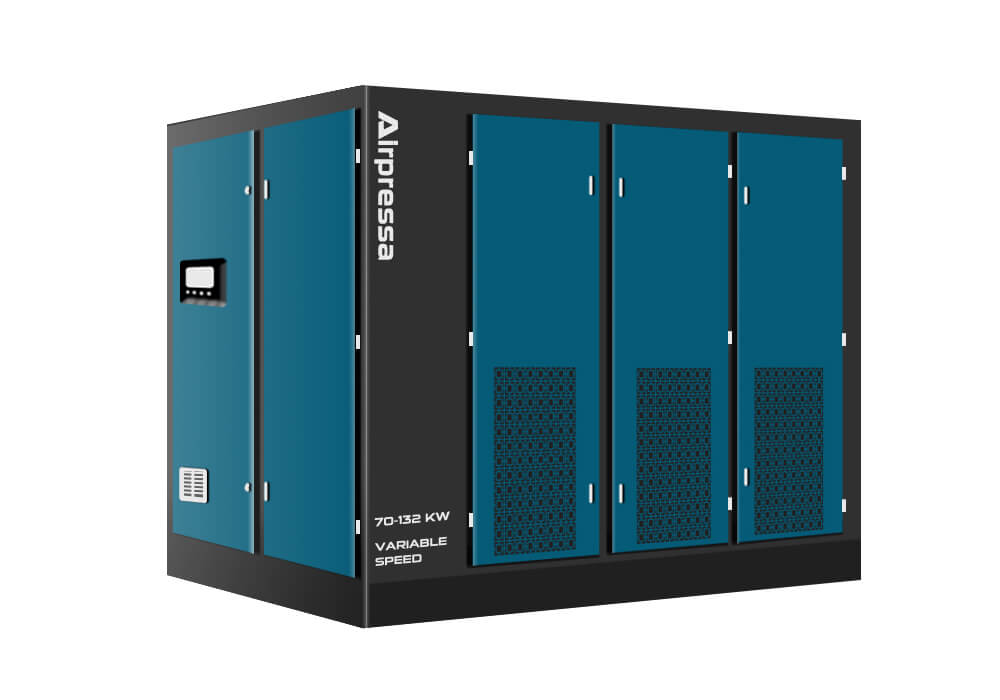
Variable Speed Compressors
By employing variable speed drive technology, these compressors optimize energy consumption by adjusting the motor’s speed according to the air demand.
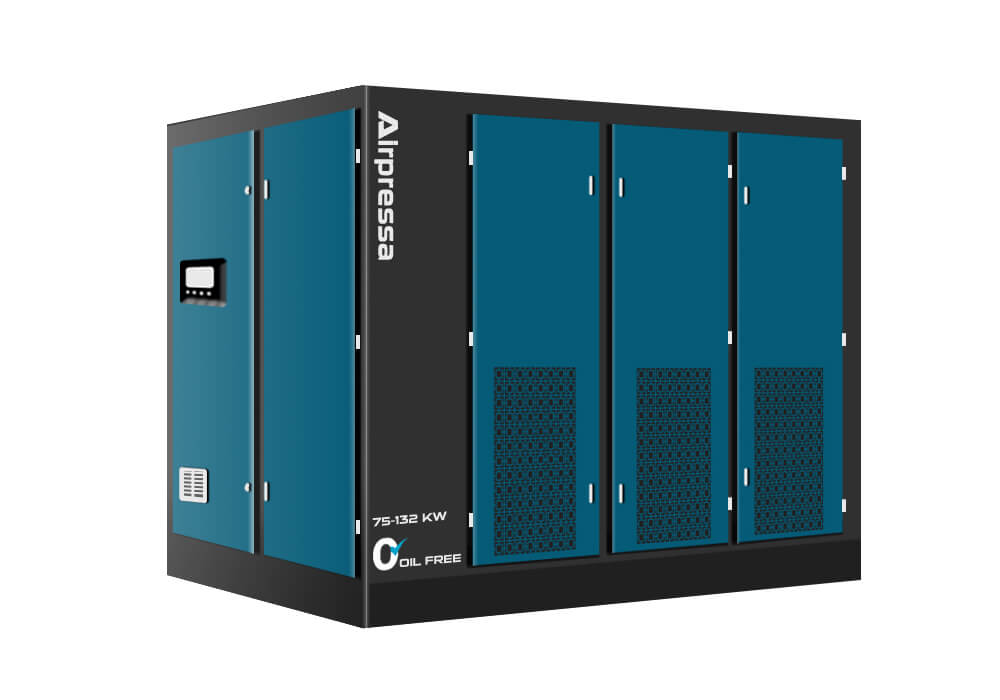
Oil-free Compressors
Oil free air compressors provide high-quality compressed air free from oil contamination, ensuring the integrity of sensitive processes and applications.
Get Expert Support
Choose Airpressa for all your compressed air needs and experience the benefits of working with a reliable, professional, and customer-focused manufacturer.