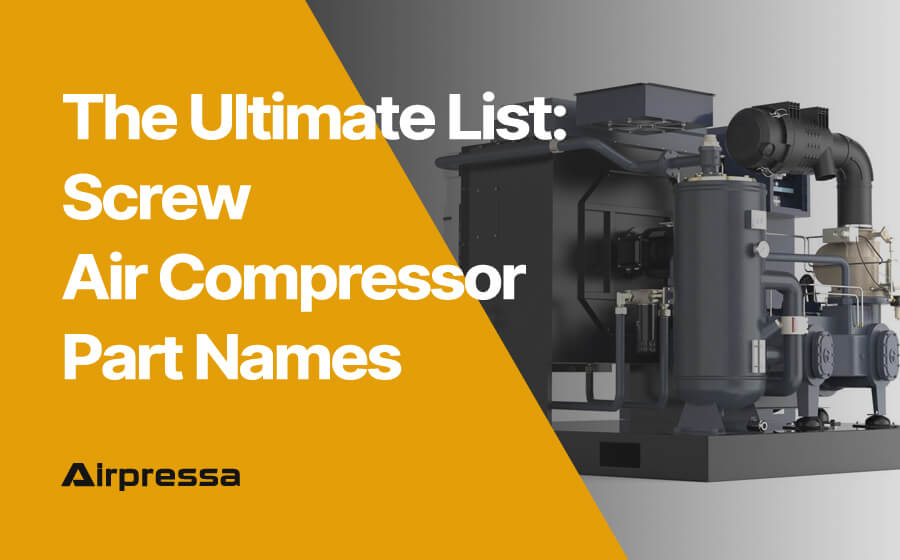
A screw air compressor is a complex machine with many parts that work together to produce compressed air. Each part plays a crucial role in the overall performance and efficiency of the compressor.
As such, it is essential to understand the different parts and their functions to properly maintain and repair the compressor.
In this article, we present the ultimate list of screw air compressor part and names, along with a brief description of each part and its function.
You can click on any compressor part name that you interest to get there quickly.
Air Intake Filter
The air intake filter is an essential screw air compressor part. Its primary function is to protect the compressor’s internal components from damage caused by airborne contaminants, such as dust, dirt, and other debris.
How Does it Work?
The air intake filter works by filtering the air that enters the compressor through a series of layers. As air enters the filter, it passes through a pre-filter that captures larger particles, such as dirt and debris.
The finer filter elements typically consist of pleated paper or synthetic media, which capture smaller particles such as dust and other contaminants.
As air passes through these elements, the contaminants become trapped in the filter media, allowing only clean air to enter the compressor.
Over time, the filter media becomes saturated with contaminants, reducing its effectiveness. For this reason, it is important to replace the air intake filter periodically, according to the manufacturer’s recommendations.
In addition to protecting the compressor’s internal components, the air intake filter also plays a role in maintaining the compressor’s efficiency.
When the filter becomes clogged with contaminants, it can restrict the airflow to the compressor, reducing its performance and increasing its energy consumption.
To ensure the proper operation of a screw air compressor, it is essential to use the correct air intake filter and to replace it regularly.
The replacement frequency will depend on factors such as the operating environment, the compressor’s usage, and the type of filter media used.
Air End
The air end is also a critical part in a screw air compressor. It consists of rotors, bearings, and shafts that work together to compress air.
Rotors
The rotors are the main working parts of the air end. They are two parallel, helical screws that rotate in opposite directions, trapping air between them and compressing it as it moves along the screws.
Rotors are precision machined to ensure that the clearance between them is minimal, which allows for maximum compression efficiency.
Bearings
The bearings are an essential part of the air end, providing support for the rotors and shafts. They are designed to handle high loads and ensure that the rotors rotate smoothly and efficiently.
In addition, bearings help to reduce vibration and noise, which can be a problem in some compressors.
Shafts
The shafts are also an integral part of the air end, providing the rotational power needed to turn the rotors. They are typically made of high-strength steel and are designed to withstand the stresses of continuous operation.
The air end works by drawing in air through the inlet port and compressing it between the rotors. As the air moves along the screws, the volume decreases, and the pressure increases.
Once the air has been compressed to the desired pressure, it is discharged through the outlet port and into the air receiver or distribution system.
The air end is a critical component in the operation of a screw air compressor, and it is essential to choose a high-quality air end for optimal performance and longevity.
More information about the screw compressor air end, you can view this article: What Is The Compressor Air End And How to Choose?
Intercooler
The intercooler is a heat exchanger that is used to cool the compressed air between the first and second stages of compression in a two-stage compressor.
As one of the air compressor components, the intercooler plays a critical role in the efficiency and performance of the compressor.
How Does it Work?
The intercooler works by using the incoming cool air from the atmosphere to cool down the hot compressed air. As the compressed air flows through the intercooler, it passes over a series of tubes where the incoming cool air is forced over the surface area. This cools down the hot compressed air and allows it to be compressed more efficiently in the next stage of compression.
During the screw air compression process, the air temperature rises due to the increased pressure. The hotter the compressed air is, the less dense it becomes, resulting in a reduced air output.
The intercooler addresses this problem by cooling the compressed air and reducing its temperature before it is sent to the second stage of compression.
The intercooler also helps to reduce the workload on the second stage of compression, which can improve the overall efficiency and lifespan of the compressor.
By reducing the temperature of the compressed air before it enters the second stage, the compressor doesn’t have to work as hard to compress the air to the desired pressure.
If you are looking to purchase a screw air compressor, make sure that it includes a high-quality intercooler as part of its design.
Aftercooler
Like the intercooler, the aftercooler is also a heat exchanger that cools the hot compressed air coming out of the compressor before it enters the air receiver tank.
The aftercooler plays a critical role in ensuring the efficient and safe operation of the compressor.
When the compressed air comes out of the compressor, it is hot and contains moisture and contaminants. The aftercooler cools the compressed air, causing the moisture to condense into water droplets that can be removed by a moisture separator.
This helps to protect downstream equipment, such as air dryers and filters, from damage caused by moisture and contaminants.
How Does it Work?
The aftercooler works by transferring the heat from the compressed air to a cooling medium, such as water or air.
In a water-cooled aftercooler, the compressed air flows through a tube surrounded by a jacket through which water flows. The heat from the compressed air is transferred to the water, which is then discharged into a cooling tower or other type of heat exchanger.
In an air-cooled aftercooler, the compressed air flows through a series of finned tubes, and the heat is transferred to the surrounding air, which is then vented outside.
It’s important to note that the aftercooler requires proper maintenance to function effectively. Over time, the aftercooler can become clogged with dirt, dust, and other contaminants, which can impede the flow of air or water and reduce the cooling capacity.
Regular cleaning and maintenance of the aftercooler is essential to ensure that the compressor operates at peak performance and that downstream equipment is protected.
Oil Cooler
The oil cooler in a screw air compressor is responsible for cooling the lubricating oil that flows through the compressor. The lubricating oil is used to reduce friction between the moving parts of the compressor, and it also helps to remove heat from the compression process.
How Does it Work?
The oil cooler is usually located in the oil circuit, and it works by using air or water to cool the oil. The oil is pumped through a series of small tubes, and a cooling medium flows over the tubes, removing the heat from the oil.
In air-cooled oil coolers, the cooling medium is usually air, and a fan is used to blow the air over the tubes.
In water-cooled oil coolers, the cooling medium is water, and the oil flows through a series of tubes that are immersed in a tank of water.
The oil cooler in a screw air compressor is critical to the proper functioning of the compressor.
If the oil temperature is too high, it can cause damage to the compressor, and if it is too low, it can cause the lubricating oil to break down, leading to accelerated wear on the compressor’s moving parts.
When selecting an oil cooler for a screw air compressor, it is essential to consider factors such as the compressor’s size, the operating environment, and the type of lubricating oil used.
A well-designed oil cooler will help to ensure the long-term reliability and performance of the screw air compressor.
Separator Element
The separator is responsible for separating the compressed air from the lubricating oil in the compressed air system.
The lubricating oil is used to lubricate the compressor’s bearings and other moving parts, and it can contaminate the compressed air if not properly separated. This is where the separator element comes in.
The separator element is a filter that removes the oil particles from the compressed air. It is typically made of a fibrous material that traps the oil droplets as they pass through.
How Does it Work?
The separator element works by creating a pressure drop across the filter element. As the compressed air flows through the filter, the oil droplets are trapped by the fibrous material, while the clean air passes through. The separated oil is collected at the bottom of the housing and drained from the system.
The size of the oil droplets that the separator element can remove depends on the element’s pore size. In general, a smaller pore size means better oil removal, but it also means a higher pressure drop across the element.
It typically consists of a housing, which contains the filter element, and a drain valve, which removes the separated oil.
The housing is usually made of aluminum or steel and is designed to withstand the high pressures and temperatures of the compressed air system.
The drain valve is typically located at the bottom of the housing and allows the separated oil to be drained from the system.
The filter element can become clogged with oil and other contaminants, leading to reduced oil separation and increased pressure drop across the element. This can result in decreased compressor performance and increased energy consumption.
So, regular replacement of the separator element is necessary to ensure that the compressor system remains efficient and effective.
Oil Filter
The oil filter is a crucial part of a screw air compressor that helps to maintain the quality of the compressor oil by removing any contaminants that may be present.
The filter is typically located within the oil system of the compressor and is responsible for removing impurities such as dust, debris, and metal particles that can cause damage to the compressor.
How Does it Work?
The oil filter works by allowing the oil to pass through a series of fine mesh screens, which trap any contaminants that may be present. As the oil flows through the filter, the contaminants are gradually removed, and the oil is returned to the compressor system in a purified state.
This process ensures that the oil is kept clean and free of impurities, which helps to maintain the efficiency and longevity of the compressor.
It is essential to maintain the oil filter regularly to ensure it continues to work effectively. The frequency of maintenance will depend on the type of compressor, its usage, and environmental factors.
Typically, oil filters should be replaced every 3-6 months, but it is recommended to check the manufacturer’s guidelines for specific maintenance instructions.
Oil Pump
The oil pump is responsible for circulating oil throughout the compressor system to lubricate the moving parts and prevent friction and wear.
How Does it Work?
In a screw air compressor, the oil pump is typically located at the bottom of the compressor and driven by a motor. The oil pump draws oil from the oil reservoir and pumps it into the compressor’s main oil circuit, where it lubricates the rotors, bearings, and other moving parts.
The oil pump in a screw air compressor is designed to operate continuously and maintain the required oil pressure to ensure proper lubrication.
If the oil pressure drops below the required level, it can cause damage to the compressor’s moving parts, leading to premature wear and reduced lifespan.
Motor
What is the Motor in a Screw Air Compressor?
The motor is the core source of power for a screw air compressor, and it is responsible for generating the torque necessary to drive the compressor’s rotor.
How Does it Work?
The motor in a screw air compressor typically operates using an induction motor design.
- Induction motors work by generating a rotating magnetic field within the motor’s stator.
- The magnetic field induces a current in the rotor, causing it to spin.
- The rotor is attached to the motor’s shaft, and as the motor spins the shaft, it rotates the rotor.
The motor’s speed is controlled by the compressor’s control system, which varies the frequency of the electrical supply to the motor. By varying the frequency, the control system can adjust the motor’s speed to match the compressor’s demand for compressed air.
There are different types of motors used in screw air compressors, including:
AC Motors: AC motors are the most common type of motor used in screw air compressors. They operate using alternating current (AC) and are available in single-phase or three-phase designs.
DC Motors: DC motors operate using direct current (DC) and are less common in screw air compressors. They are typically used in applications where precise speed control is required.
Variable Frequency Drive (VFD) Motors: VFD motors are designed to operate using a variable frequency drive, which allows the motor’s speed to be adjusted to match the compressor’s demand for compressed air.
Click to check our variable speed compressors.
Drive system
The drive system of a screw air compressor is responsible for transmitting power from the motor to the compressor’s rotors. It consists of belt, pulley, and coupling that work together to transfer energy efficiently and reliably.
Belt
The belt is one of the most important components of the drive system. They are made of durable materials such as rubber and are responsible for transmitting power from the motor to the compressor.
There are different sizes and shape of belts, and choosing the right one depends on the compressor’s power requirements and the type of motor used.
In fact, with the rapid development of technology today, belt drive air compressors have almost been eliminated and replaced by direct drive air compressors.
Pulley
The pulley is another component of the drive system. They work together with the belts to transfer power from the motor to the compressor.
Pulley is designed to provide the required speed and torque to the compressor rotors. The size and shape of the pulleys are determined by the type of motor used and the compressor’s power requirements.
Coupling
The coupling is used to connect the motor and the compressor’s rotors. It allows for the transfer of energy between the two components while also absorbing any misalignment between them.
Couplings come in different types, including rigid, flexible, and fluid, each designed for specific applications.
Maintenance of the drive system is essential for ensuring its proper operation and longevity. This includes inspecting the belts for wear and tear, checking the pulleys for alignment and balance, and ensuring the couplings are properly lubricated and aligned.
Safety Relief Valve
The safety relief valve is an essential part in air compressors that plays a crucial role in ensuring the safe operation of the system.
A safety relief valve is typically installed at the highest point in the compressed air system, where pressure is most likely to build up. It is designed to open and release compressed air when the pressure in the system exceeds the predetermined level.
This release of pressure prevents the system from becoming over-pressurized, which can cause damage to the compressor and other system components, as well as potential safety hazards.
In addition to preventing damage to the air compressor and system, the safety relief valve also protects personnel from potential accidents.
If the air compressor system were to become over-pressurized, it could rupture or explode, causing serious injury or even death. The safety relief valve ensures that the pressure is released in a controlled manner, reducing the risk of injury and damage.
It is important to note that the safety relief valve must be correctly sized and installed for the specific application. The valve must be capable of handling the maximum pressure of the system and must be installed in accordance with manufacturer guidelines and local regulations.
Testing the safety relief valve are also essential to ensure its proper function. The valve should be inspected and tested periodically to ensure that it opens at the correct pressure and that there are no leaks or other issues that could compromise its function.
Drain Valve
The drain valve is responsible for removing accumulated condensate from the compressed air system. Condensate is a natural byproduct of compressed air systems and is a result of the air cooling and condensing as it passes through the air compressor system.
Drain valves can be either manual or automatic and are designed to prevent water and other contaminants from accumulating in the compressed air system.
If not removed, the condensate can damage the air compressor, downstream equipment, and even the finished products of the compressed air system.
Manual drain valves are operated manually by the operator, whereas automatic drain valves are controlled by a timer or a sensor that detects the amount of condensate in the system.
Automatic drain valves offer several advantages over manual drain valves, such as more reliable and consistent operation and reduced risk of human error.
There are various types of automatic drain valves available in the market, including electronic level sensing drains, timer controlled drains, and zero loss drains.
Electronic level sensing drains use sensors to detect the amount of condensate in the system and open and close the valve accordingly.
Timer controlled drains operate on a set schedule, while zero loss drains use a solenoid valve to discharge the condensate while keeping the compressed air in the system.
When choosing a drain valve for your screw air compressor, it is essential to consider the type of condensate the size of the compressed air system, and the application for which the compressed air will be used.
Control Panel
The control panel houses a variety of gauges, sensors, and control valves that help maintain the proper functioning of the compressor. And it helps the compressor to operate safely and efficiently by monitoring various parameters such as temperature, pressure, and flow rates.
Pressure Gauge
One of the most important components of the control panel is the pressure gauge.
The pressure gauge measures the pressure of the compressed air inside the compressor tank and displays it on the panel. The operator can then adjust the pressure according to the specific requirements of the application.
Temperature Sensor
Another key component of the control panel is the temperature sensor.
The temperature sensor measures the temperature of the compressed air as it enters and exits the compressor. This is important because high temperatures can damage the compressor components and reduce its lifespan.
The control panel also houses various control valves that help regulate the flow of compressed air. These valves can be manually or automatically controlled and are essential for maintaining the proper operating conditions of the compressor.
In addition to these components, the control panel may also feature other important controls such as a compressor on/off switch, overload protection, and emergency stop buttons.
The control panel allows the operator to monitor and control various parameters, which helps to prevent damage to the compressor and ensure consistent performance.
With the right control panel components in place, a screw air compressor can operate reliably for years to come.
Sound Enclosure
When talk about screw air compressors, one of the main concerns for many users is the noise level.
Operating at high speeds and with powerful motors, these machines can generate a lot of noise, which can be a nuisance for workers. That’s where sound enclosures come in – can significantly reduce the noise level of a screw air compressor.
So, what is a sound enclosure? Simply put, it’s an additional structure that surrounds the compressor unit and helps to muffle the noise it produces.
These enclosures are typically made of high-density materials, such as steel or aluminum, and are designed to be sturdy and durable enough to withstand the vibration and heat generated by the compressor.
How Does it Work?
The sound enclosure uses a combination of sound-absorbing materials and clever engineering to reduce the noise level of the compressor.
The walls of the enclosure are lined with acoustic foam or other sound-absorbing materials, which help to absorb the sound waves produced by the compressor and prevent them from escaping.
Its enclosure also features sound baffles and other design features that help to redirect and dissipate the sound waves, further reducing the noise level.
The sound enclosure is not a standard part on all screw air compressors – they are often offered as an optional add-on. However, for users who are concerned about noise levels, they can be a worthwhile investment.
By reducing the noise level of a compressor, a sound enclosure can create a more comfortable and productive working environment, while also minimizing the risk of noise-related health issues for workers.
This air compressor part list is not exhaustive, and some compressors may have additional or different parts. It’s always a good idea to consult the manufacturer’s manual for a comprehensive list of parts and their specifications.