Home » Industries »
Mining Air Compressor
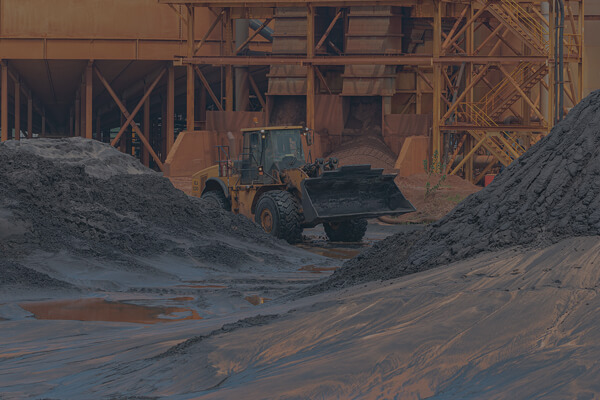
Air Compressor for Mining
Mining air compressors play a vital role in the mining industry, providing a reliable and efficient source of compressed air for various critical applications. From drilling and blasting to powering pneumatic tools and machinery, air compressors are indispensable in enhancing productivity and ensuring safety in mining operations.
How Is the Air Compressor Used in the Mining Industry?
Enabling Efficient Drilling and Blasting Operations
In mining, drilling and blasting are essential processes for excavation and rock fragmentation. Air compressors power pneumatic drills that penetrate hard surfaces, making way for mining activities. The controlled release of compressed air in the drilling process facilitates smooth and efficient drilling operations, resulting in increased productivity and reduced costs.
Ventilation and Dust Control
Mining environments can be hazardous due to the accumulation of dust and gases. Air compressors drive ventilation systems that maintain a steady flow of fresh air in underground mines, ensuring a safe and breathable atmosphere for workers. Additionally, compressed air is utilized to suppress dust, minimizing respiratory hazards and promoting a cleaner work environment.
Powering Pneumatic Tools and Machinery
From jackhammers to material handling equipment, pneumatic tools are widely used in the mining industry. These tools require a reliable source of compressed air to operate effectively. Air compressors supply the necessary air pressure to power these tools, enhancing their performance and facilitating various mining tasks.
Drills, wrenches, hack saws, and other vital equipment used in the depths of underground mines all rely on compressed air for optimal performance.
Supporting Flotation and Separation Processes
In mineral processing, flotation and separation processes are crucial for separating valuable minerals from gangue. Air compressors provide the necessary air supply for froth flotation, a widely used method in mineral concentration. The injected compressed air produces bubbles that carry hydrophobic particles to the surface, enabling their separation from the hydrophilic gangue.
Dust Control in Material Conveyance
Mining involves the transportation of bulk materials through conveyor systems. Dust can be generated during material handling, posing health risks and equipment wear. Air compressors contribute to dust control by powering dust suppression systems along conveyor belts, minimizing airborne particulates and ensuring a safer working environment.
Cleaning Applications
The clean and pressurized nature of compressed air makes it ideal for purging unwanted particles from filters and other spaces within the dusty and dirty environment of mining operations.
Using compressed air for cleaning tasks reduces the need for additional cleaning materials, contributing to the longevity of vital mining equipment and minimizing downtime for maintenance.
Emergency and Rescue Operations
Compressed air plays a critical role in emergency situations and rescue operations within mining facilities. Portable air compressors supply air to breathing apparatus for miners during emergencies, providing them with a reliable source of breathable air while evacuating hazardous areas.
In conclusion
Air compressors are indispensable tools in the mining industry, catering to a wide range of applications that enhance productivity, safety, and efficiency. From drilling and blasting to powering pneumatic machinery, providing ventilation, and supporting mineral processing, air compressors contribute significantly to the success of mining operations. Their reliable and versatile nature makes them a fundamental component in modern mining practices, ensuring smooth and safe mining activities.
Selecting the Right Air Compressor for Mining Applications
As technology continues to advance, the mining industry seeks innovative solutions to optimize energy consumption, reduce operating expenses, and enhance overall productivity. In this pursuit, efficient screw air compressors have emerged as a game-changing technology that offers significant advantages for mining operations.
Variable Speed Screw Air Compressors
Rotary screw compressors are widely used in manufacturing and mining industries. Traditional fixed-speed compressors were once the norm, operating at a constant speed regardless of the air demand.
However, this approach led to energy wastage.
Screw air compressors have undergone remarkable advancements in recent years.
The introduction of variable speed drive (VSD) technology revolutionized the air compressor industry. Variable speed screw compressors adjust the motor speed based on air demand, ensuring that the compressor operates at the most energy-efficient level at all times.
Oil Free Screw Air Compressors
In recent years, oil-free air compressors have emerged as a game-changer in the mining industry, offering a host of benefits that improve productivity, safety, and sustainability.
1. The Advantages of Oil-Free Technology
Oil-free air compressors, as the name suggests, operate without the need for lubricating oil in the compression chamber. This technology eliminates the risk of oil contamination in the compressed air stream, ensuring the purity and cleanliness of the air supply. In mining applications, where even the slightest contamination can cause equipment malfunctions and compromise product quality, oil-free air compressors offer a significant advantage.
2. Enhanced Safety and Environmental Compliance
Safety is a paramount concern in mining, particularly in confined and hazardous environments. Oil-free air compressors reduce the risk of oil leakage and fire hazards, making them ideal for use in areas where safety is critical. Moreover, oil-free technology aligns with environmental regulations and sustainability initiatives, as it minimizes the potential for oil spills and ensures cleaner air emissions.
3. Improved Equipment Reliability and Longevity
Mining operations often face harsh conditions, and equipment reliability is vital to maintain smooth operations. Oil-free air compressors, with their simplified design and reduced maintenance requirements, offer enhanced reliability and longevity. The absence of oil in the compression process results in lower wear and tear on components, translating to reduced downtime and maintenance costs.
4. Versatility and Adaptability
Oil-free air compressors come in various sizes and configurations, catering to a wide range of mining applications. Whether it’s pneumatic tools, dust control, ventilation, or material handling, these compressors can be tailored to meet specific needs. Their versatility allows for seamless integration into existing mining processes, making the transition to oil-free technology smoother for mining operators.
5. Noise Reduction
Mining sites are notorious for generating significant noise levels due to heavy machinery and equipment. Oil-free air compressors, known for their quieter operation compared to oil-injected compressors, contribute to a more comfortable and safer working environment for miners.
In conclusion, oil-free air compressors have redefined the role of compressed air in the mining industry. Their unique characteristics, including purity, environmental responsibility, safety, cost-effectiveness, and versatility, make them an ideal choice for modern mining operations.
As the demand for sustainable and efficient solutions continues to grow, oil-free air compressors will undoubtedly play a crucial role in enhancing mining productivity while upholding the highest standards of safety and environmental stewardship.
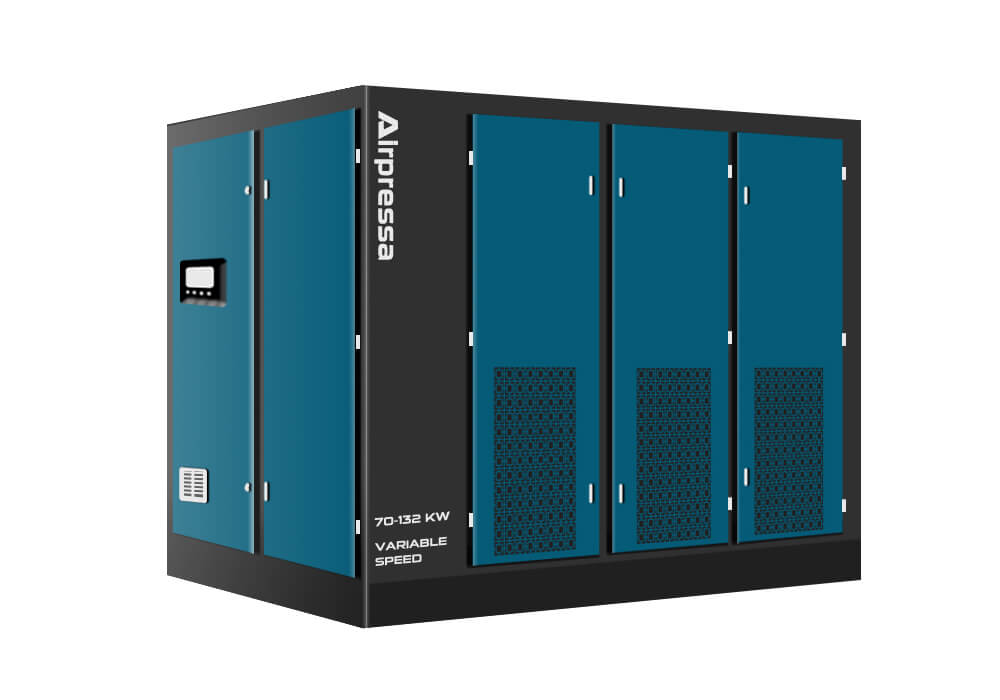
Variable Speed Compressors
By employing variable speed drive technology, these compressors optimize energy consumption by adjusting the motor’s speed according to the air demand.
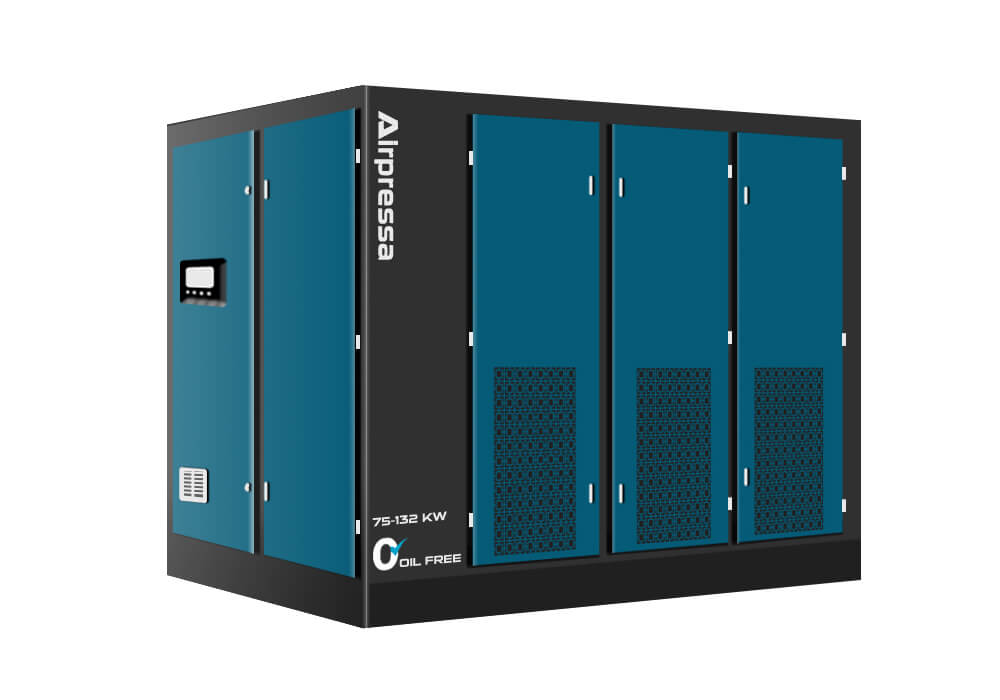
Oil-free Compressors
Oil free air compressors provide high-quality compressed air free from oil contamination, ensuring the integrity of sensitive processes and applications.
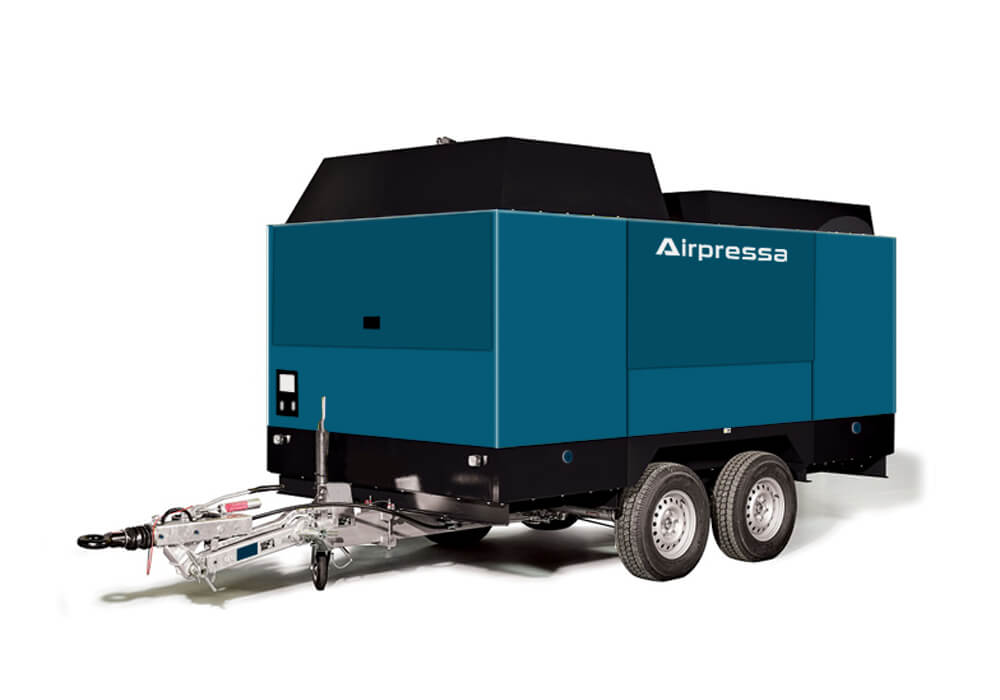
Diesel Portable Compressors
Diesel portable screw air compressor production lies in its wide application range, mobility, robust performance, efficient power output, and user-friendly maintenance.
Next, you need to take into account the performance, parameters and functions of the mining air compressor.
Optimizing Energy Consumption
Energy costs constitute a substantial portion of a mining operation’s expenses. With the implementation of variable speed screw air compressors, energy consumption is optimized, resulting in substantial savings. During periods of reduced air demand, the VSD technology lowers the motor speed, reducing energy consumption accordingly. This adaptive approach enables mining companies to minimize their carbon footprint and contribute to a more sustainable environment.
Matching Air Demand
Mining operations are dynamic, and air demand can vary significantly based on the tasks being performed. Traditional compressors struggle to cope with these fluctuations, leading to inefficiencies. VSD screw air compressors, on the other hand, excel at matching air supply with demand. By adjusting the compressor’s motor speed, they provide a continuous supply of compressed air at the required pressure, even during peak demand periods. This ensures uninterrupted productivity, allowing mining operations to run smoothly.
Reducing Operating Costs
In addition to energy savings, efficient screw air compressors also contribute to cost reduction in other ways. The minimized wear and tear on compressor components, thanks to the adaptive motor speed, result in extended equipment life and reduced maintenance costs. Moreover, the consistent and reliable performance of VSD screw compressors leads to decreased downtime, further optimizing overall operating expenses.
Remote Monitoring and Maintenance
Efficient air compression goes beyond just the equipment itself; it also involves smart monitoring and maintenance practices. Remote monitoring systems equipped with advanced sensors and connectivity options enable real-time performance tracking. This data-driven approach allows mining operators to identify potential issues early on, optimize system settings, and schedule maintenance proactively, minimizing downtime and maximizing productivity.
Maintenance Considerations for Mining Air Compressor
In the rugged and demanding environment of mining operations, air compressors play a crucial role in powering various pneumatic tools and equipment. These workhorses are subjected to extreme conditions, making regular maintenance and servicing vital to ensure their longevity and peak performance.
Understanding the Mining Environment
Mining sites are notorious for their harsh conditions, including dust, debris, moisture, and high temperatures. Air compressors operating in such environments face increased wear and tear. It is essential to recognize the specific challenges posed by the mining environment and tailor maintenance schedules accordingly.
Establishing a Comprehensive Maintenance Plan
A well-structured maintenance plan is the foundation for the efficient operation of mining air compressors. Regular inspections, cleaning, and lubrication are essential to prevent the buildup of contaminants that could compromise performance. Implementing a comprehensive maintenance schedule ensures that potential issues are addressed promptly, preventing costly breakdowns and production delays.
Regular Filter Replacements
Air compressors in mining environments are exposed to a significant amount of dust and particulate matter. As a result, air filters are prone to clogging and reduced efficiency. Regularly replacing air filters is imperative to maintain optimal airflow, prevent compressor strain, and extend the life of internal components.
Monitoring Oil Levels and Quality
Air compressors rely on lubricating oil to minimize friction and ensure smooth operation. Monitoring oil levels and quality is crucial to prevent equipment damage and ensure that the compressor operates efficiently. Regular oil analysis helps identify any potential contaminants or issues with oil degradation.
Examining Cooling Systems
Effective cooling is essential to prevent overheating of air compressors in mining applications. Dust and debris can accumulate on cooling fins, reducing their efficiency. Regular inspection and cleaning of cooling systems are vital to prevent overheating and maintain consistent performance.
Timely Repairs and Component Replacements
In mining operations, downtime is costly and can disrupt production schedules. Timely repairs and component replacements are critical to minimize downtime and keep the operation running smoothly. Regularly monitoring the performance of air compressors and addressing any arising issues promptly will help prevent major breakdowns.
Training for Maintenance Personnel
A knowledgeable and well-trained maintenance team is an invaluable asset to any mining operation. Providing proper training to maintenance personnel ensures that they can identify potential issues, carry out maintenance tasks correctly, and make informed decisions regarding repairs or replacements.
For more details on the maintenance of screw mining air compressors, please check this article: Air Compressor Maintenance Checklist: The Ultimate Manual
Get Expert Support
Choose Airpressa for all your compressed air needs and experience the benefits of working with a reliable, professional, and customer-focused manufacturer.