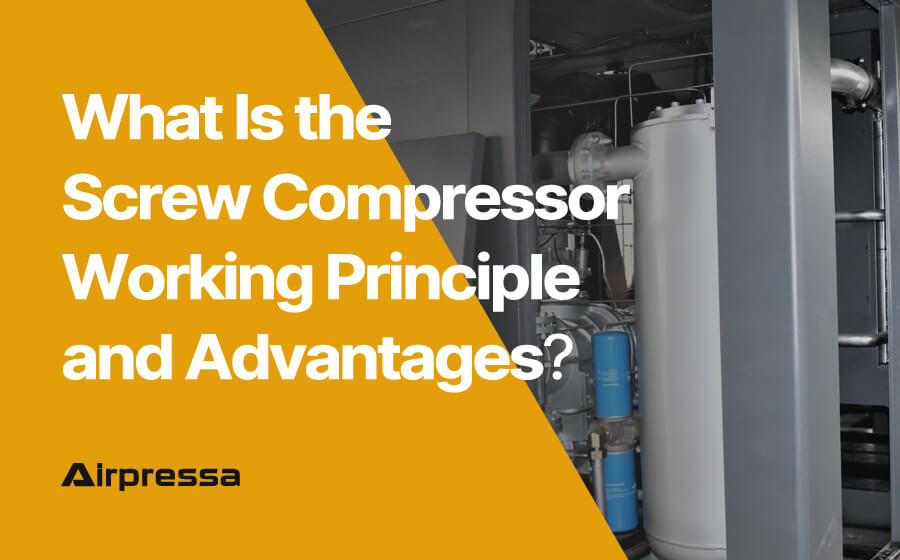
The screw compressor is a critical utility in many industries, powering a wide range of applications such as pneumatic tools, manufacturing processes, and transportation systems. Its unique working principle, high efficiency, and versatility make it a preferred choice in these industries.
In this article, we will delve deeper into the working principle, advantages, structure, and troubleshooting of screw compressors, providing valuable insights for those considering this technology for their compressed air needs.
You can click on any section that you interest to get there quickly.
What Is the Screw Compressor?
The screw compressor is a type of positive displacement air compressor that uses two helical rotors to compress the air.
There are some main types of screw compressors:
- Oil-lubricate screw sompressor
- Oil-free screw sompressor
- 2-stage screw compressor
- Fixed speed screw compressor
- Variable speed screw compressor
- Low pressure screw compressor
Oil-injected screw compressors use oil to lubricate the moving parts and cool the compressed air, while oil-free screw compressors rely on other methods, such as water or air cooling, to achieve the same results.
Oil-free screw compressors are typically more expensive than oil-injected models, but they are often preferred in applications where oil contamination is a concern, such as in the food and beverage industry.
The variable speed screw air compressor saves more energy and reduces the electricity bill of the enterprise.
Screw Compressor Working Principle
The screw compressor’s two rotors rotate in opposite directions, they operate on the principle of “screw and lock,” where the male and female rotors interlock to trap and compress air as they rotate.
As the rotors rotate, the volume between them decreases, causing the air to be compressed. The compressed air is then discharged through a valve at the end of the compressor. The process is continuous, and the air is compressed at a constant rate, resulting in a steady flow of high-pressure air.
This unique design allows screw compressors to deliver a continuous supply of compressed air with minimal pulsation and vibration.
Key Components of the Screw Air Compressor
A complete screw air compressor is mainly composed of the following parts:
Rotors
The rotor pair is the heart of the screw compressor.
A screw air compressor features two rotors, typically helical in shape, that intermesh to create compressed air. The rotors rotate in opposite directions, trapping and compressing air between them.
Casing
The casing houses the rotor pair and ensures that the air is compressed without leaking out. The casing is usually made of cast iron or steel and is designed to withstand high pressures.
Inlet and Outlet Ports
The inlet and outlet ports are the entry and exit points for the compressed air. The inlet port allows air to enter the compressor, while the outlet port allows compressed air to exit.
Bearings
The bearings support the rotor shafts and ensure that the rotors rotate smoothly and without friction. The bearings are usually made of high-strength materials such as bronze or ceramic.
Oil Separator
The oil separator separates the oil from the compressed air, ensuring that the air is free of contaminants.
Oil system
Screw air compressors rely on oil to lubricate the rotors, reduce friction and prevent overheating. The oil system includes an oil cooler, oil filter, oil pump, and oil separator.
Drive system
The drive system transfers power from an electric motor or engine to the rotors. It typically consists of a V-belt, coupling, or direct drive system.
Control system
Screw air compressors feature advanced control systems that regulate pressure, temperature, and flow rate to ensure optimal performance and energy efficiency.
After-cooler
After the air is compressed, it is typically hot and moist. An after-cooler cools the compressed air and removes moisture before it enters the distribution system.
Air receiver tank
The air receiver tank is a vital component that stores compressed air and provides a steady supply to downstream equipment.
Air dryer
Air dryers are optional components that remove moisture from compressed air, improving the quality of the air and protecting downstream equipment.
Safety valves
Safety valves are critical components that prevent over-pressurization of the compressor, protecting the equipment and personnel from harm.
Regular maintenance and inspections can help identify and address any issues with these components, ensuring safe and reliable operation.
The Importance of Proper Lubrication
Lubrication plays a critical role in the functioning of a screw compressor. It is essential to ensure that the compressor operates smoothly and efficiently. Lubrication reduces friction between moving parts, minimizes wear and tear, and prevents overheating.
Choosing the Right Lubricant
Different compressors require different types of oils, depending on their design, operating conditions, and the type of gas being compressed. Using the wrong lubricant can lead to reduced efficiency, increased wear and tear, and even compressor failure.
It is worth mentioning that at present, the oil-free air compressor are becoming more and more popular. It can reduce the risk of oil pollution in production.
Oil-free screw air compressors mainly include:
- Dry oil-free screw air compressor
- Water-lubricated screw air compressor
The oil-free screw air compressor is suitable for prevention industries, pharmaceutical industry, food industry, and textile industry.
Regular Maintenance
Regular maintenance is necessary to ensure that the compressor is operating correctly and efficiently. The oil in the compressor needs to be changed regularly, and the oil filters need to be replaced.
The air compressor also needs to be inspected for leaks, worn parts, and other issues that can affect its performance.
You can check this article for more details: Air Compressor Maintenance Checklist: The Ultimate Manual
Advantages of Screw Air Compressors
Screw air compressors have become a popular choice for many industries due to their high efficiency and reliability. These compressors have numerous advantages over other types of air compressors, making them an ideal choice for many applications.
High Efficiency
One of the main advantages of screw air compressors is their high efficiency. These compressors use a rotary screw mechanism to compress the air, which is much more efficient than the reciprocating mechanism used by other types of compressors.
Energy Saving
Screw air compressors have built-in energy-saving features, such as variable speed drives and energy recovery systems. These features allow the compressor to adjust its output based on the air demand, reducing energy consumption and operating costs.
Lower Cost of Ownership
Overall, screw air compressors have a lower cost of ownership than other types of compressors. These compressors require less maintenance, have a longer lifespan, and produce higher-quality air. This translates to lower operating costs and a better return on investment.
Low Maintenance
Another advantage of screw air compressors is their low maintenance requirements. Screw compressors have fewer moving parts than other types of compressors, which means they require less maintenance and have a longer lifespan.
Additionally, screw compressors have fewer oil-related issues, reducing the need for oil changes and minimizing the risk of oil contamination.
Continuous Operation
Screw air compressors can operate continuously, which is a significant advantage in applications that require a constant supply of compressed air.
These compressors do not need to shut down for cooling, which reduces downtime and also increases productivity.
Quiet Operation
Screw air compressors operate quietly, which is important in environments where noise levels need to be minimized.
Compared to reciprocating compressors, screw compressors produce less vibration and noise, making them ideal for applications where noise pollution is a concern.
High Reliability
Screw air compressors are known for their high reliability. These compressors have a simple design with fewer moving parts, which means they are less prone to mechanical failure. This makes them an ideal choice for critical applications where downtime is not an option.
Versatile Applications
Screw air compressors are suitable for a wide range of applications. They can be used in industries such as automotive, food and beverage, manufacturing, and pharmaceuticals
Besides, screw compressors can handle a variety of compressed air demands, from low-pressure applications to high-pressure applications.
Better Air Quality
Screw air compressors produce high-quality air due to their oil-injected design. The oil used in these compressors helps lubricate the internal components and remove contaminants from the compressed air, resulting in cleaner air.
Easy Installation
Screw air compressors are easy to install and require minimal infrastructure. These compressors can be installed in a variety of locations, including on the production floor, outside, or in a separate compressor room.
Screw compressors are available in various sizes and configurations, making it easy to find the right compressor for your application.
Troubleshooting for Screw Compressors
Like all machines, the screw air compressor can experience problems that require troubleshooting, such as:
Overheating
Overheating is a common problem with screw air compressors. It can be caused by a variety of factors, including low oil levels, dirty oil filters, or clogged radiators.
To troubleshoot this issue, first, check the oil levels and oil filters. If they are low or dirty, replace them. If this does not resolve the issue, check the radiator for dirt or debris. If it is clogged, clean it or replace it.
Air Leakage
Air leakage can cause a drop in system pressure and reduce the efficiency of the compressor. This issue can be caused by a variety of factors, including damaged hoses or fittings, worn gaskets, or loose connections.
You can check all hoses and fittings for damage or wear. If any are damaged, replace them. If the connections are loose, tighten them.
Sometimes, the gaskets for wear and replace if necessary.
High Oil Consumption
High oil consumption is another common issue with screw air compressors. It can be caused by a variety of factors, including worn piston rings, clogged oil filters, or high oil temperatures.
To troubleshoot this issue, start by checking the oil filters and replacing them if they are clogged.
And it may also be due to two other failures:
The oil temperature. If it is too high, the oil cooler may need to be cleaned or replaced.
The piston rings wear.
Excessive Vibration
Excessive vibration can be caused by a variety of factors, including misaligned couplings, worn bearings, or loose bolts.
Usually, will check the couplings for alignment, they should be aligned. Or check whether the bearings are worn or the bolts are loose.
Electrical Issues
Electrical issues can cause a variety of problems with screw air compressors, including motor failure, blown fuses, or tripped circuit breakers.
You can check the power supply and the circuit breakers, or contact an electrician to check.
A worse reason is that the motor is damaged, then you need to spend a lot of money to replace the new motor.
Key Factors to Choosing A Screw Compressor
A screw compressor is an investment that can have a significant impact on the productivity and efficiency of your operations. Here are some important factors to keep in mind when selecting a screw compressor.
Air demand and pressure requirements
One of the most important factors to consider when selecting a screw compressor is the air demand and pressure requirements of your application. Make sure the compressor you choose can provide the right amount of air pressure and flow rate for your needs.
What is CFM compressor and how to calculate CFM?
Energy efficiency
Screw compressors can be energy-intensive, so it’s important to choose a compressor that is energy efficient. Look for models that have high-efficiency motors and are equipped with features like variable speed drives that can help reduce energy consumption.
Reliability
The reliability of a compressor is critical to the smooth operation of your business. Look for models that are built with high-quality components and are designed to operate efficiently and reliably over a long lifespan.
Maintenance requirements
Regular maintenance is essential to keep your compressor operating at peak efficiency. When selecting a screw compressor, consider the maintenance requirements of the unit and make sure you have the resources and expertise to keep the compressor in good working order.
Size and footprint
The size and footprint of the compressor are important considerations, particularly if you have limited space in your facility. Make sure the compressor you choose fits your available space and can be installed without interfering with other operations.
Cost
Screw compressors can be a significant investment for your business. So, it’s important to consider the cost of the unit and the potential return on investment. Look for models that provide the right balance of performance, reliability, and cost-effectiveness.
Import screw air compressors from Germany and the United States, and you can also purchase screw air compressors from China to get reliable and most cost-effective machines.
You can read this article: How to Source Rotary Screw Air Compressors? The Ultimate Guide
After-sales support
Finally, consider the after-sales support provided by the manufacturer or distributor. Make sure you have access to a reliable support team that can help you with any issues or questions that arise after the purchase.
By considering these key factors when choosing a screw compressor, you can select a unit that meets your specific needs and provides reliable, efficient performance for years to come.
FAQ
Q: How does a VSD screw compressor control capacity?
A: A screw air compressor controls capacity by using a built-in variable frequency drive (VFD) that adjusts the speed of the compressor motor to match the air demand. This allows the compressor to operate more efficiently and saves energy.
Q: What is the maximum pressure for a screw air compressor?
A: The maximum pressure for a screw air compressor can vary depending on the specific model and manufacturer. However, most screw compressors are capable of producing pressures up to 200 psi.
Q: How many hours does a screw compressor last?
A: The lifespan of a screw compressor can vary depending on several factors such as usage, maintenance, and environmental conditions. However, with proper care and maintenance, a screw compressor can last for tens of thousands of hours before requiring major repairs or replacement.
Q: Does a screw compressor run continuously?
A: Screw compressors can be designed to run continuously, but it’s not always necessary. With the use of a variable frequency drive (VFD), a screw compressor can adjust its speed and output to match the air demand. This means the compressor can stop and start as needed, leading to energy savings and longer equipment lifespan.
Q: What is the normal temperature for a screw compressor?
A: The normal operating temperature for a screw compressor typically ranges from 160°F to 200°F (70°C to 93°C). However, this can vary depending on the specific model and manufacturer, so it’s important to refer to the manufacturer’s specifications for more precise information.
Q: Why are screw compressors so expensive?
A: Screw compressors are generally more expensive than other types of compressors due to their design and complexity. They are designed to operate at high efficiency levels and require high-quality materials and manufacturing processes. Additionally, they often include advanced features such as built-in VFDs and advanced control systems, which contribute to the higher cost.
And the oil-free screw air compressors are more expensive than lubricated screw air compressors.
Q: Is a screw compressor better than a piston compressor?
A: Similar to the previous question, the choice between screw and piston compressors depends on the specific application and needs of the user. Screw compressors are generally better suited for larger applications with higher air demand, while piston compressors are better suited for smaller applications with lower air demand. Additionally, screw compressors tend to be more energy-efficient and require less maintenance than piston compressors, but they are also more expensive.