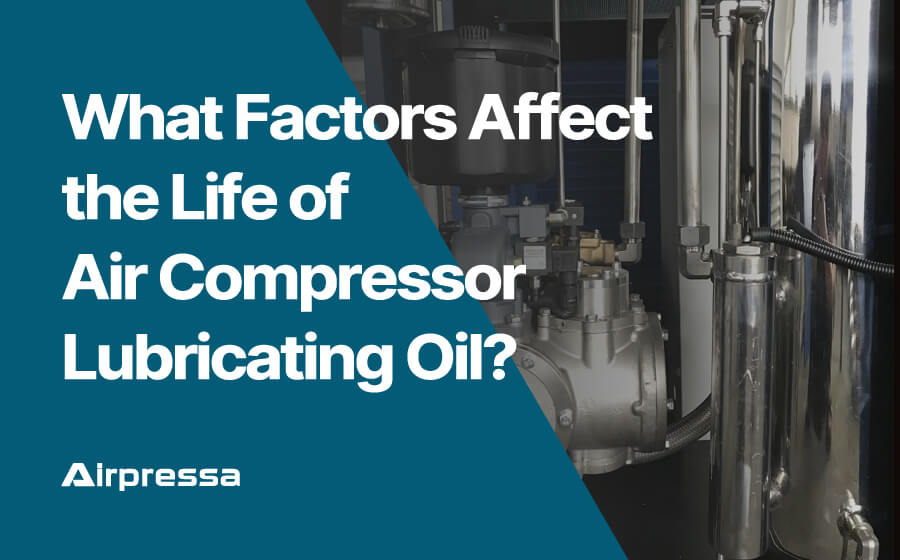
Air compressors are essential in various industrial applications, and their smooth operation heavily relies on the quality of lubricating oil used.
Lubricating oil can reduce friction and wear between mechanical parts, lowering operating temperatures, preventing rust and corrosion, and providing cleaning and sealing functions.
However, the life of lubricating oil is not indefinite. Several factors influence its performance and longevity. Understanding these factors is critical to ensuring the efficient operation of air compressors and extending the life of the lubricating oil.
You can click on any section that you interest to get there quickly.
Why Air Compressor Lubricating Oil is So Important
Enhancing Efficiency
Proper lubrication could reduce friction and wear, then the compressor operates more smoothly and consumes less energy.
Preventing Downtime
Unexpected breakdowns can be costly and disruptive. Regular use of high-quality lubricating oil can prevent common issues such as overheating, component wear, and contamination.
This proactive maintenance reduces the likelihood of unexpected failures and the associated downtime, ensuring continuous and reliable operation.
Extending Equipment Lifespan
Air compressor lubricating oil protects vital components from premature wear and damage, significantly extending the service life of the equipment.
Cost Savings
While the initial cost of high-quality lubricating oil may be higher, the long-term savings are substantial. Efficient operation reduces energy consumption, fewer breakdowns lower maintenance and repair costs, and extended equipment lifespan means less frequent replacements.
Overall, proper lubrication translates to significant cost savings over the life of the air compressor.
Ensuring Safety
Safety is paramount in any industrial setting. Overheated or malfunctioning compressors can pose serious risks, including fires or explosions.
Air compressor lubricating oil helps maintain safe operating temperatures and prevents mechanical failures that could lead to dangerous situations.
Regular maintenance with the right oil ensures that the compressor operates safely within its designed parameters.
Therefore, the selection and maintenance of air compressor lubricating oil are equally important. So, what factors affect its use and life?
Quality of Lubricating Oil
The quality of the lubricating oil used in air compressors is a primary factor in determining its lifespan.
High-quality oils have superior oxidation stability, wear protection, viscosity-temperature characteristics, and anti-emulsification properties. These attributes ensure the oil performs well under extreme conditions like high temperatures and pressures.
In contrast, lower-quality oils may contain impurities and water, leading to faster oxidation and degradation, reducing viscosity and increasing acidity. Choosing the right lubricating oil is essential for optimal compressor performance and longevity.
- Oxidation Stability: High-quality oils resist oxidation better.
- Wear Protection: Superior oils provide better protection against wear.
- Viscosity Characteristics: High-quality oils maintain performance across temperature ranges.
Anti-Emulsification: Quality oils resist water contamination.
Most air compressor manufacturers will recommend using synthetic lubricants rather than mineral oils.
What Are the of Air Compressor Oil Types? Which One is Better?
Air compressor oil and types are critical component in ensuring the efficient operation and longevity of compressors. Understanding the role of lubricating oil in air compressors and its importance can help users maintain their equipment more effectively.
Operating Temperature
Operating temperature significantly impacts the life of compressor lubricating oil. High temperatures accelerate the oxidation process, causing the oil to break down more quickly. This leads to the formation of sludge and varnish, which can clog filters and reduce lubrication efficiency.
Conversely, low temperatures can increase oil viscosity, making it harder for the oil to flow and lubricate parts effectively. Maintaining optimal operating temperatures is essential to prolong the life of the lubricating oil.
Environmental Factors
Environmental contamination is another critical factor that affects lubricating oil life. Particulate matter, water, and other contaminants can significantly degrade oil performance.
Particles can cause abrasive wear on components, while water can lead to emulsification, reducing the oil’s lubricating properties.
Moreover, high ambient temperatures can accelerate oil oxidation, while high humidity levels can introduce water contamination. Dusty environments can increase the load on filters and potentially allow more contaminants into the oil.
- Temperature Control: Maintain a stable operating environment.
- Humidity Management: Prevent water contamination through dehumidification.
- Dust Control: Use proper filtration to keep contaminants out.
Load and Pressure Conditions
The load and pressure conditions under which the compressor operates also affect the life of the lubricating oil. Higher loads and pressures can increase the oil’s operating temperature, accelerating oxidation and degradation.
Operational Management
Proper operational management also significantly influences the lifespan of compressor lubricating oil.
Excessive load operations can lead to high oil temperatures, accelerating oxidation and degradation. Frequent starts and stops can keep the oil in a high-temperature working state for extended periods, increasing its aging process.
Therefore, it’s essential to adjust operating parameters based on the compressor’s workload and conditions to avoid overloading and frequent starts and stops.
Oil Change Intervals
You should follow the oil change intervals recommended by the air compressor manufacturer.
Overextending oil change intervals can lead to the accumulation of contaminants and degradation products, reducing the oil’s effectiveness. Conversely, changing oil too frequently can be costly and unnecessary.
Maintenance and Care
Timely replacement of filters and oil filters effectively removes impurities and contaminants from the air, preventing them from entering the lubrication system and contaminating the lubricating oil.
Regular inspection and cleaning of the cooling system help maintain good heat dissipation performance, avoiding overheating that can lead to oil oxidation and degradation.
- Filter Maintenance: Regularly change filters to remove impurities.
- Cooling System: Ensure efficient heat dissipation to prevent oil degradation.
- Oil Checks: Monitor oil levels and quality, replenishing as necessary.
- Scheduled Maintenance: Follow a structured maintenance plan.
Conclusion
The life of air compressor lubricating oil is influenced by several critical factors, including maintenance practices, operational management, oil quality, and environmental conditions.
By understanding and addressing these factors, it is possible to ensure the efficient operation of air compressors and extend the life of the lubricating oil.
Implementing regular maintenance schedules, managing operating conditions, choosing high-quality oil, and controlling environmental factors are all essential steps in achieving this goal.