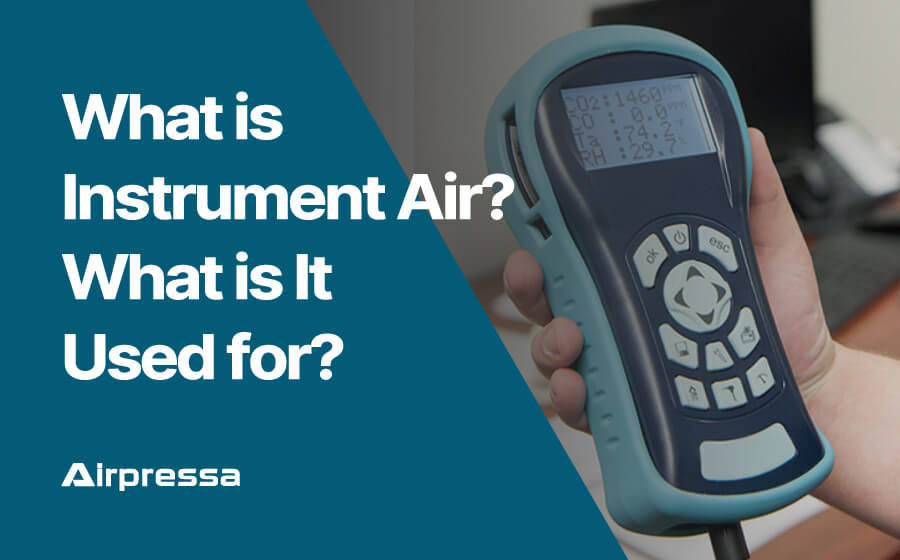
Instrument air is a very important concept in compressed air systems.
The oil and gas industry in particular has the highest demand for instrument air and instrument air packages among the compression systems Airprssa has sold and installed in the past.
You can click on any section that you interest to get there quickly.
What is Instrument Air?
Instrument air is a supply of compressed air that is treated and conditioned for use in process control instruments and equipment. The treatment usually involves removing moisture, oil, and other contaminants that could potentially interfere with the operation of the instruments.
In practical settings, instrument air is used to actuate control valves, drive pneumatic tools, operate air motors, perform purging, and a variety of other functions within industrial applications.
The critical characteristic of instrument air is its high purity, which is essential to maintain the accuracy and reliability of pneumatic controls and instrumentation.
It’s crucial to maintain the quality of instrument air as substandard or contaminated air can result in the malfunction of delicate equipment, leading to potential safety concerns and negatively impacting the overall efficiency of an operation.
The specifications and standards for instrument air are often defined by industry bodies and may vary based on the specific application and industry.
What is the Difference Between Instrument Air and Industrial Compressed Air?
While both instrument air and common industrial compressed air are essential components in many industries, they serve distinct purposes and possess different characteristics.
Instrument Air
Its primary use is to actuate control valves and pneumatic instruments. This form of air is carefully treated and conditioned to be free from contaminants such as moisture, dust, and oil particles.
Often, instrument air has a pressure in the range of 3-15 psig. The high level of purity in instrument air is critical for ensuring the accurate and reliable functioning of delicate instruments and control systems.
Industrial Compressed Air
Comparatively, industrial compressed air, often also referred to as plant air or process air, has more general usage across various industrial processes.
This means its treatment may not be as stringent as that of instrument air. Its use includes powering pneumatic tools, cleaning equipment, and other more general applications within an industrial environment.
The key difference between the two, therefore, lies in their purity levels and the applications for which they are used. Instrument air needs to be cleaner and more controlled due to its usage in sensitive equipment, whereas industrial compressed air might contain more contaminants and be used for broader functions.
What Are the Instrument Air Uses and Industries?
Instrument air has a wide array of uses across multiple industries due to its high purity and reliable performance. Here are some significant industries and corresponding uses for instrument air:
Oil and Gas Industry
The most common application for instrument air is in the oil and gas industry.
It plays a pivotal role in achieving safety, efficiency, and reliability in various operations. Here are a few uses instrument air is utilized in the oil and gas sector:
1. Actuation of Control Valves
The precise operation of control valves is crucial in the oil and gas industry. Instrument air, with its high purity, is used to actuate these valves, thereby controlling the rate of flow, pressure, and other parameters in the pipeline systems.
2. Operational Safety
The instrument air is an inert gas, reducing the probability of explosions or fires in potentially hazardous environments like oil rigs. This attribute makes it suitable for use in pressurizing equipment enclosures and providing a safe atmosphere.
3. Gas Flaring and Venting
In oil extraction and processing, instrument air is used in gas flaring. Flaring is a method used to safely burn off flammable gas released by pressure relief valves during unplanned over-pressuring of plant equipment.
4. Sandblasting and Surface Preparation
In the maintenance of ship and oil platform structures, instrument air can be used in sandblasting processes. The high-pressure, clean, and dry air stream is ideal for removing rust and preparing surfaces for repainting.
Instrument air reduces the risk of explosions and fires in high-risk environments with its inherent safety properties.
Chemical Industry
In chemical plants, instrument air is frequently used in pneumatic control. It operates pneumatic control valves and dampers which regulate the flow of fluids in pipelines and process systems. This aids in maintaining precise control over the plant processes.
Power Generation
Instrument air is vital in power plants, especially in the operation of turbines. The clean, dry air helps cool certain components and also actuates several control mechanisms to achieve optimal power output.
Pharmaceuticals
In pharmaceutical manufacturing, instrument air works as a clean and safe power source for various process control systems. Given the demanding environment of pharmaceutical manufacturing, a reliable source of high-purity air like instrument air is crucial.
How to Get the Instrument Air?
To produce high-quality instrument air, several stages of air treatment involving various machines and equipment are necessary to ensure its cleanliness and dryness.
1. Initial Filtration
In the initial stage, a pre-filter is usually installed at the air compressor’s outlet. This aids in removing large particles, water, and oil droplets from the compressed air.
2. Condensate Separation
The instrument air often contains moisture which can interfere with the functioning of sensitive equipment. An automatic condensate separator is utilized to remove the bulk of this water vapor.
3. Drying
Equip your air compressor with an air dryer.
Air dryers remove moisture from compressed air to a large extent and improve air quality.
What Is The Compressed Air Dryer? A Comprehensive Overview
What is the Compressed Air Dryer?
Types of Compressed Air Dryer
Components of Compressed Air Dryers
How to Choose the Right Compressed Air Dryer
Compressed Air Dryer Common Faults
4. Instrument Air Package
Instrument air packages include varying numbers of duct air filters. And divided into several levels:
Q’ grade air filters
‘P’ grade air filters
‘M’ grade air filters
‘S’ grade air filters
‘H’ grade air filters
The combination of these air filters will remove tiny particles, dust, or residual oil droplets that could interfere with the air-powered instruments and control systems. They can greatly improve the quality of compressed air.
The air filters could be coalescing filters or activated carbon filters, depending upon the required air quality.
Compressed Air Filter System: Air Treatment Guide
The compressed air filter system is an essential component of almost every air compression system. As an important air treatment system, it can provide cleaner aerodynamics for manufacturing and projects.
5. Regular Maintenance
Thorough and regular maintenance is necessary for each component of the instrument air unit. For example, treated paper elements in filters should be discarded and replaced periodically for the best results.
The Importance of the Dew Point for Instrument Air Quality
Essentially, the dew point refers to the temperature at which the moisture in the air begins to condense into water droplets.
This is crucial for instrument air systems for several reasons:
Prevent Contamination
High dew points indicate higher moisture content in the air. This is problematic because moisture can lead to the formation of rust or corrosion in the air compression system and connected components, leading to contamination and inefficient operation.
Avoid Freezing
Particularly for outdoor systems exposed to cold environments, ensuring a low dew point is of paramount importance. If the dew point temperature is above the ambient temperature, moisture within the air can freeze within the piping, causing blockages and potential damage.
Ensure Efficiency
Keeping a low dew point can help ensure that pneumatic systems operate efficiently and reliably. Moisture can interfere with the effectiveness of pneumatic controls and lead to faulty readings.
Preserve System Life
By maintaining an appropriate dew point, the overall lifespan of the instrument air system can be considerably prolonged. The avoidable moisture-related issues can otherwise lead to frequent maintenance needs and potential early system replacement.
Therefore, maintaining a suitable dew point by using an effective air drying system is key to high-quality instrument air. It helps ensure a reliable, efficient operation while protecting the compressed air system‘s integrity and longevity, ultimately leading to cost savings and better productivity.
What Is Pressure Dew Point? Why Is It So Important?
Pressure dew point is a key term that must be mentioned in the air compressor industry. It plays a vital role in the entire compressed air system, connected equipment and applications.
Different from atmospheric dew point, pressure dew point has more practical application significance. So, what is pressure dew point and why is it so important?
How to Find the Right Dew Point for Instrument Air?
Determining the appropriate dew point for your instrument air system greatly depends on your specific application and the environmental conditions present where your air compression system is located. Here are some general steps to help you find the right dew point:
Identify Your Operational Requirements
Different applications require different air quality standards depending on the sensitivity of the equipment and the air’s end use. For example, sensitive instruments may need a lower dew point to prevent damage.
Consider Environmental Conditions
The operating environment can significantly affect the choice of the dew point. If the system is installed in a high humidity location or where temperatures can drop significantly, a lower dew point may be necessary to prevent condensation.
Consult Industry Standards
Various industry standards, such as ISO 8573-1, provide guidance on the optimal instrument air quality, including a recommendation for the dew point. Consulting these standards can offer a benchmark for your system.
Check Manufacturer Specifications
Instrument manufacturers often provide specifications or guidelines for the quality of air that should be used. These might include specific dew point recommendations.
Seek Expert Advice
If you’re uncertain about your specific needs, consider consulting with an air compressor specialist or supplier. They can provide tailored advice based on their experience with similar applications.