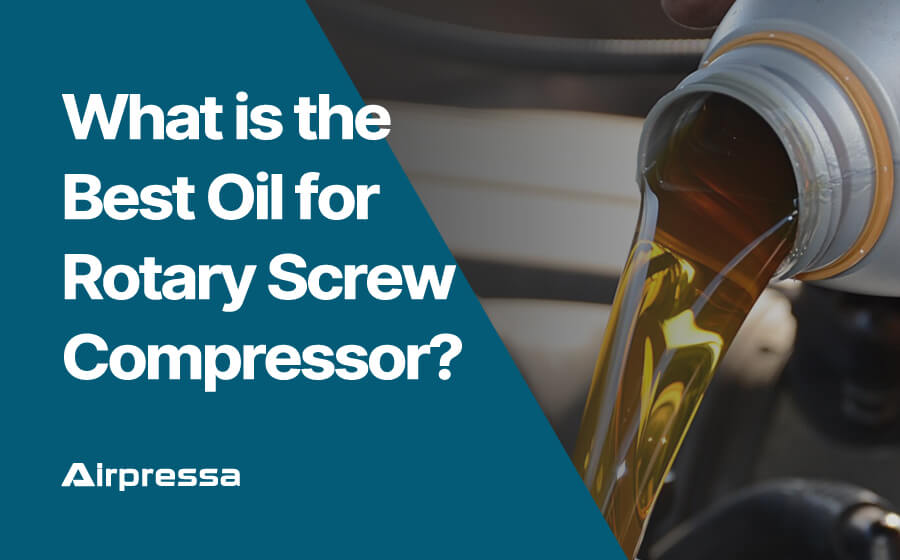
Choosing the right oil for rotary screw compressor is crucial for maintaining its performance, efficiency, and longevity. The type of oil used can significantly impact the operation and maintenance requirements of the compressor.
This article compares fully synthetic, semi-synthetic, and mineral oil, providing insights into their benefits and drawbacks to help you make an informed decision.
You can click on any section that you interest to get there quickly.
Fully Synthetic Oil
Fully synthetic oil is a man-made lubricanting oil. It is chemically engineered from base oils and a tailored blend of additives to meet specific performance criteria.
These base stocks are often derived from chemically modified petroleum components or entirely synthetic compounds such as polyalphaolefins (PAOs) or esters.
The process of creating these base stocks involves refining them to a much higher degree than conventional mineral oils, removing impurities and allowing for the design of molecules that provide specific performance characteristics.
Manufacturers can produce synthetic oil with precise properties and performance characteristics.
Properties and Benefits
Superior Performance
Fully synthetic oils are engineered for optimal performance. They offer excellent thermal stability, allowing them to withstand higher temperatures without breaking down.
Extended Lifespan
These oils have a longer service life compared to mineral and semi-synthetic oils. They require fewer changes, reducing maintenance intervals and downtime.
Enhanced Lubrication
Synthetic oils provide superior lubrication, reducing friction and wear on compressor components. This leads to improved efficiency and a longer lifespan for the compressor.
Cleaner Operation
They produce fewer deposits and sludge, keeping the internal components of the compressor cleaner. This reduces the risk of blockages and improves overall performance.
Drawbacks
Higher Cost
The main disadvantage of fully synthetic oils is their higher cost compared to mineral and semi-synthetic oils. However, the extended lifespan and reduced maintenance can offset this initial expense over time.
Compatibility Issues
In some cases, fully synthetic oils may not be compatible with older compressors or certain seal materials. It is essential to check the manufacturer’s recommendations before switching to synthetic oil.
Semi-Synthetic Oil
Semi-synthetic oils are created by mixing high-quality mineral oils with synthetic base stocks.
The combination results in a lubricant that offers enhanced performance characteristics compared to pure mineral oils, though not as advanced as fully synthetic oils.
This blend aims to provide many of the benefits of fully synthetic oils while maintaining a more affordable price point.
The exact proportion of synthetic to mineral oil can vary, but typically, semi-synthetic oils contain 10% to 30% synthetic oil.
Properties and Benefits
Balanced Performance
Semi-synthetic oils are a blend of mineral and synthetic oils. They offer a balance between performance and cost, providing better lubrication and thermal stability than mineral oils but at a lower cost than fully synthetic oils.
Improved Lifespan
Semi-synthetic oils last longer than mineral oils, reducing the frequency of oil changes and associated maintenance costs.
Good Lubrication
They provide better lubrication than mineral oils, which helps in reducing wear and improving the efficiency of the compressor.
Drawbacks
Moderate Cost
While cheaper than fully synthetic oils, semi-synthetic oils are more expensive than mineral oils. The cost-benefit ratio should be considered based on the specific application and operating conditions.
Performance Limitations
Semi-synthetic oils do not perform as well as fully synthetic oils in extreme conditions. For high-temperature or high-load applications, fully synthetic oils may still be the better choice.
Mineral Oil
Mineral lubricating oil, often referred to as conventional oil, is derived directly from refining crude oil. It is the most basic type of lubricating oil and has been used extensively in various industrial and automotive applications for many years.
While it lacks some of the advanced properties of synthetic oils, it remains widely used due to its cost-effectiveness and adequate performance in many standard applications.
Properties and Benefits
Cost-Effective
Mineral oils are the most affordable option, making them suitable for applications where budget constraints are a significant factor.
Sufficient for Standard Applications
These oils provide adequate lubrication and protection for standard air compressor operations under moderate conditions.
Drawbacks
Shorter Lifespan
Mineral oils break down faster than synthetic oils, requiring more frequent oil changes. This can increase maintenance costs and downtime.
Lower Performance
They do not perform as well as synthetic oils in high-temperature or high-load conditions. This can lead to increased wear and potential overheating issues.
Higher Deposit Formation
Mineral oils tend to produce more deposits and sludge, which can clog internal components and reduce the efficiency of the compressor.
Conclusion
The best oil for a rotary screw compressor depends on the specific needs and operating conditions of the compressor.
Fully synthetic oils offer superior performance, longer lifespan, and cleaner operation but come at a higher cost.
Semi-synthetic oils provide a good balance of performance and cost, making them suitable for many applications.
Mineral oils are the most cost-effective but require more frequent changes and may not perform as well in demanding conditions.
For most industrial applications, fully synthetic oil is recommended due to its long-term benefits and superior performance.
However, for budget-conscious operations, semi-synthetic oils offer a practical alternative, providing enhanced performance over mineral oils without the higher cost of fully synthetic options.
Always consult the compressor manufacturer’s recommendations to ensure compatibility and optimal performance.
What Are the of Air Compressor Oil Types? Which One is Better?
Air compressor oil and types are critical component in ensuring the efficient operation and longevity of compressors. Understanding the role of lubricating oil in air compressors and its importance can help users maintain their equipment more effectively.
Why Should You Use Synthetic Oil for Compressors?
Whether it is the compressor manufacturer, dealer or training expert, they always recommend synthetic lubricating oil.
There are several reasons:
Superior Thermal Stability
Synthetic oils are engineered to withstand higher temperatures without breaking down. This thermal stability is more conducive to rotary screw compressors operate under high heat conditions.
Unlike mineral oils, synthetic oils maintain their viscosity and lubricating properties even at elevated temperatures, ensuring consistent performance and protection against wear.
Extended Oil Life
One of the most significant advantages of synthetic oils is their extended service life. Synthetic oils degrade much slower than their mineral counterparts, allowing for longer intervals between oil changes.
This means less downtime for maintenance and lower overall maintenance costs, making synthetic oils a cost-effective choice in the long run.
Enhanced Lubrication
The molecular structure of synthetic oils is designed to provide superior lubrication.
They form a robust lubricating film that reduces friction and wear between moving parts. This is particularly beneficial for rotary screw compressors, where the reduction in friction can lead to smoother operation and enhanced efficiency.
Reduced Deposit Formation
Synthetic oils are less prone to forming deposits such as sludge and varnish. These deposits can clog components and reduce the efficiency of the compressor. By using synthetic oil, you can ensure a cleaner operation, which translates to better performance and less frequent maintenance.
Most final users or projects always hope the rotary screw compressor can non-stop work even 24h. In this case, synthetic oils are significantly better than mineral oils at this time.
Improved Cold Start Performance
Synthetic oil has superior flow characteristics at low temperatures. This improved cold start performance means that the oil can circulate more quickly during startup, providing immediate protection to the compressor components.
Synthetic oil will prevent the wear and tear during the initial moments of operation when the risk of damage is highest.
Better Environmental Performance
Many synthetic oils are formulated to be more environmentally friendly. They can be designed to have lower volatility, reducing oil consumption and emissions.
Compatibility with High Performance Compressors
Modern rotary screw compressors are often designed with tighter tolerances and higher performance expectations. Synthetic oils are typically more compatible with these advanced designs, providing the necessary lubrication and protection without compromising on efficiency or causing compatibility issues.
While synthetic oils may have a higher upfront cost compared to mineral oils, their long-term benefits far outweigh the initial investment.
By ensuring optimal performance and reducing maintenance requirements, synthetic oils contribute to the overall efficiency and reliability of rotary screw compressors.
For anyone looking to maintain their compressor in top condition and maximize its operational lifespan, synthetic oil is the recommended option.
The Best Oil for Rotary Screw Compressor
Obviously, for most rotary screw air compressors, synthetic oil is the best choice. Although the purchase cost of mineral oil is lower, once the compressor efficiency decreases or even fails, it will not be worth it.
In addition, the viscosity of the lubricating oil should be 46 or 68 (based on ISO VG@40C CST).
Of course, you should carefully follow the recommendations in the manufacturer’s instructions or warranty.