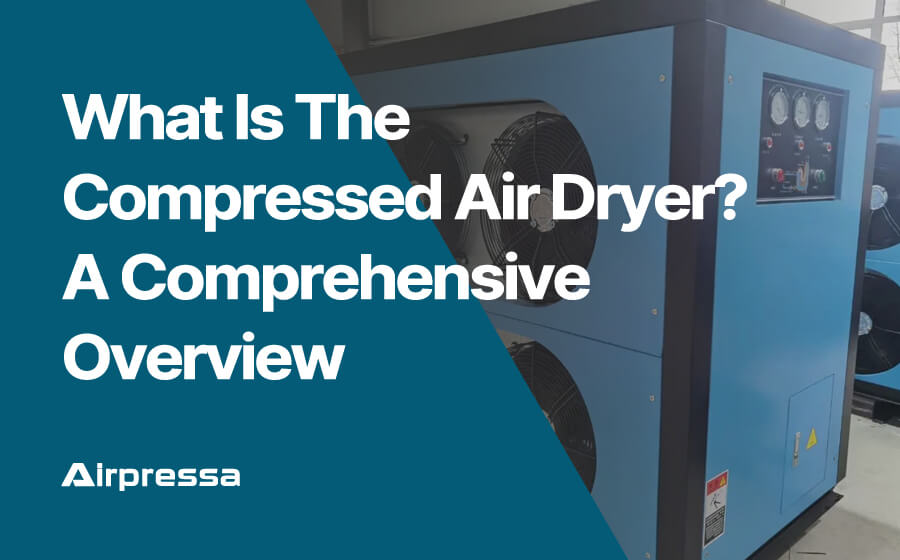
The compressed air dryer is an important part of air compression system, it ensures the quality and efficiency of compressed air systems.
Let’s delve into what a compressed air dryer is and why it’s a crucial component in various industries.
You can click on any section that you interest to get there quickly.
What is the Compressed Air Dryer?
The compressed air dryer is a device designed to remove moisture and contaminants from compressed air.
When air is compressed, its temperature rises, causing the moisture it carries to condense. If this moisture isn’t adequately removed, it can lead to corrosion in pipelines, damage to pneumatic tools, and compromise the quality of end products in manufacturing processes.
Types of Compressed Air Dryer
Let’s explore the three main types of compressed air dryers and understand how they work and where they find application.
Refrigerated Air Dryer
Working Principle
Refrigerated air dryers operate by cooling the compressed air to low temperatures, causing much of the water vapor to condense. The cooled air is then reheated to room temperature upon exiting the dryer before being used.
The process involves the following steps:
– Compression: The incoming warm and moist air is compressed.
– Cooling: The compressed air is cooled, causing the moisture to condense into water.
– Separation: The condensed water is separated and drained, leaving dry air.
Applications
Refrigerated air dryers are widely used in general industrial applications where the required level of dryness is moderate. Common applications include automotive, textile, and fabrication industries.
Desiccant Air Dryer
Working Principle
Desiccant air dryers use adsorption to remove moisture. When the compressed air through a compartment filled with desiccant material, which absorbs the moisture.
The process involves the following stages:
– Adsorption: The compressed air passes through a bed of desiccant material (commonly silica gel or activated alumina), which adsorbs moisture.
– Regeneration: Once the desiccant is saturated, a portion of dry air is diverted to remove the absorbed moisture, regenerating the desiccant.
Applications
Desiccant dryers are employed in applications where extremely dry air is required, such as pharmaceutical manufacturing, electronics, and critical instrument air systems.
Usually, in the food, health, and pharmaceutical industries, desiccant air dryers, oil-free compressors, and stainless steel compressed air tanks are the mainstream options.
More info about the compressed air tank, you can click here to know more: What is The Compressed Air Tank and How to Choose?
Membrane Air Dryer
Working Principle
Membrane air dryers work by passing the compressed air through a series of hollow fibers, where water vapor and contaminants are selectively removed.
These dryers are often used in applications where space is limited and do not require refrigerants for operation.
The process involves:
– Permeation: The membrane allows water vapor to pass through, selectively separating it from the compressed air.
– Discharge: The separated water vapor is discharged, leaving dry air.
Applications
Membrane air dryers are suitable for low-capacity, point-of-use drying. They find applications in laboratories, medical equipment, and other settings where compact and efficient drying is necessary.
Comparison of Different Types of Compressed Air Dryers
Aspect | Refrigerated Air Dryer | Desiccant Air Dryer | Membrane Air Dryer |
Principle | Cools compressed air to remove moisture through condensation. | Uses adsorption (commonly with silica gel or activated alumina) to remove moisture. | Utilizes a permeable membrane to selectively separate water vapor from compressed air. |
Working Stages | Compression, Cooling, Separation | Adsorption, Regeneration | Permeation, Discharge |
Dryness Level | Moderate | Extremely Dry | Moderate (Suitable for low-capacity applications) |
Applications | General industrial (automotive, textile, fabrication) | Critical applications (pharmaceuticals, electronics) | Point-of-use applications (laboratories, medical equipment) |
Maintenance | Relatively Low | Requires periodic replacement of desiccant | Minimal, with no need for desiccant replacement |
Initial Cost | Moderate | High | Moderate (Low for small capacity units) |
Operating Cost | Low | Moderate to High (due to desiccant replacement) | Low |
Space Requirements | Compact | Larger footprint due to multiple vessels for cycling | Compact |
Energy Efficiency | High | Moderate | High |
Flexibility | Suitable for varying demand | Suited for constant or fluctuating demand | Suitable for constant demand |
What Is The Regenerative Desiccant Air Dryer? How Does It Work?
industries.
When compressed air is received, the air dryer processes the air to achieve the conditions required for the application. Compared with refrigerated air dryers, what are the differences between regenerative desiccant air dryers? How does it work?
Components of Compressed Air Dryers
Here are some of the key parts of a compressed air dryer and their functions, let’s take refrigerated air dryer as an example:
Air Filters
Function: Remove particulates, dust, and contaminants from the incoming compressed air.
Importance: Protect downstream components and maintain the quality of compressed air.
Heat Exchanger
Function: Cool the incoming warm and moist air to facilitate moisture condensation.
Importance: Reduces the temperature of the compressed air, allowing for more effective moisture removal.
Refrigeration System
Function: Utilizes a refrigerant to cool and condense moisture in the air.
Importance: Lowers the dew point of the compressed air, preventing condensation in the air distribution system.
Desiccant Bed (In Desiccant Air Dryers)
Function: Adsorbs moisture from the compressed air.
Importance: Particularly relevant in low dew point applications, such as in pharmaceutical or food industries.
Expansion Valves
An expansion valve plays a key role by decreasing the pressure and temperature of the refrigerant, ensuring its readiness for the next evaporating phase.
Evaporator
Function: Evaporates the condensed moisture and returns it to a vapor state.
Importance: Ensures efficient water removal without causing system downtime.
Condensate Drain
Function: Removes collected condensate from the system.
Importance: Prevents the accumulation of water, which can lead to corrosion and compromise air quality.
Air-to-Air Heat Exchanger
Function: Recovers heat from the outgoing air stream to preheat incoming air.
Importance: Increases the overall efficiency of the drying process, saving energy.
Moisture Separator
Function: Further separates moisture from the compressed air after initial cooling.
Importance: Enhances the moisture removal efficiency of the dryer.
Air Pressure Gauges
Function: Monitor and display the pressure levels at various points in the system.
Importance: Helps in diagnosing and addressing issues related to pressure drops or abnormal conditions.
Control System
Function: Regulates the operation of the dryer components.
Importance: Ensures that the dryer adapts to varying air flow and moisture conditions for optimal performance.
Regular inspections, timely replacements, and adherence to recommended maintenance schedules contribute to the longevity and reliability of the system.
How to Choose the Right Compressed Air Dryer
Compressed air dryers are essential components in maintaining the efficiency and longevity of a compressed air system. Selecting the right one for your specific needs involves considering various factors.
Confirm Your Air Quality Requirements
Different applications have varying requirements for air quality. Consider whether your application demands merely dry air or if it requires extremely low dew points for critical processes. This understanding will guide you in choosing between refrigerated, desiccant, or membrane dryers.
Assess the Operating Environment
Factors such as ambient temperature and humidity levels can impact the efficiency of certain dryer types. For instance, refrigerated dryers may struggle in high-temperature environments.
Evaluate the Required Capacity
Determine the flow rate and capacity your system requires. It’s essential to match the dryer’s capacity with that of the air compressor to ensure optimal performance. Consider any potential future increases in air demand when sizing your dryer.
Under the premise of large air consumption, refrigeration air dryers and desiccant air dryers are better choices.
Consider Energy Efficiency
Energy costs are a significant consideration. Refrigerated dryers are generally more energy-efficient than desiccant dryers, but the latter might be necessary for specific applications. Evaluate the long-term operational costs to make an economically sound decision.
Factor in Maintenance Requirements
Each type of compressed air dryer comes with its maintenance needs. Refrigerated dryers usually have lower maintenance requirements compared to desiccant dryers. Consider your team’s expertise and available resources for maintenance tasks.
Think About Installation Space
Refrigerated dryers are often compact and suitable for confined spaces, while desiccant dryers may require more room. Evaluate whether a dryer can be installed at the point of use or if it needs to be centrally located.
Compressed Air Dryer Common Faults
Compressed air dryer is a critical process in ensuring the quality and efficiency of various industrial applications. However, like any system, compressed air dryers can encounter faults that affect their performance.
- Moisture Carryover
Issue: Moisture in the compressed air lines.
Solution: Check and replace faulty desiccant beds in desiccant dryers. Ensure proper maintenance of condensate drains and separators.
- Pressure Drop
Issue: Unintended reduction in compressed air pressure.
Solution: Clean or replace clogged filters. Ensure the correct sizing of the dryer for the compressed air system.
- Excessive Energy Consumption
Issue: Higher-than-expected energy bills.
Solution: Regularly clean or replace air filters. Consider upgrading to a more energy-efficient compressed air dryer.
- Overheating
Issue: Elevated temperatures in the dryer.
Solution: Check for proper ventilation around the dryer. Ensure that the ambient temperature matches the specified operating conditions.
- Contaminant Buildup
Issue: Accumulation of contaminants in the dryer, affecting performance.
Solution: Regularly clean and inspect dryers for contaminants. Install proper filtration systems upstream of the dryer.
- Incorrect Dew Point
Issue: Dew point higher than the specified level.
Solution: Inspect and replace desiccant beds in desiccant dryers as needed. Check for air leaks and repair them promptly.
- Oil Carryover
Issue: Presence of oil in the dried compressed air.
Solution: Install and maintain proper filtration, including coalescing filters. Regularly monitor and service oil removal systems.
- System Leaks
Issue: Air leaks in the compressed air system.
Solution: Conduct regular leak detection audits. Repair leaks promptly to maintain system efficiency.
- Incorrect Sizing
Issue: Undersized or oversized dryer for the compressed air system.
Solution: Ensure proper sizing during the initial installation. Consider system expansion or changes in demand over time.
- Faulty Controls
Issue: Malfunctioning control systems affecting dryer operation.
Solution: Regularly inspect and calibrate control systems. Update software if applicable.
The above are some common faults of compressed air dryers and preliminary solutions. In actual compressed air system operation, the situation is often much more complicated.
So, regular inspections, coupled with a thorough understanding of the specific dryer type in use, can significantly enhance the reliability of the entire compressed air system.
Top Industrial Refrigerated Compressed Air Dryer Manufacturers Checklist
Ingersoll Rand
Atlas Copco
Kaeser Compressors USA
Gardner Denver
BOGE
Chicago Pneumatic
Quincy
SMC Corporation
Schulz
etc.
Click to learn more.